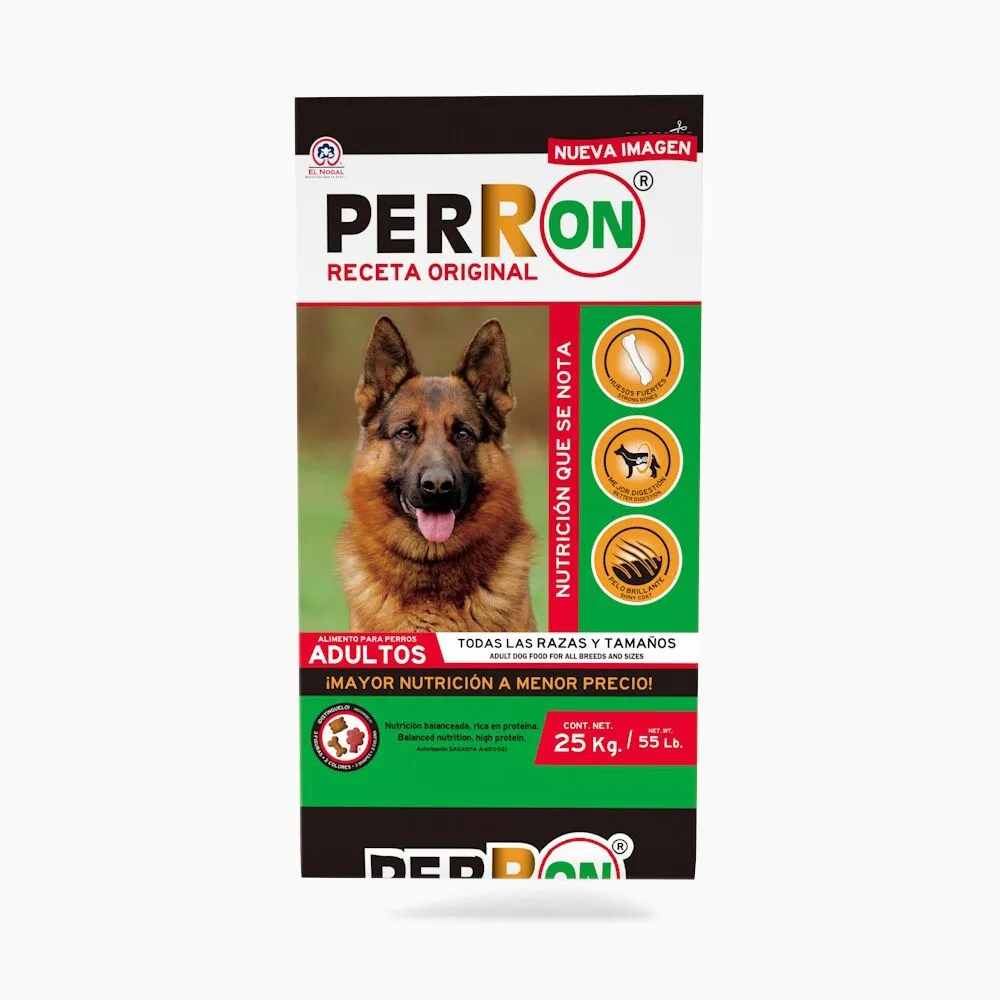
Aluminum foil composite bags are among the most versatile and durable packaging solutions available today, widely used in industries ranging from food to pharmaceuticals. This article delves into the technological advancements that have enhanced the functionality of these bags and their cost-efficient solutions for modern businesses. From barrier properties to customization options, aluminum foil composite bags meet diverse needs while aligning with sustainability and efficiency goals.
Technological Advancements in Aluminum Foil Composite Bags
The evolution of aluminum foil composite bags is driven by innovations in materials, production techniques, and design enhancements.
