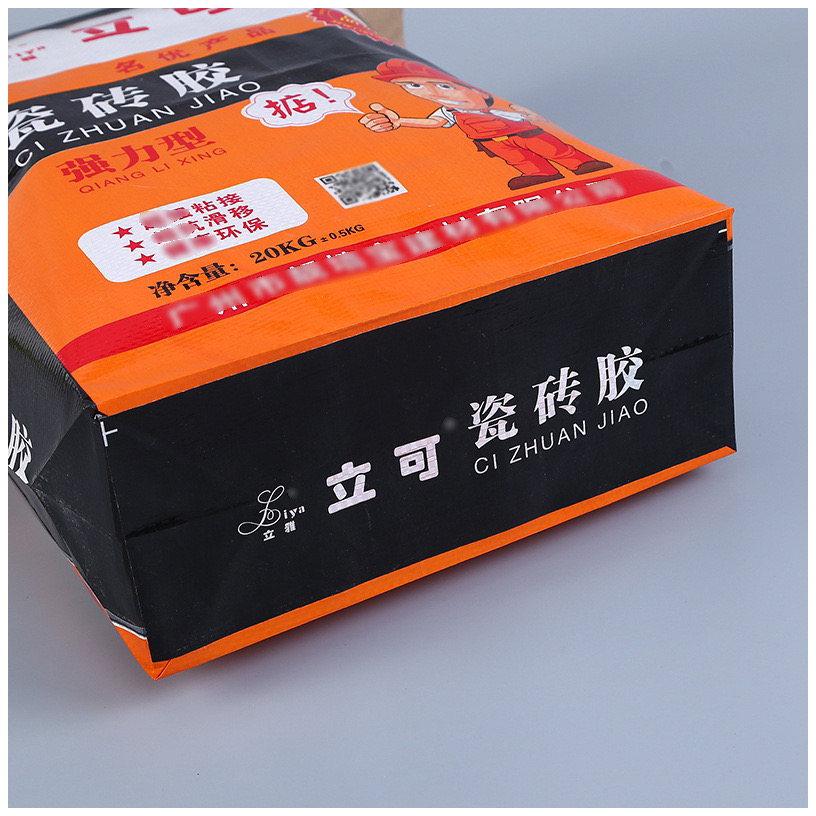
Poly woven bags, commonly known as Poly Fabric Sacks or Poly Fabric Bags, are integral to packaging solutions across various industries due to their lightweight, durable, and cost-effective nature. These bags are made from woven polypropylene (PP) fibers, creating a sturdy structure that holds up against the rigors of handling, storage, and transport. At the forefront of this technological revolution are Starlinger and W&H, two leading manufacturers of the high-tech machinery that makes it all possible. Through their cutting-edge equipment, the durability and flexibility of woven polypropylene bags have reached new heights, especially when considering the influence of the draw-twist process and high automation in production.
The Draw-Twist Process: Enhancing Durability and Flexibility
The draw-twist process is central to improving the mechanical properties of poly woven bags. During this process, polypropylene fibers are drawn and twisted, creating a more compact and strong yarn that increases the strength and flexibility of the final product. This enhanced durability is critical for industries that require robust packaging, such as construction, agriculture, and food.
In addition, the draw-twist process helps to prevent elongation under load, ensuring the bags maintain their shape and integrity under stress. These bags exhibit high tensile strength, tear resistance, and elongation capacity—key characteristics for a variety of applications, including bulk packaging, grain storage, and transportation of heavy goods. The poly fabric sacks produced through this process remain pliable, offering the necessary flexibility without sacrificing strength.
The use of Starlinger technology in the draw-twist process is especially crucial. With precision-controlled machinery, Starlinger ensures that every yarn is of consistent thickness and strength, delivering a high-quality product that consistently meets the demanding standards of the market. Additionally, W&H’s advanced extrusion equipment further optimizes the production of these bags by ensuring uniformity and superior quality control in the woven fabric.
High Automation and Increased Efficiency
Automation in the manufacturing process has played a pivotal role in enhancing the overall quality and efficiency of poly woven bags. With the integration of Starlinger and W&H machinery, production lines now boast automation capabilities that can reach line speeds exceeding 200 pieces per minute. This high-speed automation facilitates faster production cycles, helping manufacturers meet global demands while ensuring each bag is made with precision.
