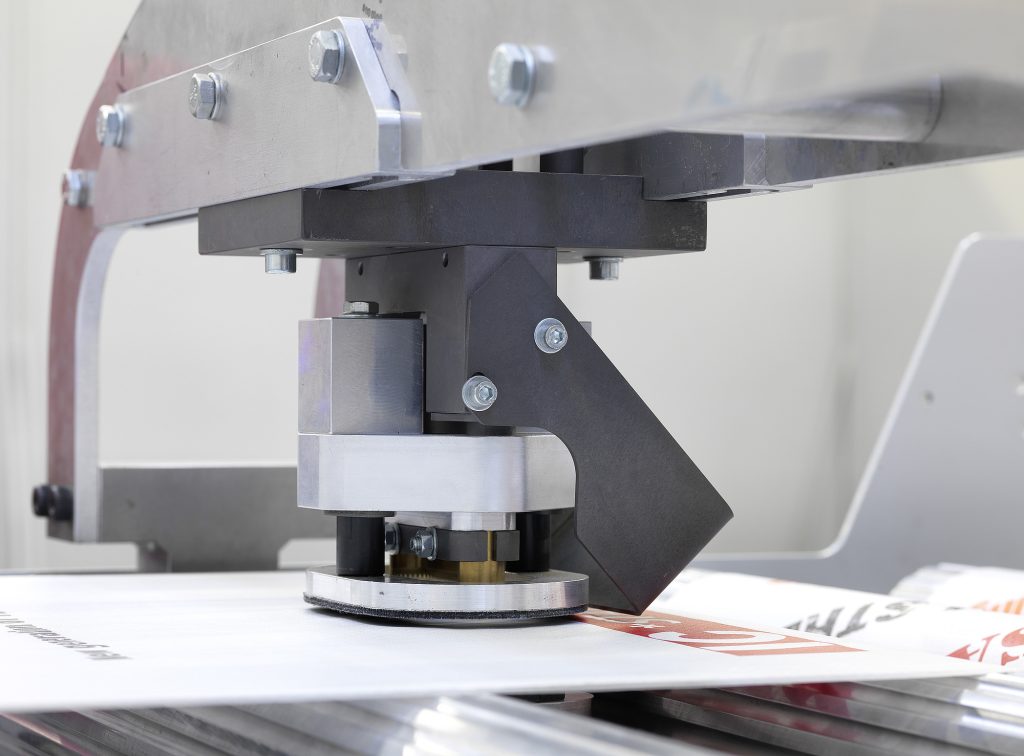
The modern packaging industry demands more than just functionality; it requires precision, reliability, and efficiency. This is especially true in the production of Form-Fill-Seal (FFS) roll bags, a solution widely used in industries ranging from agriculture to construction and beyond. The role of quality control (QC) in FFS roll bags production is not just about meeting basic standards but about ensuring that every bag meets the specific needs of the customer while being durable, cost-effective, and efficient. Quality control is the backbone of consistency and excellence in FFS roll bags production, ensuring that each bag adheres to the required specifications for material strength, sealing, and printing.
FFS Roll Bags: An Overview
FFS roll bags are produced using a Form-Fill-Seal system, where rolls of polyethylene or polypropylene are automatically formed, filled, and sealed into bags by a machine. These bags are widely used for packaging agricultural products, chemicals, fertilizers, and more due to their high strength, resistance to punctures, and customizable features.
Common Applications of FFS Roll Bags:
- Agricultural Packaging: Used to store grains, seeds, fertilizers, and animal feed.
- Chemical Packaging: Provides safe and reliable containment for chemicals, both hazardous and non-hazardous.
- Retail and Consumer Goods: Used in packaging bulk products like pet food, flour, and construction materials.
The Role of Quality Control in FFS Roll Bags Production
Quality control is critical at every stage of FFS roll bag production, from raw material sourcing to the final inspection of the finished product. Here’s a breakdown of how quality control influences the production process.
1. Raw Material Selection
The foundation of a high-quality FFS roll bag begins with the selection of polypropylene (PP) or polyethylene (PE) resins. These materials must meet strict standards to ensure that they provide the necessary strength, flexibility, and resistance to environmental factors. QC begins with verifying the quality of these raw materials through rigorous testing, ensuring the bags can withstand the conditions for which they are designed.
2. Film Extrusion
Film extrusion is one of the most crucial steps in the production of FFS roll bags. During this process, resin pellets are melted and extruded into thin films that form the base material for the bags. The quality of the extruded film directly impacts the strength, printability, and sealing properties of the bags.
QC Measures for Film Extrusion:
- Thickness uniformity: QC inspectors monitor the thickness of the film to ensure it is consistent. Variations can lead to weak points or holes in the bags.
