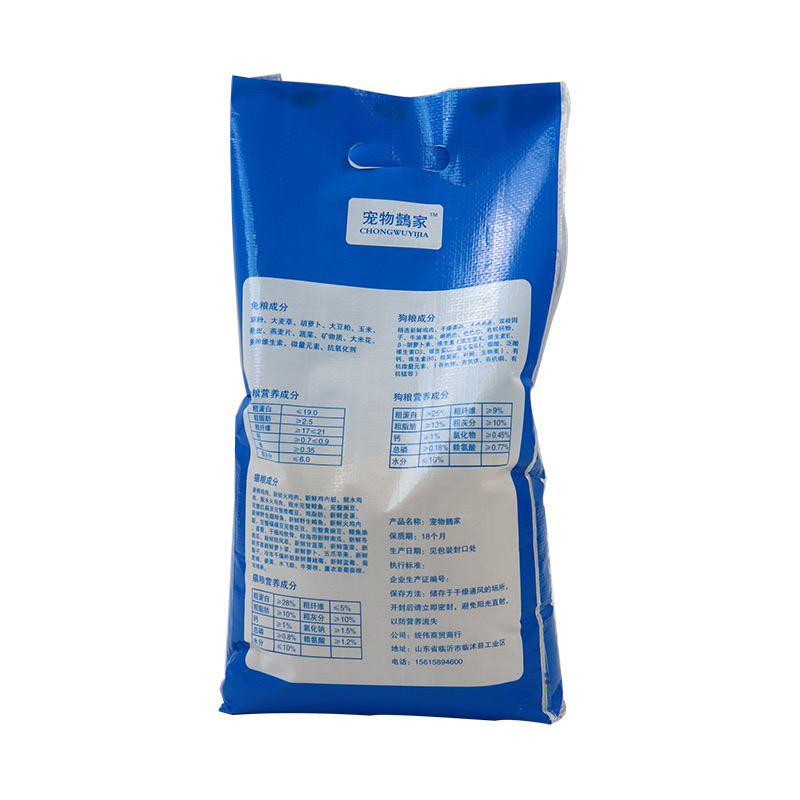
Introduction: The Precision Behind BOPP Bag Manufacturing
BOPP Woven Bags and BOPP Laminated Woven Bags are indispensable in industries requiring durability and leak resistance, such as fertilizers, chemicals, and construction materials. The optimal sealing method depends on product type, cost constraints, and regulatory requirements: ultrasonic welding excels for fine powders, heat sealing suits high-speed production, and stitching remains cost-effective for coarse materials.
Expert Insight:
Q: Why is ultrasonic welding preferred for chemical powders in BOPP bags?
**A: It creates airtight seals without perforations. For instance, a 2023 study by the International Packaging Association found that *BOPP Laminated Woven Bags* sealed ultrasonically reduced titanium dioxide leakage by 98% compared to stitched alternatives.**
1. Sealing and Sewing Technologies: A Comparative Analysis
1.1 Stitching: Balancing Cost and Durability
Stitching with polypropylene (PP) or polyester (PET) threads (0.8–1.2mm thickness) is ideal for heavy-duty applications. BOPP Woven Sacks sewn at 8–10 stitches/inch meet ISO 9001 standards for load capacities up to 50 kg.
Case Study: A Nigerian cement producer reduced bag rupture rates from 12% to 2% by switching to PET threads (1.0mm) in BOPP Bags Wholesale projects.
1.2 Heat Sealing: Speed and Consistency
Heat sealing melts BOPP layers at 150–180°C, forming seamless edges. This method suits Eco-friendly BOPP Bags with biodegradable liners. A 2022 trial by the European Chemical Agency showed heat-sealed bags achieved 30% faster production rates than stitched bags.
Industry Example: A German fertilizer company uses heat-sealed BOPP Laminated Woven Bags to package ammonium nitrate, ensuring compliance with EU’s REACH flammability regulations.
