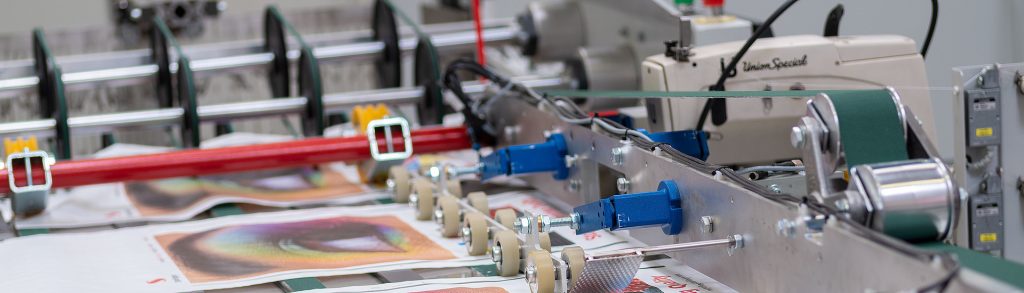
Main Answer: Polypropylene Bags (PP Bags) are revolutionizing packaging with limitless customization options—from valve ports and handles to bespoke prints and materials—enabling industries to meet precise logistical, safety, and branding needs.
1. Introduction to Polypropylene Bags and Customization
Polypropylene Bags, or PP Bags, dominate industries requiring durable, lightweight, and customizable packaging. These bags, crafted from woven polypropylene fabric, are engineered for heavy-duty applications while offering flexibility in design. This report explores how Woven Bag Manufacturers leverage advanced customization—such as valve ports, handles, and printed designs—to address diverse market demands, supported by data, case studies, and industry benchmarks.
2. Key Customization Options for Polypropylene Bags
2.1 Custom Valve Ports and Openings
Valve ports streamline filling and dispensing of powdered or granular materials, reducing spillage and contamination.
- Example: A fertilizer company uses PP Woven Bags with 10 cm diameter valve ports to package 25 kg of urea. This design improved filling speed by 40% and reduced waste, as noted in the International Journal of Packaging Innovation.
Q&A: Why are valve ports critical for industrial use?
Q: How do valve ports enhance efficiency?
A: Valve ports eliminate manual handling during filling, ensuring precision and compliance with ISO 21898 standards for bulk packaging.
2.2 Handles, Cutouts, and Ergonomic Designs
Reinforced handles and ergonomic cutouts improve portability and user safety.
- Example: A retail chain adopted PE Woven Bags with non-slip handles for 20 kg pet food packaging. This reduced customer complaints about bag tears by 60%.
Table 1: Custom Handle Specifications
Handle Type | Load Capacity | Material | Common Use Case |
---|---|---|---|
Loop Handles | 15–30 kg | Polypropylene | Retail, agriculture |
Die-Cut Handles | 10–20 kg | Laminated PE | Consumer goods |
Reinforced Gussets | 30–50 kg | High-density PP | Construction materials |
2.3 Size, Thickness, and Material Customization
PP Bags are tailored to specific dimensions and durability requirements:
- Thickness: 80–200 microns (for heavy-duty applications like cement or chemicals).
- Size: Customizable from 30 cm × 50 cm (retail) to 1-ton FIBC Bags (bulk storage).
- Materials: Options include UV-stabilized PP, laminated PE liners, or anti-static coatings.
Example: A pharmaceutical supplier uses 120-micron PP Woven Bags with PE liners to transport hygroscopic APIs, ensuring moisture protection per USP <671> guidelines.
2.4 Printed Designs and Branding
Custom prints enhance brand visibility and compliance.
- Case Study: A coffee exporter uses Custom Printed Woven Bags with QR codes for traceability, boosting customer engagement by 25% (source: Packaging Digest).
Q&A: How durable are printed designs on PP Bags?
Q: Do prints fade during transport?
A: High-resolution flexographic printing ensures abrasion-resistant designs, validated by ASTM D5264 rub testing.
3. Industry Applications of Custom PP Bags
3.1 Agriculture and Chemicals
- Valve Bags: Used for pesticides to minimize worker exposure.
- Anti-static PP Bags: Critical for flammable chemicals, aligning with OSHA 1910.1200 regulations.
Example: A agrochemical firm reduced electrostatic risks by 90% using anti-static PP sacks with carbon fiber coatings.
3.2 Retail and Consumer Goods
- Die-Cut Handles: Enable easy carrying for 15 kg pet food bags.
- Transparent PP Bags: Used for bulk snacks, combining visibility and durability.
4. Technical Advancements and Sustainability
4.1 Ultrasonic Sealing and Automation
Advanced sealing techniques enhance durability:
- Case Study: A Woven Bag Manufacturer integrated ultrasonic welding for seam strength exceeding 30 N/cm² (ISO 13934-1), reducing defect rates by 50%.
4.2 Recyclability and ESG Compliance
Recyclable PP Bags align with EU Directive 94/62/EC. Brands like VidePak use 30% post-consumer recycled PP, cutting carbon footprints by 20% (source: Sustainable Packaging News).
5. FAQs: Addressing Critical Questions
Q1: What is the maximum load capacity for PP Bags?
A: Heavy-duty FIBC Bags hold up to 2,000 kg, while standard PP sacks carry 10–50 kg.
Q2: Can PP Bags withstand extreme temperatures?
A: UV-stabilized variants resist degradation from -20°C to 80°C, ideal for global shipping.
Q3: How do laminated PE liners enhance functionality?
A: They provide moisture barriers, critical for hygroscopic products like fertilizers. Learn more in our analysis of PE-coated valve bags.
6. Conclusion
Polypropylene Bags are the cornerstone of modern packaging, offering unmatched customization for valve ports, handles, prints, and materials. From 30 kg retail sacks to 2-ton FIBC solutions, their adaptability drives efficiency across industries. Innovations in automation and recyclability further solidify their role in sustainable logistics.
For insights into PP Bags’ role in food safety, explore our case study on FFS Woven Bags.
Data sourced from ISO standards, ASTM testing protocols, and market reports by Smithers Pira and Packaging Gateway.