The multi-machine linkage feature, available in Starlinger and W&H systems, allows for simultaneous coordination of various machines, increasing production efficiency and minimizing downtime. The ability to monitor and adjust settings automatically throughout the production process ensures the consistency of each woven bag. This level of automation is particularly beneficial in large-scale operations, as it enhances productivity while also reducing human error.
This high degree of automation translates into cost savings for manufacturers. By reducing labor costs and minimizing waste, the manufacturing process becomes more sustainable, allowing businesses to offer more competitive prices while maintaining product quality. Moreover, the enhanced production efficiency provides an edge in terms of meeting the increasing demand for woven polypropylene bags in international markets.
Product Features and Parameters of Poly Woven Bags
The performance of poly woven bags is determined by various parameters that are influenced by the manufacturing process. Key parameters include:
Parameter | Description |
---|---|
Material | Polypropylene (PP), offering high strength and resistance to weather conditions. |
Tensile Strength | High resistance to stretching, which is ideal for packaging heavy materials. |
Tear Resistance | Ability to withstand tearing under pressure, making it durable during transportation and handling. |
Flexibility | Bags retain flexibility even under heavy load, preventing cracks or breaks. |
Weight | Lightweight compared to other packaging materials like paper or jute. |
Customization | Customization in printing, colors, and sizes for brand-specific solutions. |
Capacity | Varies depending on bag size; commonly used in capacities ranging from 10 kg to over 100 kg. |
UV Resistance | Improved UV resistance, preventing degradation from exposure to sunlight. |
These characteristics, made possible by Starlinger and W&H technology, ensure that woven polypropylene bags serve a wide range of applications. Whether used for bulk packaging in the agricultural sector, the chemical industry, or as poly fabric sacks for cement packaging, their reliability remains unmatched.
FAQs
- What are the primary applications for Poly Woven Bags? Poly Woven Bags are commonly used in industries such as agriculture, construction, food packaging, and chemicals. Their durable and flexible nature makes them ideal for storing and transporting goods like grains, seeds, chemicals, and building materials.
- How do Starlinger and W&H contribute to the quality of Poly Woven Bags? Starlinger and W&H offer state-of-the-art equipment that improves the strength, flexibility, and production efficiency of woven polypropylene bags. Their machinery ensures precise manufacturing, enhancing product quality while optimizing production speed.
- Are Poly Fabric Sacks recyclable? Yes, Poly Fabric Sacks made from polypropylene are recyclable. The material is reusable and can be processed into new products, reducing environmental impact.
- Can Poly Woven Bags be customized? Absolutely. Poly Woven Bags can be customized in terms of size, color, design, and even printing. This makes them a versatile solution for packaging across different industries.
- What are the benefits of using Poly Fabric Sacks for bulk packaging? The primary benefits include their durability, strength, and cost-effectiveness. They are designed to withstand heavy loads and rough handling while being flexible enough to adapt to various storage and transport needs.
The Role of Technology in the Evolution of Poly Woven Bags
The evolution of woven polypropylene bags can be traced back to the advancements in manufacturing technologies, particularly with the introduction of Starlinger and W&H equipment. These companies have played a critical role in revolutionizing the packaging industry by offering innovative, high-performance machinery that significantly improves the efficiency, durability, and flexibility of poly fabric sacks.
The machines used in the production process, such as circular looms, extrusion lines, and printing machines, allow for mass production without compromising quality. With a line speed that can exceed 200 pieces per minute and the ability to automate several processes, manufacturers can produce large quantities of woven polypropylene bags quickly, ensuring that global supply chains are met with timely and reliable solutions.
This technological progress aligns with industry demands for both functional performance and sustainability. As businesses seek to reduce costs, improve efficiency, and meet environmental standards, Starlinger and W&H remain at the forefront of packaging innovations.
For further information on how poly woven bags are used in various industries and how their durability and flexibility are enhanced by advanced technologies, you can explore these detailed articles:
- The Versatility and Benefits of Poly Woven Bags
- Enhancing Packaging Solutions with Poly Fabric Sacks
In conclusion, the incorporation of advanced technology by Starlinger and W&H into the manufacturing process of poly woven bags has dramatically enhanced the quality, durability, and flexibility of these packaging solutions. Their influence not only increases production efficiency but also ensures that these bags remain reliable for a wide range of applications.