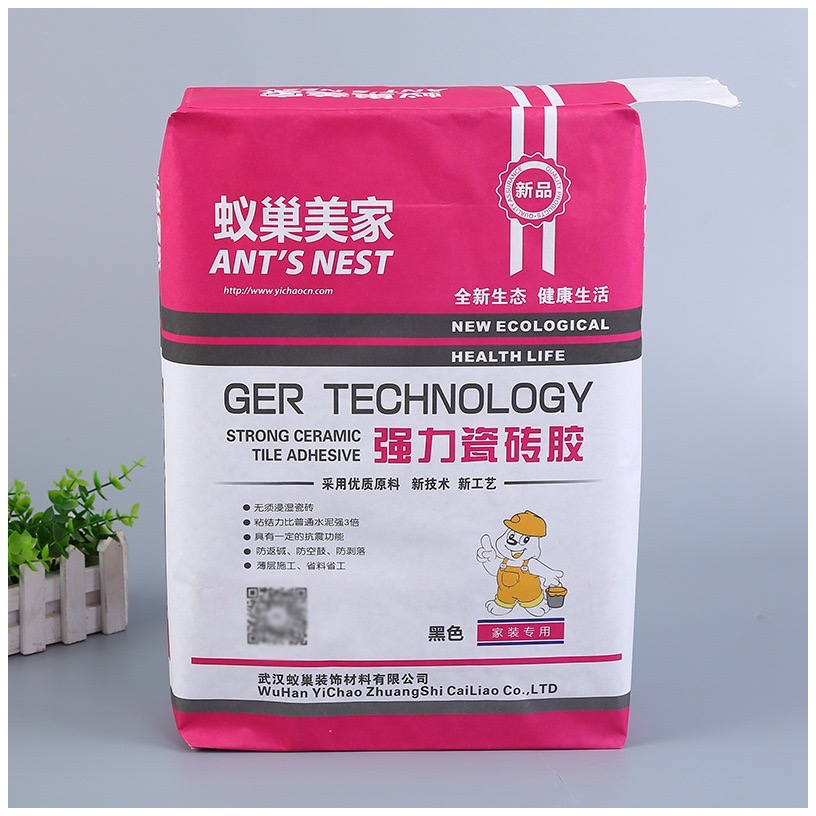
- 1. Differences Between Moisture Proof Woven Bags and Waterproof Woven Bags
- 2. Technical Advantages: Strength, Abrasion, Tear Resistance
- 3. Conversation Snippet
- 4. Product Parameters Table
- 5. FAQs
- 6. Environmental and Economic Benefits of Recyclable PP
- 7. Forward-Looking Trends: Infrastructure and Circularity
- 8. Illustrative Examples
- 9. Conclusion
Main Answer: Moisture Proof Woven bags—including Moisture Proof Woven sacks, Moisture Proof PP Bags, and multi-wall woven bags—primarily shield contents from ambient humidity or mild dampness, whereas Waterproof Woven Bags excel at preventing direct water penetration (e.g., rainfall or water immersion). Whether you need a moderate anti-humidity barrier or a fully water-blocking solution depends on the level of exposure your product faces. Notably, both bag types incorporate woven polypropylene (PP)—a strong, recyclable material that meets environmental goals and performance standards. As global packaging studies (2026) show a 5–6% yearly rise in PP sack demand, product designers are increasingly adopting closed-loop recycling strategies and exploring biodegradable coatings to boost sustainability.
Below, we explore the technical distinctions between moisture-proof and waterproof woven PP sacks, examine how each addresses humidity and water challenges, and consider the social-economic rewards of using recyclable PP. We also delve into developing trends like integrated recycling infrastructure and biodegradable polymer research, highlighting how these packaging advancements align with market priorities for product safety, brand image, and eco-friendly progress.
1. Differences Between Moisture Proof Woven Bags and Waterproof Woven Bags
1.1 Moisture Proof Woven Bags
- Focus: Controlling internal moisture (condensation, ambient humidity).
- Lamination: Typically lighter or partial to maintain breathability.
- Best Suited For: Grains, cereals, or items needing dryness but not immersed in liquid.
Example: A cereal exporter discovered that Moisture Proof Woven sacks with moderate PE lamination drastically reduced clumping across humid warehouse conditions, avoiding the heavier cost of full waterproofing.