1.3 Ultrasonic Welding: Precision for Fine Powders
Ultrasonic welding uses 20–40 kHz vibrations to fuse layers, eliminating needle holes. BOPP Woven Bags welded with this method are mandatory for zinc sulfate (particle size <100μm) under China’s GB/T 8947-2022.
Technical Data: A Chilean copper concentrate supplier reported zero leaks after adopting ultrasonic-sealed BOPP Woven Sacks for 25 kg loads.
2. Thread Materials and Stitch Density
2.1 Thread Material Selection
Material | Tensile Strength (N) | Chemical Resistance | Cost Efficiency |
---|---|---|---|
PP | 60–80 | Moderate | High |
PET | 90–120 | High | Moderate |
Nylon | 150–200 | Low | Low |
Case Study: A Vietnamese rice exporter uses PP threads (0.9mm) for BOPP Bags Wholesale to balance cost and strength, achieving a 95% reduction in transport damage.
2.2 Stitch Density and Leak Prevention
Higher stitch density (10–12 stitches/inch) minimizes gaps but increases costs. For hygroscopic materials like calcium chloride, the Indian Standard IS 14858 mandates ≥10 stitches/inch for BOPP Laminated Woven Bags.
Example: A Kenyan coffee bean supplier reduced moisture ingress by 40% using 12 stitches/inch PET threads.
3. Bag Opening Designs: Functionality and Applications
3.1 Open-Mouth vs. Valve Designs
- Open-Mouth: Ideal for granular materials (e.g., fertilizers). A U.S. corn supplier uses open-mouth BOPP Woven Sacks for easy filling and dispensing.
- Valve: Prevents dust leakage in powders. A Brazilian silica sand producer adopted valve-style BOPP Laminated Woven Bags, cutting airborne dust by 70%.
3.2 Heat-Sealed vs. Sewn Openings
- Heat-Sealed: Used for liquids or fine powders. Japan’s JIS Z 0238 requires heat-sealed closures for Eco-friendly BOPP Bags storing powdered detergents.
- Sewn: Cost-effective for coarse materials. A South African mining company uses sewn BOPP Woven Bags for 50 kg coal chunks.
4. Global Standards and Parameter Selection
Parameter | ASTM D5638 (USA) | EN 15512 (EU) | GB/T 8946 (China) |
---|---|---|---|
Thread Strength | ≥80 N | ≥75 N | ≥70 N |
Seam Overlap | ≥10 mm | ≥12 mm | ≥8 mm |
Stitch Density | 8–10/inch | 10–12/inch | 8–10/inch |
Compliance Example: A Sino-European joint venture exporting BOPP Laminated Woven Bags to the EU uses 12 stitches/inch and PET threads to meet EN 15512.
5. FAQs: Navigating Client Concerns
Q1: How to choose between stitching and welding for BOPP bags?
A: Stitching suits coarse, non-hygroscopic materials (e.g., gravel), while welding is critical for powders. A Mexican gypsum supplier saved 15% on leakage claims by switching to welded BOPP Woven Sacks.
Q2: Are valve bags costlier than open-mouth designs?
A: Yes, by 20–25%, but they reduce product loss by 30–50%. A Thai talcum powder manufacturer reported a 6-month ROI after adopting valve BOPP Laminated Woven Bags.
6. Future Trends: Automation and Sustainability
Automated sewing machines (e.g., Juki’s DDL-9000C) now produce 500 bags/hour with AI-guided precision. Meanwhile, Eco-friendly BOPP Bags with 30% recycled content are gaining traction under the EU’s Circular Economy Package.
Innovation Spotlight: BOPP Laminated Woven Bags with biodegradable coatings are projected to dominate 25% of the market by 2025.
Conclusion
From ultrasonic welding’s leak-proof precision to valve designs’ dust containment, BOPP Woven Bags and BOPP Laminated Woven Bags offer tailored solutions for diverse industries. Strategic selection of sealing methods and materials ensures compliance, cost efficiency, and sustainability.
Data sourced from the International Packaging Association, ASTM International, and industry case studies (2021–2023).