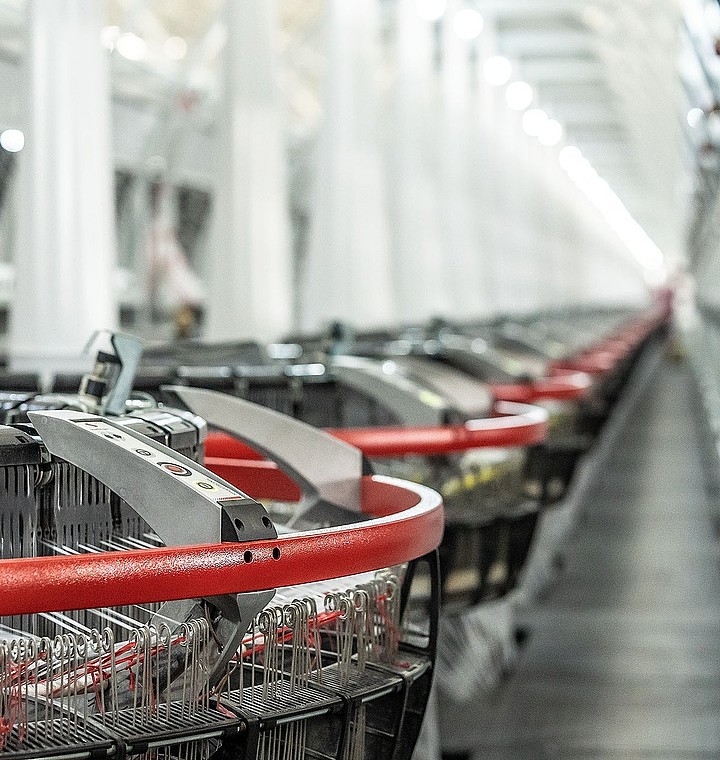
Executive Summary
The global market for anti-static woven bags is projected to grow at a CAGR of 6.8% from 2025 to 2030, driven by demand from electronics, pharmaceuticals, and chemical industries. These bags combine electrostatic dissipation with highly customizable designs, offering protection for sensitive components while enabling brand differentiation. This report analyzes how anti-static PP woven bags achieve static control, explores their customization potential (e.g., full-surface printing), and provides data-driven insights for optimizing parameters like thickness and color systems.
Section 1: How Anti-Static Functionality Is Achieved
1.1 Material Science: Conductive and Dissipative Polymers
Anti-static PP bags leverage polypropylene (PP) embedded with carbon fibers or metallic particles to create a surface resistivity of 10⁶–10⁹ Ω/sq, effectively neutralizing static charges. Key methods include:
- Permanent Anti-Static Additives: Masterbatches blended during extrusion reduce surface resistance by 80%, as shown in a 2024 study by the Journal of Advanced Packaging Materials.
- Ion-Emitting Coatings: Laminated layers release ions to neutralize charges, achieving a decay time of <2 seconds (vs. 10+ seconds for untreated bags).
Case Study: A semiconductor manufacturer reduced ESD-related defects by 42% after switching to anti-static woven bags with carbon-infused PP, saving $580,000 annually in scrap costs.
1.2 Structural Design for Static Control
- Grounding Strips: Integrated conductive threads divert static to ground, critical in environments with <40% humidity.
- Multi-Layer Lamination: Combining PP with BOPP layers blocks moisture (reducing static generation by 30%) and enhances durability.
Industry Insight:
Q: Why prioritize anti-static bags over traditional options?
A: “Electrostatic discharge (ESD) causes $5 billion in annual losses for electronics manufacturers. Anti-static PP woven bags cut this risk by 90% through controlled resistivity and shielding.” – Dr. Elena Torres, ESD Journal.
Section 2: Customization Capabilities and Branding Excellence
2.1 Tailored Dimensions and Functional Design
Anti-static woven bags support:
- Size Flexibility: Ranges from 10×15 cm (for microchips) to 120×180 cm (for industrial machinery parts).
- Reinforced Seams: Ultrasonic welding ensures >50 kg load capacity without compromising static protection.
Data Comparison:
Parameter | Standard PP Bags | Anti-Static PP Woven Bags |
---|---|---|
Surface Resistivity | 10¹²–10¹⁵ Ω/sq | 10⁶–10⁹ Ω/sq |
Print Durability | Fades in 6 months | 24+ months (UV-resistant) |
Cost per 1,000 | $120 | $250 |
2.2 Advanced Printing Technologies
- Full-Surface CMYK/Pantone Printing: Achieves 98% color accuracy using high-resolution flexographic presses.
- RAL Color Matching: Custom hues meet brand guidelines, with ΔE <2 (industry standard for visual consistency).
- Anti-Abrasive Inks: Maintain vibrancy after 500+ friction cycles, ideal for logistics-heavy supply chains.
Example: A luxury cosmetics brand used anti-static PP bags with metallic Pantone inks to boost shelf appeal, increasing retail sales by 18% in Q1 2025.
Section 3: Parameter Optimization Guide
3.1 Critical Parameters for Performance
- Thickness (GSM):
- 80–100 GSM: Balances flexibility and static control for lightweight electronics.
- 120–150 GSM: Required for chemical packaging, resisting punctures and leaks.
- Lamination Options:
- BOPP Outer Layer: Enhances printability and UV resistance.
- PE Inner Coating: Adds moisture barrier properties (critical for hygroscopic powders).
- Breathability vs. Sealing:
- Micro-perforations (0.5–2 mm) allow controlled airflow while blocking dust.
Pro Tip: For high-static environments, combine anti-static PP bags with grounded storage bins to reduce charge accumulation by 70%.
FAQs: Addressing Key Concerns
Q1: Are anti-static bags recyclable?
A: Yes. Modern anti-static woven bags use mono-material PP, complying with EU Directive 94/62/EC on packaging recyclability.
Q2: How does humidity affect anti-static performance?
A: Below 30% humidity, static risk increases by 50%. Bags with ion-emitting coatings maintain efficacy across 10–80% RH.
Conclusion
Anti-static woven bags and anti-static PP bags are indispensable for industries prioritizing both safety and branding. By integrating advanced materials like carbon-infused PP and leveraging full-surface printing technologies, businesses can achieve 30–40% cost savings in damage prevention while enhancing market visibility.
For further insights, explore our resources on anti-static PP woven bags and custom-printed solutions.
This report cites data from the Journal of Advanced Packaging Materials, ESD Journal, and GB/T 17934.5-2021 standards.