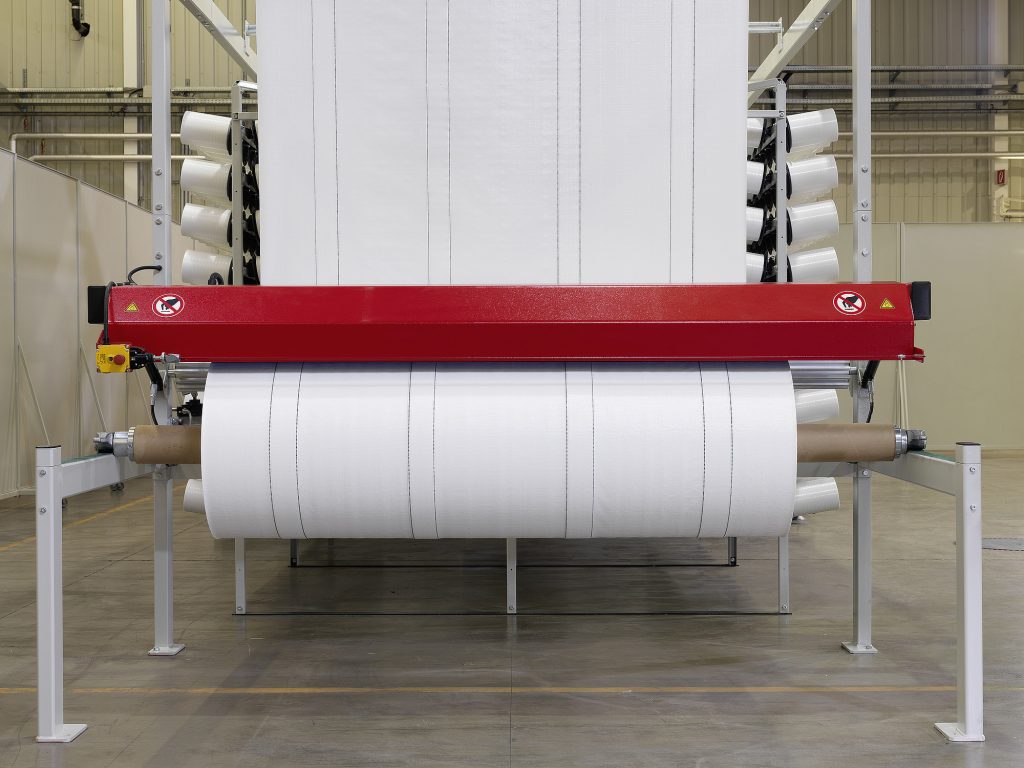
- 1. Why Poly-paper Bags Excel in Agricultural Packaging
- 2. Technical Advantages of Kraft Paper PP Bag Solutions
- 3. Applications and Specific Product Needs
- 4. Essential Product Parameters for Laminated Woven Bags
- 5. Common Questions in a Conversational Format
- 6. FAQs
- 7. Real-World Illustrations
- 8. Learn More Through External Resources
- Conclusion
Answer in Brief: By merging the robust strength of polypropylene with the breathable and print-friendly qualities of paper, Poly-paper Bags effectively reduce product losses, extend shelf life, and enhance transport safety for agricultural goods such as seeds, nuts, and grains.
Global agricultural packaging faces a host of challenges—from preventing moisture damage to deterring pests and retaining product quality throughout long-haul transportation. In 2023, the U.S. Department of Agriculture (USDA) estimated that nearly 20% of global grain is lost due to improper packaging and suboptimal storage conditions, underscoring the critical need for improved solutions. Poly-paper sacks and Kraft Paper Woven Bag designs are emerging as a top choice, blending paper’s eco-friendly image and moderate breathability with polypropylene’s load-bearing capability.
1. Why Poly-paper Bags Excel in Agricultural Packaging
- Hybrid Construction for Durability
- Example: A major wheat exporter in Canada reported that switching to Kraft Paper PP Bag solutions, with a polypropylene interior, reduced bag breakage by 25% during forklift loading.
- Woven polypropylene fibers support heavier loads, while the paper exterior provides good print surfaces and a consumer-friendly, natural appearance.