1.2 Waterproof Woven Bags
- Focus: Preventing actual water contact (rainfall, splashes, partial immersion).
- Construction: Thicker lamination and sealed seams for full barrier protection.
- Best Suited For: Products shipped in rainy ports or near aquatic environments (fish feed, certain chemicals).
Example: A fishmeal distributor adopted robust Waterproof Woven Bags, heat-sealing bag edges to avert water intrusion, thus ensuring product consistency despite frequent dockside handling.
1.3 Deciding Which Is More Functional
- Moisture Proof: Sufficient if your product faces mild humidity risk rather than direct water exposure.
- Waterproof: Vital if your supply chain involves heavy rainfall, splash risks, or marine transport.
2. Technical Advantages: Strength, Abrasion, Tear Resistance
2.1 Woven PP Fabric Strength
Polypropylene tapes yield:
- High Tensile Integrity: Minimizes tears from forklift friction or stacking pressure.
- Abrasion Resistance: Long-lasting under repetitive movement or contact with rough surfaces.
Example: A large fertilizer plant integrated multi-wall Moisture Proof PP Bags with laminated exteriors, reducing scuff-related ruptures by 15% while maintaining minimal bag replacement costs.
2.2 Barrier Performance: Moisture vs. Water
- Moisture Proof: Targets ambient or internal condensation; partial lamination is often enough.
- Waterproof: Uses heavier coating or multi-layer lamination, plus sealed closures to avoid water infiltration.
Example: A feed exporter shipping in monsoon conditions found a fully Waterproof Woven Bags approach essential to block direct rains, while a simpler moisture-proof design sufficed in dry climates.
2.3 Tear and Durability
- Multi-Layer Weaves: Some designs incorporate 2–3 plies, strengthening load capacity up to 50 kg.
- Sewn or Heat-Sealed Seams: Minimizes leakage points for powders or granular goods.
Example: A plaster manufacturer introduced 90 gsm multi-layer sacks with sealed edges to withstand forklift compressions, cutting spillage and end-customer complaints.
3. Conversation Snippet
Topic: Optimal Choice for Seasonal Shipping
Question: “Should we shift to Waterproof Woven Bags for rainy months even though we usually use Moisture Proof Woven sacks?”
Answer: “If your shipments encounter direct rainfall, fully Waterproof Woven Bags are safer. However, if conditions only require controlling humidity, Moisture Proof PP Bags remain cost-effective while ensuring dryness. Assess the shipping environment for rainfall exposure versus mild moisture risk.”
4. Product Parameters Table
Parameter | Typical Range/Value | Influence on Performance |
---|---|---|
Fabric GSM | 60–120 | Balances tear strength & shipping cost |
Lamination | PE / BOPP (thin to thick) | Dictates moisture vs. full water barrier |
Inner Liner | Optional (PE, specialized) | Critical for dust-laden or fine powders |
UV Stabilizer | 150–300 kLy (if needed) | Preserves color & bag integrity under sunlight |
Bag Capacity | 5–50 kg (common) | Adapts to feed, cereals, chemicals, or construction materials |
Closure Method | Sewn / Heat-Sealed / Valve | Affects dust control, water ingress, user convenience |
Printing Options | Flexo / Gravure / Digital | Showcases brand identity, product data, compliance labels |
5. FAQs
- Q: Are Moisture Proof Woven sacks enough for wet climates?
A: They suffice for moderate humidity but not necessarily for heavy downpours. If direct water contact is probable, opt for fully Waterproof Woven Bags. - Q: Do Moisture Proof PP Bags handle fine powders well?
A: Yes. Adding a liner or using multi-layer lamination prevents dust leaks, preserving product dryness in stable warehouse conditions. - Q: Why is woven PP favored over standard plastic films?
A: Woven PP achieves higher tear resistance, is reusable or recyclable (#5), and allows advanced printing for brand or safety instructions. - Q: Does heavy lamination hamper bag recyclability?
A: Some specialized lamination layers need extra steps in recycling, but many plants can still process them effectively if adhesives are used responsibly. - Q: Are both moisture- and waterproof sacks suitable for hot or sunlit storage?
A: Yes, but consider UV stabilizers or thicker lamination if exposed to strong UV for extended periods.
