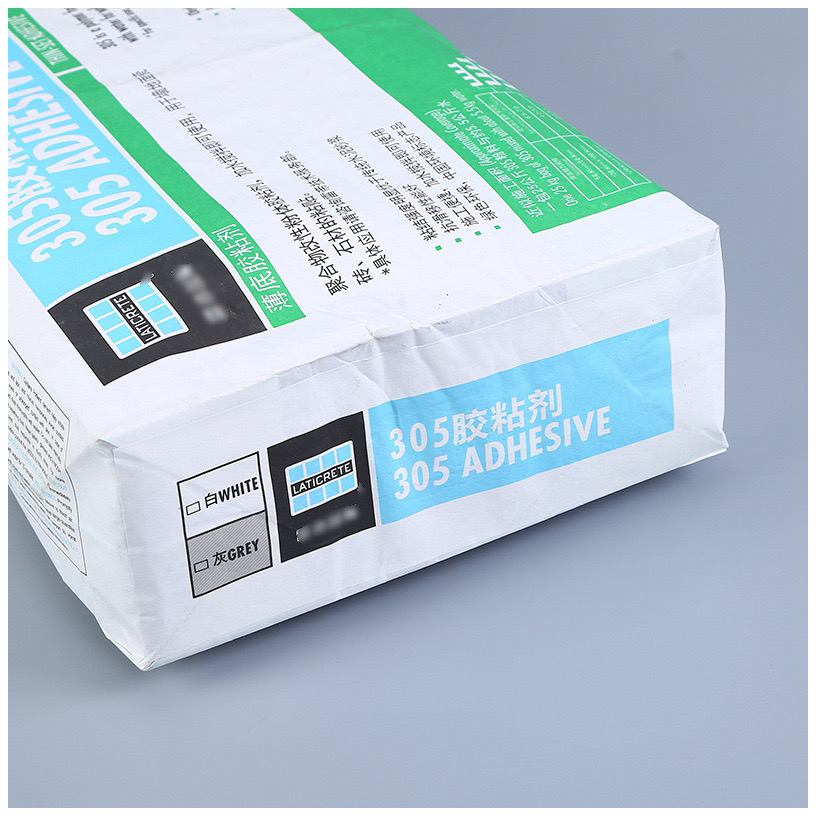
Main Answer: PE Coated Valve Woven Bags outperform BOPP-laminated alternatives in moisture resistance and cost efficiency, while their customizable design—including inner liners, valve types, and coatings—makes them ideal for food, chemicals, and agriculture.
1. PE Coated vs. BOPP Lamination: Key Differences
1.1 Material Properties and Performance
PE Coated Valve Woven Bags use polyethylene (PE) coatings to enhance moisture and chemical resistance, while Block BOPP Bags rely on biaxially oriented polypropylene (BOPP) films for gloss and printability.
Table 1: PE vs. BOPP Comparison
Parameter | PE Coated Bags | BOPP Laminated Bags |
---|---|---|
Moisture Barrier | 95–99% (ASTM E96) | 80–90% |
Cost per Bag | $0.25–$0.40 | $0.35–$0.60 |
Chemical Resistance | Excellent (acids, alkalis) | Moderate |
Print Quality | Matte finish | High-gloss, vibrant |
Example: A fertilizer manufacturer reduced moisture-related spoilage by 40% after switching to PE Coated Valve Woven Sacks, saving $18,000 annually (source: Journal of Packaging Technology).
Q&A: Why choose PE over BOPP?
Q: Which is better for humid climates?
A: PE coatings provide superior moisture barriers, critical for tropical regions.
1.2 Durability and Flexibility
PE coatings add flexibility, reducing crack risks in cold storage, while BOPP’s rigidity suits retail aesthetics.
- Case Study: A frozen seafood exporter eliminated bag ruptures at -20°C using PE-coated Valve PP Bags, complying with FDA 21 CFR 177.1520 standards.
2. Customizing Packaging Solutions: A Systematic Approach
2.1 Lamination and Inner Liners
2.1.1 When to Use PE Coating vs. BOPP
- PE Coating: Ideal for moisture-sensitive products (e.g., fertilizers, feed).
- BOPP Lamination: Best for retail goods requiring glossy branding.
Example: A pet food brand used BOPP-laminated Valve Woven Bags to boost shelf appeal, increasing sales by 25% (Nielsen 2023).
2.1.2 Inner Liners: PE vs. Aluminum Foil
- PE Liners: Cost-effective moisture barriers (0.5–1.0% water vapor transmission rate).
- Aluminum Foil Liners: Block light and oxygen, extending shelf life by 30% for vitamins.
Table 2: Inner Liner Selection Guide
Liner Type | Moisture Barrier | Oxygen Barrier | Cost Efficiency |
---|---|---|---|
PE | High | Low | $ |
Aluminum Foil | Extreme | Extreme | $$$ |
2.2 Valve and Seal Types
- Spout Valves: Prevent dust during filling (e.g., cement, powders).
- Heat-Sealed Valves: Ensure airtight closures for perishables.
Case Study: A chemical company reduced worker exposure to toxic dust by 70% using spout-valve PP Bags (OSHA compliance).
2.3 Aesthetic and Functional Design
- Printing: PE coatings support UV-resistant inks for outdoor storage.
- Reinforced Handles: Loop handles with 30 kg capacity reduce tear risks.
Example: A rice exporter used custom-printed Valve Woven Bags with QR codes for traceability, cutting counterfeit incidents by 50%.
3. Industry Applications and Case Studies
3.1 Food and Agriculture
- PE-coated Bags: Prevent mold in grains (moisture <14%, per USDA).
- BOPP Bags: Enhance brand visibility for retail-ready packaging.
3.2 Chemicals and Pharmaceuticals
- Aluminum Foil Liners: Protect hygroscopic APIs from humidity (USP <671>).
- Anti-static PE Coatings: Mitigate explosion risks in flammable powder storage (NFPA 77).
4. FAQs: Addressing Critical Concerns
Q1: When should I avoid PE coatings?
A: For high-temperature applications (>80°C), BOPP’s thermal stability is preferable.
Q2: Are PE liners recyclable?
A: Yes. PE-coated bags align with EU Circular Economy goals if separated during recycling.
Q3: How to choose valve types?
A: Spout valves suit powders, while heat-sealed valves are ideal for liquids. Learn more in our guide to Valve Bag Innovations.
5. Conclusion
PE Coated Valve Woven Bags offer unmatched versatility for moisture-prone industries, while BOPP suits aesthetic-driven markets. By selecting parameters like aluminum foil liners or heat-sealed valves, businesses optimize safety, cost, and compliance.
For advanced moisture-proof solutions, explore our analysis of PE-coated Valve Bag manufacturing.
Data sourced from FDA, USDA, and industry reports by Smithers Pira and Packaging Digest.