- Balancing Moisture Control and Breathability
- Paper allows limited air exchange, preventing mold growth in humidity-prone storage areas, while the plastic substrate offers a reliable moisture barrier.
- Example: A seed distributor in Germany chose Kraft Paper Woven Sack options with moderate lamination and recorded a 15% higher germination rate for flower seeds kept in humid warehouses.
- Enhanced Stacking and Transport Stability
- The kraft-paper outer texture often reduces slippage, making tall warehouse stacks safer and easier to manage.
- Example: A rice exporter in Southeast Asia found that Laminated Woven Bags made with a polypropylene core and kraft outer were less prone to shifting during transit, lowering spillage incidents by 30%.
2. Technical Advantages of Kraft Paper PP Bag Solutions
- Improved Pest Resistance
- Many insects can chew through standard paper but struggle with woven polypropylene’s tougher barrier.
- Example: A California-based nut processor halved its infestation rate after integrating a polypropylene-lined Kraft Paper Woven Bag featuring a high-density weave.
- Customization for Product Requirements
- Agricultural goods like soybeans or coffee beans might require higher breathability than grains that only need moderate ventilation.
- Example: A Vietnamese coffee exporter opted for micro-perforated Poly-paper sacks to let roasted beans off-gas without trapping excess moisture, preserving flavor for up to 6 months.
- Eco-Friendliness and Market Appeal
- Paper exteriors are often perceived as more eco-friendly by end consumers, aligning with rising sustainability demands.
- Example: Surveys indicate that 62% of global consumers prefer paper-based or paper-coated packaging for food products due to its “natural” look and potential recyclability (Source: Eurostat, 2023).
3. Applications and Specific Product Needs
Seeds and Germination Rates
- Key Concern: Maintaining seed viability through controlled moisture and air circulation.
- Discussion: Seeds generally benefit from moderate ventilation; a sealed environment may trigger mold or premature germination.
- Example: A grass seed supplier in Europe increased seed longevity by using Poly-paper Bags with an 80 g/m² paper layer plus a 50 μm polypropylene backing.
Nuts (Almonds, Walnuts, Pistachios)
- Key Concern: Rancidity and insect entry.
- Discussion: Nuts contain oils that oxidize when exposed to excessive moisture or oxygen, so partial lamination and a PE liner help maintain freshness.
- Example: An almond distributor in Spain adopted Poly-paper sacks with double stitching, drastically reducing packaging tears and rancidity rates over a 6-month window.
Grains and Cereals (Rice, Wheat, Corn, Soybeans)
- Key Concern: Bulk weight support and fungus prevention.
- Discussion: Laminated Woven Bags can handle 25–50 kg loads while protecting against fungal growth.
- Example: A U.S. wheat cooperative reduced torn bag incidents by 20% after switching to reinforced Kraft Paper PP Bag designs with higher tensile strength.
Coffee Beans
- Key Concern: Preserving aroma and flavor while allowing controlled degassing.
- Discussion: Coffee beans often need one-way valves or micro-perforations to release CO₂ without admitting excess moisture.
- Example: A Brazilian roastery shipped specialty beans in partially perforated Kraft Paper Woven Sack packaging, extending flavor profiles during overseas transit.
Starch (Potato, Corn, Wheat Starch)
- Key Concern: Avoiding moisture absorption that causes lumping.
- Discussion: Fully or partially laminated Poly-paper sacks with a 40–60 μm inner PE layer can keep starch clump-free.
- Example: A European starch manufacturer reported a 35% drop in lump formation post-distribution, attributing it to improved packaging and consistent temperature controls.