6. Environmental and Economic Benefits of Recyclable PP
6.1 Eco-Friendly Design
Both Moisture Proof Woven Bags and Waterproof Woven Bags typically use polypropylene:
- Recyclable: PP (#5) can be processed at many recycling facilities.
- Closed-Loop Initiatives: Brands increasingly collect used sacks for reprocessing into new products.
Example: A coffee exporter developed a return-and-recycle scheme for partially laminated sacks, cultivating customer loyalty and cutting packaging waste.
6.2 Balancing Cost vs. Performance
Heavier waterproof coatings or multi-layer structures can increase bag weight:
- Potentially Higher Cost: More plastic usage and thicker lamination.
- Prolonged Bag Life: Durable sacks can reduce breakage rates, offsetting higher initial cost.
Example: A chemical additive firm tested a mid-tier lamination that averted moisture issues while letting them reuse or recycle sacks after multiple uses.
6.3 Future of Degradable Innovations
While standard PP offers robust mechanical strength, ongoing R&D explores:
- Bio-based PP: Potentially reducing fossil-based inputs.
- Biodegradable Films: Breaking down under specific conditions, though performance trade-offs remain.
- Advanced Recycling: More integrated facilities to repurpose laminated or multi-layer sacks.
Example: A Southeastern Asian feed supplier tested biodegradable coatings for partial-lamination Moisture Proof Woven sacks, aiming to combine dryness control with environmental responsibility.
7. Forward-Looking Trends: Infrastructure and Circularity
7.1 Building a Systematic Recycling Network
Companies and governments push:
- Take-Back Programs: Incentivizing returning used sacks.
- Sorting Tech: Distinguishing multi-layer PP for advanced reprocessing.
- Global Standards: Harmonizing labeling so consumers easily identify #5 plastics.
Example: A Middle Eastern co-op partnered with local municipalities to streamline PP bag recycling, reducing landfill reliance and bolstering brand image.
7.2 Pressure from Regulations and Consumers
Mounting eco-awareness:
- Stricter Extended Producer Responsibility (EPR): Puts onus on manufacturers to manage end-of-life packaging.
- Retailer Demands: Many stores prefer or mandate eco-labeled packaging to appeal to conscious buyers.
Example: A European fertilizer brand pivoted to fully recyclable, partially laminated Moisture Proof Woven sacks, highlighting EPR compliance on their product labeling.
8. Illustrative Examples
8.1 Grain and Feed Storage
- Moisture Proof: Typically adequate in enclosed warehouses or mild humidity.
- Partial Lamination: Saves cost while preventing mold or caking.
Example: An African livestock feed supplier used Moisture Proof Woven sacks for 25 kg feed units, avoiding lumping and spoilage in moderate-rain climates.
8.2 Construction Powders (Cement, Plaster)
- Waterproof: If sitting in open-air yards subject to heavy rain or puddles.
- Heavier GSM: Minimizes forklift tears, repeated stack impacts.
Example: A European cement brand concluded fully Waterproof Woven Bags were crucial at maritime loading docks, preventing lost product from wave splashes.
8.3 Chemical or Fertilizer Usage
- Dust Minimization: Fine particulates benefit from liners or dense weaving.
- High Printing Detail: Helps clarity for hazard icons, usage instructions.
Example: A Middle Eastern fertilizer firm introduced thick-laminated Moisture Proof PP Bags, containing volatile nutrients while maintaining color-coded hazard labeling.
9. Conclusion
Moisture Proof Woven bags, Moisture Proof Woven sacks, Moisture Proof PP Bags, multi-wall woven bags, and Waterproof Woven Bags collectively represent pivotal packaging choices for industries reliant on dryness or robust water protection. Moisture Proof Woven bags suffice for moderate humidity or enclosed storage, while Waterproof Woven Bags remain indispensable when direct water contact is a concern. Both rely on woven PP for strength, reusability, and environmental compatibility, with global adoption fueling a ~5–6% annual demand increase.
Going forward, synergy between advanced lamination technologies, plastic recycling efforts, and the exploration of biodegradable resins promises to elevate sustainability and reduce carbon footprints. In tandem with building comprehensive recycling systems, these solutions allow companies to safeguard product integrity, meet consumer expectations for eco-friendly packaging, and comply with evolving regulations. By balancing dryness needs with potential water exposure, businesses can tailor each woven PP solution—delivering essential performance while contributing to a greener, more sustainable global packaging landscape.