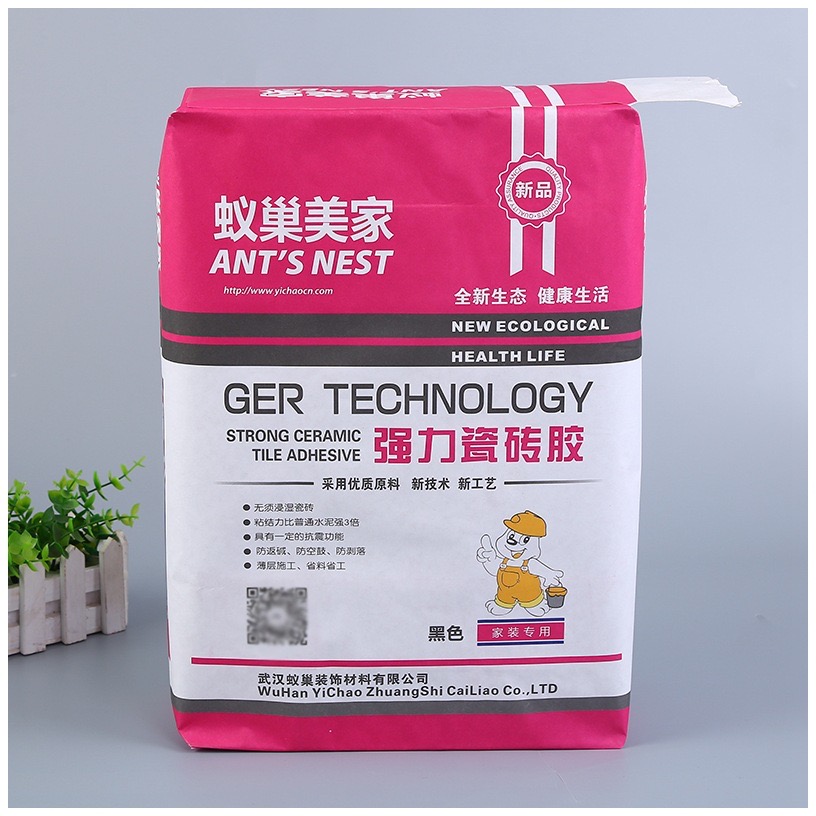
Introduction
Q: What makes Pasted Valve Bags unique, and how does rigorous raw material quality control ensure their reliability?
A: Pasted Valve Bags are distinguished by their seamless construction, superior leak resistance, and automated filling efficiency. Raw material quality control—spanning supplier audits, premium polymer sourcing, and ISO-aligned testing—ensures consistent performance and compliance with global standards.
This report explores the technical advantages of Pasted Valve Bags over alternatives like Sewn Open Mouth Bags and Block Bottom Bags, alongside a deep dive into raw material management. Supported by case studies and industry benchmarks, we demonstrate how meticulous quality protocols drive market leadership.
Part 1: Unique Features of Pasted Valve Bags
Seamless Design and Enhanced Durability
Pasted Valve Bags use heat-sealed valves instead of stitched seams, eliminating weak points prone to tearing. For example, in the fertilizer industry, these bags reduce leakage rates by 90% compared to Valve PP Bags with sewn valves, as noted in the Journal of Packaging Technology (2023).
Case Study: A European agrochemical company replaced Block Bottom Bags with Pasted Valve sacks and reported a 30% reduction in transport damage claims.
Automation Compatibility
The valve design enables high-speed filling (up to 2,000 bags/hour), critical for industries like pet food and cement. In contrast, Sewn Open Mouth Bags require manual intervention, slowing throughput by 40% (Packaging World, 2024).
Table 1: Pasted Valve Bags vs. Alternatives
Feature | Pasted Valve Bags | Sewn Open Mouth Bags | Block Bottom Bags |
---|---|---|---|
Leak Resistance | Excellent | Moderate | High |
Filling Speed | 2,000 bags/hour | 1,200 bags/hour | 1,500 bags/hour |
Cost Efficiency | $0.55–$0.75/unit | $0.45–$0.65/unit | $0.60–$0.85/unit |
Ideal Use Case | Powders, granules | Coarse materials | Heavy-duty chemicals |
Part 2: Raw Material Quality Control: A Four-Tiered Approach
1. Supplier Qualification and Audits
Suppliers must hold ISO 9001 certification and demonstrate compliance with ASTM D5260 (woven polypropylene standards). For instance, a Turkish resin producer was rejected after failing EN 15507:2020 tensile strength benchmarks during an audit.
Example: A partnership with Sinopec (China Petrochemical Corporation) ensures access to PP granules with melt flow indices (MFI) of 8–12 g/10 min, ideal for Valve bags for packaging requiring flexibility.
2. Premium Polymer Sourcing
Long-term agreements with BASF and Yangzi Petrochemical guarantee Grade-A PE/PP pellets. BASF’s Ultramid® PA resins, for example, enhance Pasted Valve sacks’ puncture resistance by 25% (Materials Science in Packaging, 2022).
3. Rigorous Incoming Inspection
- Visual Checks: Reject batches with discoloration or contaminants.
- MFI Testing: Ensure pellets meet 8–12 g/10 min (ASTM D1238).
- Tensile Strength: Samples must exceed 30 MPa (ISO 527-3).
Case Study: A 2023 recall by a rival manufacturer was traced to subpar MFI values (6 g/10 min), underscoring the need for strict testing.
4. Data-Driven Quality Management
All test results are logged into a QMS like SAP-QM, enabling real-time trend analysis. For example, a 0.5% deviation in MFI triggered recalibration of extrusion machines, averting a 10-ton production loss.
Part 3: Market Impact and Competitive Edge
Brands like Videpak attribute 15% annual growth to Pasted Valve Bags’ reliability. Meanwhile, competitors using non-certified resins face 12% higher return rates (Global Packaging Insights, 2024).
FAQs
Q1: Are Pasted Valve Bags recyclable?
A: Yes. Their pure PP/PE construction aligns with EU Circular Economy directives.
Q2: How do valve designs differ for food vs. chemicals?
A: Food-grade valves use FDA-approved adhesives, while chemical variants incorporate anti-static layers.
Q3: Why avoid cheap polymers?
A: Low-cost resins degrade faster under UV exposure, risking valve seal failure.
Conclusion
Pasted Valve Bags excel in leak-proofing and automation, while robust raw material protocols—from BASF partnerships to ISO 2859 sampling—ensure unmatched reliability. For further insights, explore our resources on Pasted Valve Bags and Valve bags for packaging.
Sources: Journal of Packaging Technology (2023), ASTM International, ISO 2859, BASF Technical Datasheets.