4. Essential Product Parameters for Laminated Woven Bags
Parameter | Recommended Range | Impact |
---|---|---|
Bag Thickness | 60–120 μm PP + 70–120 g/m² Paper | Balances rigidity, tear resistance, and weight |
Bag Grammage | 120–200 g/m² (combined) | Higher grammage supports heavier loads and extended storage |
Bag Size | 25–50 kg capacity (typical) | Accommodates different products, from dense grains to bulky coffee beans |
Exterior Lamination | BOPP or PP coating (20–30 μm) | Boosts moisture resistance and visual appeal |
Inner Liner | 40–60 μm PE for sensitive contents | Creates an extra barrier against humidity, especially crucial for nuts and starch |
Breathability | 5–10% daily air exchange (varies by product) | Helps seeds, coffee beans, or certain grains maintain freshness without oversaturation |
Sealing Technique | Heat sealing, double stitching | Minimizes pest infiltration, ensures better load handling |
Example: A Middle Eastern nut supplier facing high-humidity shipping routes chose 80 g/m² kraft plus a 30 μm BOPP laminate with an inner PE liner, drastically reducing product spoilage.
5. Common Questions in a Conversational Format
Topic: “Should I always use a PE liner in my Poly-paper Bags?”
Answer: It depends on product sensitivity. For items prone to dampness (e.g., seeds or starch), a liner is recommended. For robust grains needing minimal moisture control, you can rely on a standard Kraft Paper Woven Sack without a liner.
Topic: “How can I maintain coffee bean freshness while in transit?”
Answer: Consider micro-perforations or degassing valves. This approach vents built-up CO₂ without letting excess humidity in, preserving the beans’ flavor and aroma.
6. FAQs
- Q: Are Kraft Paper Woven Sack solutions more expensive than simple paper sacks?
A: Typically, they cost slightly more, but their longevity and protective qualities often offset the initial investment. Reduced product loss translates to long-term savings. - Q: How eco-friendly are Poly-paper sacks overall?
A: They strike a balance between strength and sustainability, as the paper outer layer is usually recyclable. However, local facilities and material choices determine the overall eco-footprint. - Q: Do Laminated Woven Bags hinder necessary ventilation for seeds?
A: Full lamination can restrict airflow. Many manufacturers now offer partial laminations or micro-perforations tailored to specific ventilation needs. - Q: Are there standard certifications for Kraft Paper PP Bag solutions?
A: Many producers seek ISO certifications or adhere to FDA/EFSA guidelines for food contact materials. Checking compliance documents ensures quality. - Q: What about large-scale industrial storage—can these bags handle forklift stacking?
A: Yes, if designed with reinforced edges and proper thickness. Several global agricultural cooperatives successfully use forklift-compatible Poly-paper Bags for high-volume operations.
7. Real-World Illustrations
- Seed Exporter in France
- Switched to a Kraft Paper Woven Sack featuring a 70 g/m² paper exterior and 60 μm PP interior layer.
- Result: Elevated germination rates, with fewer mold occurrences reported over 8 months of warehouse storage.
- Nut Distributor in the Middle East
- Introduced double-stitched Poly-paper sacks with a 50 μm PE liner for pistachios and almonds.
- Result: Decreased insect infestation and reduced spoilage during extreme heat shipping seasons.
- Grain Cooperative in India
- Adopted Laminated Woven Bags with improved stacking resistance, handling 25–50 kg loads without frequent tearing.
- Result: Lowered overall packaging breakage by 20%, cutting operational costs significantly.
8. Learn More Through External Resources
Explore in-depth performance metrics of Poly-paper Bags, where flood control and other heavy-duty applications demonstrate their remarkable durability and adaptability.
For an inside look at sustainability initiatives, browse Kraft Paper Woven Bag perspectives, focusing on the ethical and eco-conscious manufacturing strategies shaping the future of agricultural packaging.
Conclusion
Strong market demand and evolving consumer preferences continue to spotlight Poly-paper Bags, Poly-paper sacks, Kraft Paper Woven Bag, Kraft Paper PP Bag, Kraft Paper Woven Sack, and Laminated Woven Bags as advanced solutions for seeds, nuts, grains, coffee beans, and starch products. By blending the tensile power of polypropylene with the breathability and visual appeal of paper, these hybrid bags tackle moisture, pest challenges, and stacking inefficiencies head-on.
Optimizing parameters like bag thickness, grammage, and sealing techniques directly influences product quality and shelf life—an increasingly urgent priority for agricultural stakeholders. As new technologies emerge, ranging from micro-perforations to partial lamination, industry leaders can further fine-tune packaging to meet product-specific requirements, reduce spoilage, and build a more reliable global food supply chain.