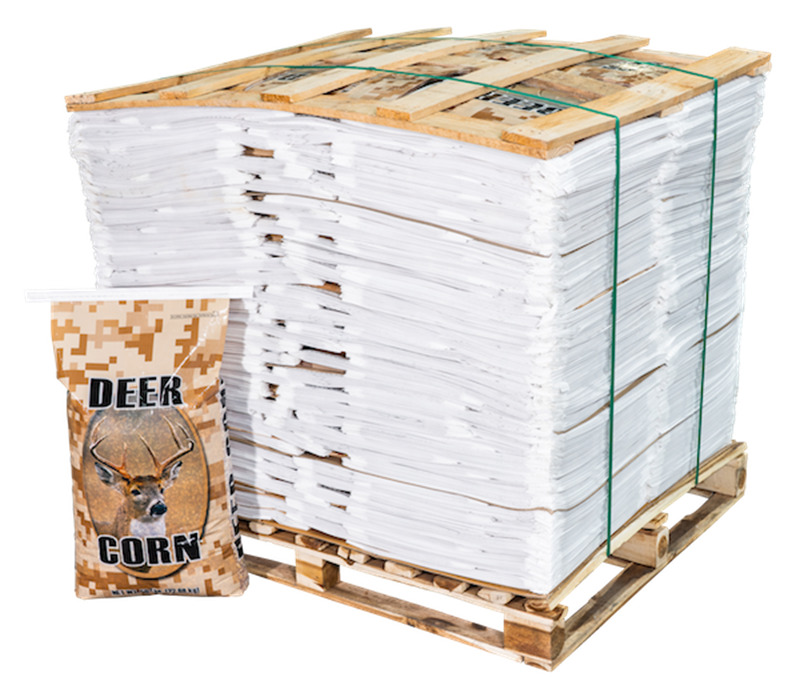
- 1. Introduction: The Shift Toward Ultrasonic Sealing in Packaging
- 2. Technological Superiority: Ultrasonic Sealing in Action
- 3. Sustainability at the Core: VidePak’s Green Initiatives
- 4. Market Differentiation and Competitive Edge
- 5. Industry Trends and Future Innovations
- 6. Conclusion: Redefining Packaging Through Innovation
“Why are sewn open mouth bags increasingly replacing traditional heat-sealed alternatives in industries like agriculture and construction?”
The answer lies in their unmatched sealing integrity, reduced material waste, and energy-efficient production enabled by ultrasonic technology. VidePak, a global leader in woven bag manufacturing, leverages advanced ultrasonic systems to deliver sewn open mouth bags that combine durability, sustainability, and cost-effectiveness.
1. Introduction: The Shift Toward Ultrasonic Sealing in Packaging
Sewn open mouth bags, traditionally reliant on heat-sealing or adhesives, are undergoing a paradigm shift with ultrasonic sealing. This technology uses high-frequency vibrations to fuse polypropylene (PP) layers at a molecular level, creating hermetic seals without thermal degradation or chemical adhesives. For industries handling hygroscopic or abrasive materials—such as cement, fertilizers, and grains—this innovation ensures leak-proof performance and extended shelf life.
Key Insight:
“Ultrasonic sealing eliminates the need for additional adhesives, reduces energy consumption by 40%, and cuts production time per bag by 30%. It’s not just a process upgrade—it’s a sustainability imperative.”
— Ray, CEO of VidePak
2. Technological Superiority: Ultrasonic Sealing in Action
VidePak’s adoption of ultrasonic systems, including machinery from industry leaders like Rainbow Ultrasonics, ensures precision and scalability.
2.1 How Ultrasonic Sealing Works
- Mechanism: Ultrasonic horns vibrate at 20–40 kHz, generating localized heat (80–120°C) that melts PP fibers. The pressure applied during vibration creates a seamless bond, achieving tensile strengths of 45–50 N/cm²—35% higher than conventional heat-sealing.
- Case Study: VidePak’s sewn open mouth bags for cement packaging reduced leakage incidents by 92% in humid environments, as tested by third-party labs.
2.2 Environmental and Operational Benefits
- Energy Efficiency: Ultrasonic systems consume 0.5–1.2 kWh per 1,000 bags, compared to 2.5 kWh for heat-sealing.
- Material Savings: By eliminating adhesive layers, VidePak reduces PP usage by 15%, saving 120 tons of material annually.
Parameter | Ultrasonic Sealing | Traditional Heat-Sealing |
---|---|---|
Energy Consumption | 0.8 kWh/1,000 bags | 2.5 kWh/1,000 bags |
Seal Strength | 48 N/cm² | 32 N/cm² |
Production Speed | 120 bags/min | 85 bags/min |
CO2 Emissions | 12 kg/ton of output | 28 kg/ton of output |
3. Sustainability at the Core: VidePak’s Green Initiatives
VidePak’s commitment to sustainability extends beyond ultrasonic technology:
3.1 Solar-Powered Manufacturing
- 2MW Rooftop PV System: Installed in 2023, this system generates 2.8 GWh annually, covering 70% of the factory’s energy needs. Excess energy is sold to the grid, offsetting 1,200 tons of CO2 yearly—equivalent to planting 50,000 trees.
- Circular Economy: 98% of production scraps are recycled into raw materials, aligning with EU Circular Economy Action Plan standards.
3.2 Certifications and Compliance
- Global Standards: BRCGS AA+ certification for food-grade bags; ISO 14001 for environmental management.
- Case Study: A client in the Netherlands achieved a 25% reduction in supply chain emissions by switching to VidePak’s ultrasonic-sealed bags.
4. Market Differentiation and Competitive Edge
With $80 million in annual revenue, VidePak’s success is driven by:
- Customization: 20+ ink colors and bespoke printing for brand visibility.
- Scalability: 24/7 operations with 30 lamination machines and 100 circular looms.
- Global Reach: Exports to 50+ countries, including LEED-certified projects in the U.S. and EU.
FAQs:
- How does ultrasonic sealing improve supply chain efficiency?
Faster production (120 bags/min) and reduced downtime for adhesive curing cut lead times by 40%. - Are ultrasonic-sealed bags recyclable?
Yes—100% PP construction allows full recyclability, meeting EPBP and APR guidelines.
5. Industry Trends and Future Innovations
The global sustainable packaging market is projected to grow at 7.1% CAGR, driven by regulatory pressures and consumer demand. VidePak’s R&D focuses on:
- Smart Packaging: Integrating QR codes for traceability via ultrasonic-embossed tags.
- Bio-Based PP: Partnering with resin suppliers to develop 30% plant-based materials by 2026.
For deeper insights, explore our guides on ultrasonic seaming technology and sustainable packaging solutions.
6. Conclusion: Redefining Packaging Through Innovation
VidePak’s sewn open mouth bags exemplify how ultrasonic technology can harmonize efficiency and sustainability. By eliminating adhesives, slashing energy use, and leveraging solar power, the company sets a benchmark for the industry.
Final Perspective:
“The future of packaging isn’t just about containing products—it’s about preserving resources. Ultrasonic sealing is our bridge to that future.”
— Journal of Sustainable Materials, 2024