- Enhanced Barrier Properties
The primary function of aluminum foil composite bags is to offer superior barrier protection. Recent advancements in metallization and polymer layering have significantly improved their ability to shield contents from oxygen, moisture, UV rays, and contaminants. These innovations ensure product longevity and quality, particularly for perishable goods. - Lightweight and Durable Designs
Technological breakthroughs in multi-layer co-extrusion have enabled the production of lightweight yet highly durable bags. These designs reduce transportation costs without compromising product protection. - Custom Printing and Branding
Advanced printing techniques now allow for high-resolution, multi-color branding directly onto the bag surface. This enhances brand visibility while maintaining the structural integrity of the bag. - Eco-Friendly Alternatives
Companies are increasingly using recyclable and biodegradable materials in aluminum foil composite bags, reflecting growing environmental concerns. These options maintain the high-performance features of traditional bags while reducing environmental impact.
Key Features and Specifications of Aluminum Foil Composite Bags
The table below summarizes the typical specifications of aluminum foil composite bags, highlighting their versatility and adaptability for different applications:
Feature | Specification | Benefits |
---|---|---|
Material Composition | Aluminum foil + LDPE/HDPE | Excellent barrier properties and durability |
Thickness Range | 0.05 mm to 0.15 mm | Customizable for strength and flexibility |
Sealing Options | Heat-sealed, zipper closure | Secure containment and easy resealability |
Size Range | Small (50g) to Large (50kg) | Suitable for varied product capacities |
Printing Options | Gravure printing, up to 10 colors | High-quality branding and customization |
Applications | Food, pharmaceuticals, chemicals | Versatile across industries |
Cost-Efficient Solutions with Aluminum Foil Composite Bags
Aluminum foil composite bags are not just technologically advanced but also cost-efficient. The following strategies optimize their production and usage:
- Bulk Manufacturing
Utilizing automated systems and Starlinger technology ensures high production volumes with reduced per-unit costs. Bulk manufacturing also minimizes material wastage. - Material Optimization
Incorporating recycled aluminum foil and thinner polymer layers without compromising quality reduces raw material expenses. - Versatile Sizing
Offering bags in various sizes helps businesses minimize costs by selecting the most appropriate packaging volume for their products. - Multi-Industry Compatibility
By serving multiple sectors, such as food, pharmaceuticals, and construction, manufacturers can streamline production processes and achieve economies of scale.
Industrial and Sustainability Applications
Aluminum foil composite bags play a vital role in both industrial and sustainable applications, showcasing their versatility:
- Industrial Applications
These bags are widely used for storing sensitive materials, such as electronic components, chemicals, and pharmaceutical drugs. Their robust barrier properties prevent contamination and degradation. - Sustainable Packaging Solutions
Companies like VidePak are incorporating eco-friendly practices by developing recyclable aluminum foil composite bags, ensuring alignment with global environmental policies and reducing carbon footprints.
External Link 1: Discover how laminated woven bags are manufactured using advanced co-extrusion processes to meet market demands in this detailed guide.
Challenges and Innovations in Production
Despite their advantages, aluminum foil composite bags face challenges such as cost management and recyclability. Innovations addressing these issues include:
- Advanced Co-Extrusion Techniques
These enable precise material layering, ensuring optimal performance while reducing raw material usage. - Reusable Designs
Reusable and resealable aluminum foil composite bags are gaining traction as a sustainable alternative. - Smart Packaging Features
Integration of QR codes and RFID tags into bag designs facilitates supply chain tracking and improves operational efficiency.
Future Trends in Aluminum Foil Composite Bags
The future of aluminum foil composite bags lies in continuous innovation, driven by consumer demands and technological advancements:
- Integration with Smart Technologies
As industries adopt IoT solutions, aluminum foil composite bags equipped with smart sensors will enhance inventory management and traceability. - Increased Recyclability
Research into fully recyclable composite materials is making headway, promising bags that maintain high performance while being environmentally responsible. - Global Market Expansion
With growing demand for secure and eco-friendly packaging, aluminum foil composite bags are set to dominate emerging markets, particularly in Asia and Africa.
External Link 2: For more insights into the role of aluminum foil composite bags in waste management and recycling, visit this comprehensive resource.
Aluminum foil composite bags exemplify the intersection of innovation, functionality, and sustainability in modern packaging. As technological advancements and cost-efficient solutions continue to evolve, these bags remain indispensable across industries, providing reliable and eco-conscious packaging solutions.