- Melt index: This is a measure of the flowability of the melted resin. QC ensures the melt index falls within the specified range for optimal performance.
- Additives: QC also checks for the correct mix of additives like UV inhibitors, antioxidants, and anti-static agents, which enhance the film’s durability and performance.
3. Bag Forming and Sealing
Once the film is produced, the next step is forming the bags. This step involves converting the roll of plastic film into individual bags, followed by sealing the bags to ensure they are secure and functional. The sealing process must be highly precise to avoid defects such as weak seals or incomplete seals that could cause the bags to split or leak during use.
QC Measures for Sealing:
- Seal strength: QC tests the strength of the seals to ensure they meet the required specifications. A poor seal can result in leakage or failure under load.
- Temperature and pressure control: The temperature and pressure used during sealing must be closely monitored to avoid under-sealing or over-sealing.
4. Printing and Customization
Many FFS roll bags are customized with printed logos, branding, and product information. Printing on these bags requires high precision to avoid smudging, color inconsistencies, or improper alignment of text and graphics.
QC Measures for Printing:
- Ink quality: QC ensures the ink used for printing is compatible with the material of the bag and can withstand external conditions such as UV exposure, moisture, and friction.
- Print alignment: Quality control inspectors check for consistent print alignment to ensure that logos and text are clear and legible.
- Color accuracy: QC verifies the color consistency between batches to ensure that the branding remains consistent across all bags.
5. Final Inspection and Testing
After the FFS roll bags are formed, sealed, and printed, they undergo a final round of inspections. These checks ensure that the bags are fully functional and meet the customer’s specific requirements.
Final QC Tests Include:
- Visual inspection: Inspectors check for visible defects such as pinholes, tears, or discoloration.
- Strength tests: QC teams may conduct burst strength or tear resistance tests to ensure that the bags will perform under normal use conditions.
- Seam integrity tests: Inspectors examine the bag’s seams to ensure there are no signs of weakness or separation.
Key Quality Control Standards in FFS Roll Bag Production
The FFS roll bags must meet several international quality control standards. These include:
Standard | Description |
---|---|
ISO 9001 | Ensures that manufacturing processes adhere to consistent and high-quality production standards. |
FDA Compliance (for food-grade bags) | Ensures that bags used for food packaging meet the necessary standards for safety, hygiene, and contamination prevention. |
ASTM D882 | Tests the tensile properties of plastic films, including the elongation at break and tensile strength, to ensure durability and reliability. |
ASTM F88/F88M | Provides a method for testing the seal strength of packaging materials. |
FAQs About FFS Roll Bags
Q1: What are FFS roll bags used for? FFS roll bags are used for packaging a wide range of products, including agricultural products, chemicals, pet food, and bulk items. They are known for their strength, durability, and cost-effectiveness.
Q2: What materials are used in FFS roll bags? FFS roll bags are typically made from polypropylene (PP) or polyethylene (PE) resins. These materials are chosen for their strength, flexibility, and resistance to various environmental factors.
Q3: How is quality controlled in FFS roll bag production? Quality control in FFS roll bags production involves checking the raw materials, monitoring the extrusion process, ensuring proper sealing, testing print quality, and conducting final inspections for strength and integrity.
Q4: Can FFS roll bags be customized? Yes, FFS roll bags can be customized with various features such as printed logos, specific bag sizes, and different film thicknesses to meet the customer’s needs.
Q5: How do FFS roll bags compare to other packaging solutions? FFS roll bags are often more cost-effective, durable, and customizable than other packaging solutions. They offer high strength and can be used for both consumer and industrial products.
Staying Ahead of the Curve with FFS Roll Bags
As the demand for sustainable packaging solutions grows, FFS roll bags are evolving with advancements in fine yarn technology and biodegradable materials. This evolution is part of a broader trend toward eco-friendly packaging solutions, where companies like VidePak are pushing for innovations in design and material selection to meet market demand for both performance and sustainability. VidePak, with its expertise in BOPP woven bags, also offers advancements in FFS roll bags, providing enhanced sealing technologies, high-quality film, and more.
For more on how FFS roll bags and sustainable packaging innovations are shaping the future, check out this article on FFS roll bags and innovations at VidePak and this insight into our commitment to sustainable packaging.
Conclusion
The role of quality control in FFS roll bags production is paramount in ensuring that the final product meets industry standards for strength, reliability, and sustainability. With advancements in material science and automation, companies like VidePak are setting new benchmarks for excellence in packaging. By adhering to stringent quality control standards at every stage of production, businesses can ensure their FFS roll bags are not only functional but also a reliable solution for their clients.