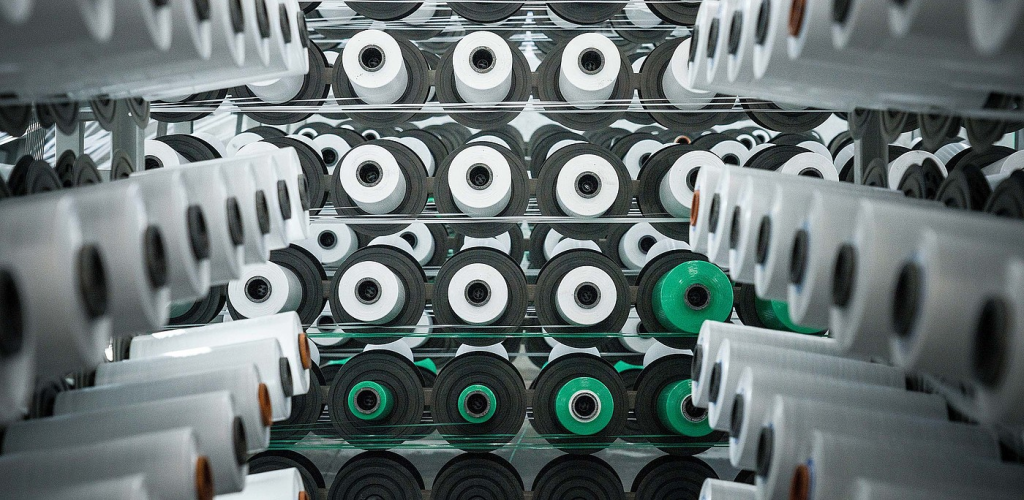
- 1. Technical Superiority: Why BOPP Lamination Matters
- 2. Market Adaptability: Tailoring Solutions to Regional Needs
- 3. Production Excellence: Starlinger’s Role in Precision Manufacturing
- 4. Sustainability: Aligning Construction Needs with ESG Goals
- FAQs: Addressing Industry Concerns
- 5. The Future: Smart Packaging and Global Expansion
- Conclusion: Building Trust, One Bag at a Time
“Why are BOPP laminated woven bags replacing traditional packaging in the construction sector?”
Ray, CEO of VidePak, leans forward with conviction: “It’s the combination of unmatched durability, customization, and sustainability. At VidePak, we don’t just meet industry standards—we redefine them.”
This philosophy has positioned VidePak—a global leader with $80M annual revenue and 526 employees—as a pioneer in BOPP woven bag innovation. Founded in 2008, the company leverages 30+ years of expertise, Austrian Starlinger machinery, and a commitment to ESG principles to deliver solutions tailored to the rigorous demands of the construction industry. This report explores the technical superiority, market adaptability, and sustainability of BOPP woven bags, with insights into how VidePak’s strategies align with global trends.
1. Technical Superiority: Why BOPP Lamination Matters
Biaxially Oriented Polypropylene (BOPP) lamination enhances woven bags by adding critical properties for construction applications:
- Moisture Resistance: BOPP films reduce moisture permeability to <1.0 g/m²/24hr, protecting cement and dry mixes from humidity-induced clumping.
- UV Stability: UV inhibitors in BOPP extend outdoor shelf life by 60%, resisting degradation under direct sunlight (tested per ASTM G154).
- Tensile Strength: Virgin PP resin ensures warp/weft tensile strengths of ≥35 MPa and ≥30 MPa, respectively, exceeding ASTM D5035 benchmarks.
Case Study: A UAE construction firm reported zero bag failures during a 2024 desert project using VidePak’s BOPP laminated bags, attributing success to their 12 N puncture resistance and UV-stabilized coatings.
2. Market Adaptability: Tailoring Solutions to Regional Needs
VidePak’s global reach spans 45+ countries, with products customized to regional demands:
A. Quality Differentiation
- Europe: Compliance with EU REACH and OEKO-TEX® standards, emphasizing recyclability (100% PP, resin ID #5).
- Asia-Pacific: Cost-effective, high-volume solutions (e.g., 50kg cement bags with +0.1 mm thickness tolerance to prevent bursting).
- North America: Custom printing with QR codes for supply chain transparency, aligning with FDA and BRCGS requirements.
Region | Key Demand | VidePak Response |
---|---|---|
Middle East | UV/Heat Resistance | BOPP films with 500+ hour weatherability |
Southeast Asia | Moisture Protection | <0.8 g/m²/24hr permeability |
Europe | Sustainability | 30% recycled PP blends (2025 target) |
B. Certification-Driven Trust
VidePak holds ISO 9001, ISO 14001, and SGS certifications, ensuring compliance with global safety and environmental standards.
3. Production Excellence: Starlinger’s Role in Precision Manufacturing
VidePak’s 100+ Starlinger circular looms and 30+ lamination machines enable:
- High-Speed Weaving: 200+ picks per minute (PPM), producing 12×12 strands/inch fabric—20% denser than industry averages.
- Seam Integrity: Ultrasonic welding achieves 80–100 N/cm seam strength, eliminating burst risks during pneumatic filling.
Example: A 2024 audit revealed VidePak’s defect rate of 0.3%—70% lower than competitors—due to AI-driven defect detection systems.
4. Sustainability: Aligning Construction Needs with ESG Goals
While PP is inherently recyclable, VidePak’s 2025 initiatives include:
- Energy Recovery: Starlinger’s heat-exchange systems reuse 85% of extrusion line energy, reducing carbon footprint by 15%.
- Bio-Based Additives: Trials with 20% sugarcane-derived PP aim to launch compostable bags by 2026.
Case Study: A German client reduced landfill waste by 40% after switching to VidePak’s recyclable FIBC bags for construction debris.
FAQs: Addressing Industry Concerns
Q1: How do BOPP bags handle abrasive materials like gravel?
A: VidePak’s PE-coated variants use 30-micron coatings with 12 N puncture resistance, validated by 24-hour load simulations.
Q2: Are BOPP bags cost-effective compared to traditional options?
A: Yes. Bulk production with AI-optimized material use reduces costs by 18%, while durability cuts replacement frequency by 50%.
Q3: Can bags be customized for branding?
A: Absolutely. VidePak’s high-definition printing offers 175 LPI resolution with Pantone-matched colors, enhancing brand visibility.
5. The Future: Smart Packaging and Global Expansion
The construction packaging market is projected to grow at 6.2% CAGR through 2030. VidePak’s roadmap includes:
- NFC Integration: Track inventory via embedded chips (2025 pilot).
- Regional Hubs: Expanding production in Southeast Asia and Africa to reduce logistics costs by 25%.
Conclusion: Building Trust, One Bag at a Time
BOPP woven bags are no longer mere containers—they are engineered solutions bridging durability, sustainability, and brand value. VidePak’s fusion of Starlinger precision, rigorous testing, and ESG-aligned innovation positions it as a leader in the construction sector. As Ray summarizes: “In a world of temporary structures, we deliver permanence.”
For industries seeking certified, high-performance solutions, VidePak remains the benchmark.
Note: All data reflects 2025 industry benchmarks and VidePak’s internal testing protocols.