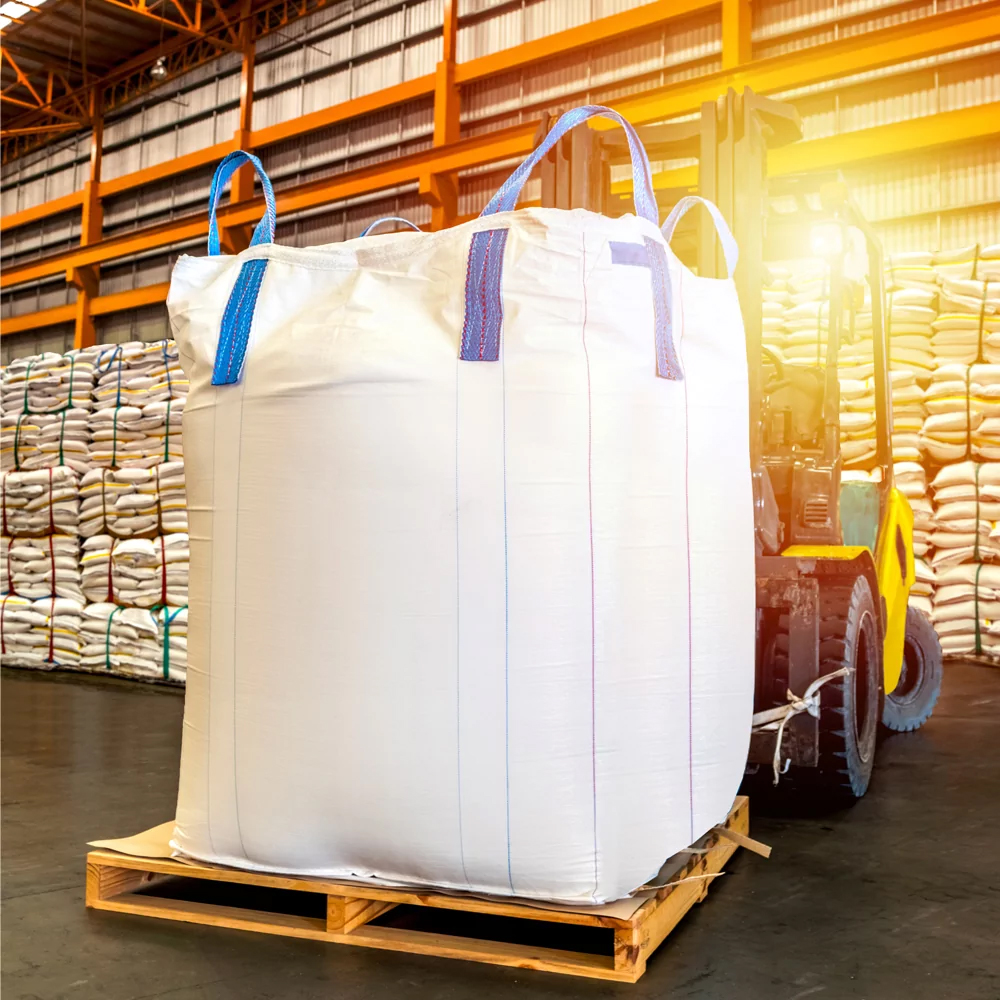
When it comes to packaging solutions, especially for bulk goods, Anti-Bulge FIBC bags, also known as Bulk bags, Ton bags, or Jumbo Bags, have become an essential part of modern industrial packaging. These bags are designed to store and transport heavy materials safely and efficiently. However, to achieve optimal performance, certain quality standards must be met during both the design and material selection stages.
In this article, we will explore two key aspects of FIBC bag manufacturing that significantly enhance their strength and reliability: how Anti-Bulge FIBC bags help increase the bag’s weight capacity, preventing bursting or bulging, and how PP (Polypropylene) and PE (Polyethylene) granules undergo rigorous quality testing to ensure that the bags’ integrity is maintained from the start of the manufacturing process.
Part 1: Anti-Bulge FIBC Bags and How They Prevent Bag Failure
The strength and reliability of FIBC bags depend on several factors, including the construction, design, and materials used in their production. One of the most critical innovations in the design of Bulk bags is the introduction of Anti-Bulge FIBC bags.
What are Anti-Bulge FIBC Bags?
Anti-Bulge FIBC bags are specially engineered to prevent the bag from bulging when filled with heavy or irregularly shaped materials. Unlike traditional FIBC bags, which can expand outwards under pressure, Anti-Bulge bags feature a design that minimizes this expansion, ensuring better load distribution and preventing the bags from becoming unstable.
Key Features of Anti-Bulge FIBC Bags
- Enhanced Load Distribution: These bags are designed to distribute the weight evenly across the bag’s surface. This reduces the strain on any one part of the bag, preventing overstretching or rupture.
- Prevention of Bulging: Traditional FIBC bags may bulge outward when packed with irregularly shaped items or heavy materials, leading to instability and possible bag failure. Anti-Bulge bags are specifically designed to resist this outward expansion, thus maintaining the shape and integrity of the bag.
- Increased Weight Capacity: By preventing bulging, Anti-Bulge bags can handle higher weights without compromising safety. This makes them ideal for transporting heavy materials such as cement, sand, and chemicals.
- Durability: The robust construction of Anti-Bulge FIBC bags allows them to withstand the physical stress exerted during loading, transport, and unloading, reducing the likelihood of damage.
The Benefits of Using Anti-Bulge FIBC Bags
The primary advantage of Anti-Bulge FIBC bags is their ability to handle larger and heavier loads without compromising safety. By preventing bulging, they reduce the risk of bag failure, which could lead to material loss or contamination.
Other benefits include:
Feature | Benefit |
---|---|
Increased Stability | Reduced bulging leads to improved stability during transportation and storage. |
Higher Load Capacity | More effective distribution of weight allows the bags to carry larger loads. |
Cost Efficiency | Fewer bag failures mean less waste and better overall cost-effectiveness. |
Improved Safety | Minimizes the risk of bag rupture, which could cause hazardous spills. |
For more details about how Anti-Bulge FIBC bags can improve your bulk packaging solutions, check out this article on the advantages of Anti-Bulge FIBC bags.
Part 2: Quality Control in PP and PE Granules
To ensure that FIBC bags perform as expected, the raw materials used in their production must meet high-quality standards. PP (Polypropylene) and PE (Polyethylene) granules are the primary materials used in the manufacturing of woven fabric for FIBC bags. These materials must undergo several tests to guarantee their quality, strength, and durability.
Key Quality Tests for PP and PE Granules
To produce high-performance Jumbo bags and other Bulk bags, PP and PE granules undergo the following quality tests:
- Visual Inspection
- Purpose: Ensures that the granules are free from visible contaminants, color inconsistencies, or defects.
- Process: The granules are inspected under various lighting conditions to check for any impurities that may affect the final product’s appearance or functionality.
- Melt Flow Index (MFI)
- Purpose: Measures the flow rate of the melted polymer, which indicates its viscosity and ease of processing.
- Process: The MFI test is carried out by heating the PP or PE granules and measuring how much material flows through a standard die under specific conditions. A higher MFI indicates a lower molecular weight and faster processing time.
- Density
- Purpose: Determines the compactness of the polymer material.
- Process: The density of the granules is tested by calculating the ratio of mass to volume. Higher density materials tend to be stronger and more durable, making them ideal for heavy-duty packaging applications.
- Tensile Strength and Elongation at Break
- Purpose: These tests measure the material’s strength and its ability to stretch before breaking.
- Process: Granules are stretched until they break, and the results help determine the flexibility and strength of the final woven fabric.
- Thermal Performance
- Purpose: Ensures that the granules can withstand high temperatures without degrading.
- Process: The granules are exposed to elevated temperatures to test their resistance to heat. This is important for applications that involve transporting materials exposed to high heat.
- Chemical Resistance
- Purpose: Tests the material’s ability to resist degradation when exposed to various chemicals.
- Process: Granules are tested for exposure to acids, alkalis, and solvents, ensuring that the woven fabric will remain intact even in harsh environments.
- UV Resistance
- Purpose: Measures the material’s resistance to ultraviolet light, which can cause degradation over time.
- Process: Granules are exposed to UV radiation to simulate long-term exposure to sunlight. This is essential for bags used in outdoor applications where UV exposure is inevitable.
The Importance of Quality Control in Granule Selection
The quality of PP and PE granules directly impacts the overall performance of the FIBC bags. If the granules do not meet stringent quality standards, the bags may fail to withstand the rigors of transportation, handling, or exposure to harsh environmental conditions. Ensuring the quality of these granules is crucial to producing durable, safe, and effective Ton bags and Jumbo Bags.
FAQs About Anti-Bulge FIBC Bags and Granule Quality Testing
- What is an Anti-Bulge FIBC bag?
- An Anti-Bulge FIBC bag is a type of Bulk bag designed to prevent bulging and enhance load distribution, allowing it to carry heavier and more stable loads.
- How does Anti-Bulge technology increase the bag’s weight capacity?
- By preventing bulging, the weight is distributed more evenly across the bag, reducing strain on any single point and allowing it to hold larger loads safely.
- Why is the quality of PP and PE granules so important in FIBC bags?
- The quality of the granules directly influences the strength, flexibility, and durability of the finished bags. Higher-quality granules result in stronger, more reliable bags.
- What is the MFI test and why is it important?
- The Melt Flow Index (MFI) measures the flow rate of melted polymer. It helps determine how easy it is to process the material and ensures that the granules will produce consistent and strong FIBC bags.
- How long do Anti-Bulge FIBC bags last?
- With proper care, Anti-Bulge FIBC bags can last for years, especially if they are made from high-quality PP or PE granules that have undergone rigorous testing.
For more details about Bulk bags and how we ensure quality from the start to the finish, refer to this comprehensive guide on Bulk bags and their applications.
Conclusion
In conclusion, the development of Anti-Bulge FIBC bags has revolutionized the way bulk materials are transported and stored. With advancements in design and materials, these bags can handle larger weights and more complex loads while ensuring safety and stability. At the same time, the stringent quality testing of PP and PE granules ensures that the bags are made from durable, high-performance materials, providing customers with a reliable and cost-effective packaging solution. Whether you are looking for Ton bags, Jumbo Bags, or Bulk bags, choosing the right materials and design is key to optimizing performance and longevity.