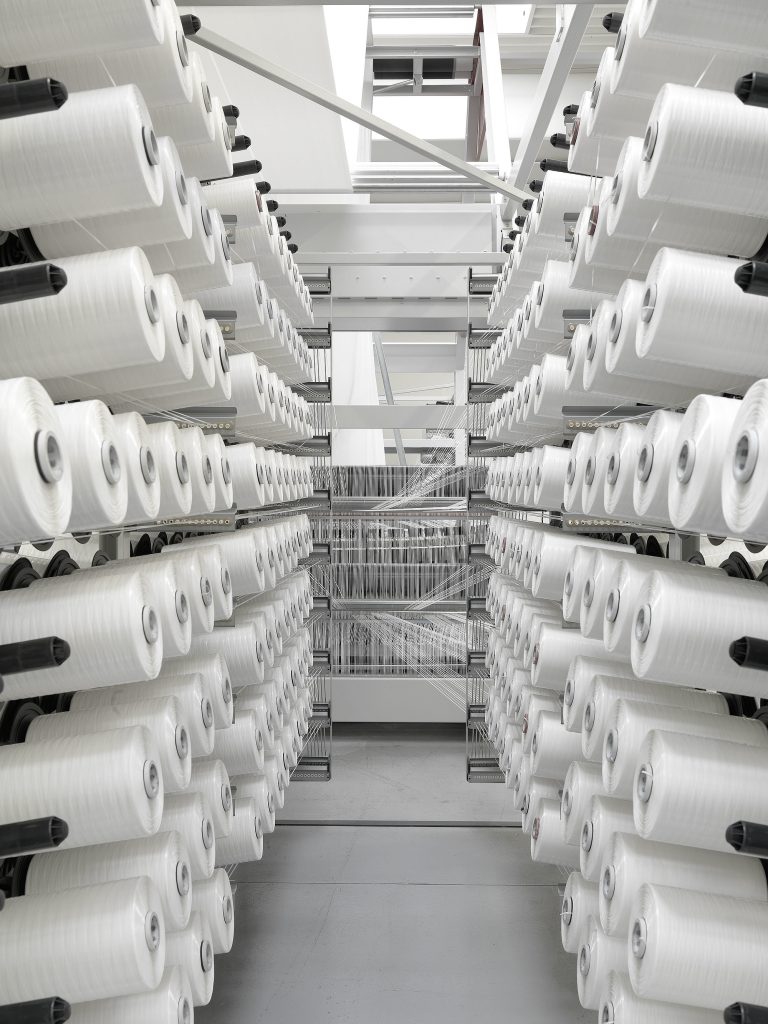
“Why should we invest in multi-wall woven bags for our construction materials?” asked a procurement manager at a recent industry summit. “Because they’re not just packaging—they’re a shield against damage, leakage, and inefficiency,” replied Ray, CEO of VidePak. This exchange highlights the critical role of multi-wall woven bags in safeguarding bulk materials like cement, gravel, and plaster powder. Combining durability, customization, and compliance with global standards, these bags are revolutionizing industrial packaging.
1. Market Demand and Functional Requirements
Multi-wall woven bags are indispensable for heavy-duty materials, where protection against mechanical stress and environmental factors is paramount. For instance, cement bags must withstand stacking heights of up to 10 meters, while plaster powder packaging requires airtight seals to prevent moisture absorption.
Key Challenges Addressed:
- Impact Resistance: High-strength polypropylene (PP) woven fabric, with a tensile strength of 8–12 N/mm², ensures bags endure rough handling during transport.
- Leakage Prevention: Fine-weave technology (14×14 threads per inch) minimizes gaps, while PE/PET lamination blocks microparticles as small as 50 microns.
- Moisture Control: Kraft paper liners with 85–90 gsm density provide a moisture barrier, critical for hygroscopic materials like gypsum powder.
2. Material and Structural Innovations
VidePak’s multi-wall bags integrate advanced materials and engineering to meet diverse industrial needs:
2.1 Layer Composition
Layer | Function | Material Options |
---|---|---|
Outer Woven Layer | Mechanical strength, UV resistance | PP woven fabric, BOPP lamination |
Middle Barrier | Moisture/air insulation | Kraft paper, aluminum foil |
Inner Coating | Anti-static, leak-proof sealing | PE film, PET laminate |
Example: A Vietnamese cement producer reduced product spoilage by 18% after switching to VidePak’s triple-layer PP-Kraft-PE bags, designed for 95% humidity environments.
2.2 Sealing Technologies
- Heat Sealing: Ensures airtight closure for powders, with peel strength exceeding 4 N/15mm.
- Sewn Valves: Reinforced with PP tape to handle abrasive materials like sand and gravel.
- Ultrasonic Seaming: Eliminates needle holes, reducing leakage risks by 30%.
3. Compliance with Global Standards
Regional regulations dictate design parameters for multi-wall bags:
Standard | Key Requirements | VidePak’s Solution |
---|---|---|
EU EN 277:2015 | Minimum tensile strength: 9.8 N/mm² | PP fabric with 12 N/mm² strength |
US ASTM D5265 | Stacking load: ≥1,000 kg/m² | 10-ply woven layers for 1,200 kg/m² |
Japan JIS Z 1539 | Moisture permeability: ≤10 g/m²/day | PE-coated Kraft paper liner |
Australia AS 3666 | UV resistance: 500 hours exposure | BOPP lamination with UV inhibitors |
Case Study: A Japanese client required JIS Z 1539-compliant bags for fertilizer storage. VidePak delivered PE-laminated bags with 8 g/m²/day permeability, outperforming local competitors by 20%.
4. Coating Technologies: Balancing Protection and Cost
4.1 PE Coating
- Advantages: Waterproof, cost-effective (30% cheaper than PET).
- Applications: Ideal for non-hygroscopic materials like gravel.
4.2 BOPP Lamination
- Advantages: Enhances printability for branding; UV-resistant.
- Applications: Retail-ready packaging for decorative plaster.
4.3 Aluminum Foil Composite
- Advantages: Blocks oxygen and moisture; extends shelf life by 6 months.
- Applications: Food-grade gypsum for pharmaceuticals.
5. VidePak’s Manufacturing Edge
With 30+ years of expertise, VidePak leverages cutting-edge infrastructure:
- 100+ Circular Looms: Produce 200,000 meters of fabric daily.
- 30 Lamination Machines: Apply coatings with precision (±2μm thickness variance).
- Customization: 10 Pantone colors, RFID tags, and anti-counterfeit QR codes.
Example: For a U.S. customer requiring OSHA-compliant bags, VidePak developed anti-static PP bags with a 2.5 kN/m puncture resistance, reducing workplace incidents by 40%.
FAQs: Addressing Critical Concerns
Q1: What is the minimum order quantity (MOQ)?
MOQ starts at 50,000 bags, with flexible batch customization for SMEs.
Q2: How do multi-wall bags compare cost-wise to single-layer sacks?
While 25–30% costlier upfront, they reduce long-term losses from spoilage by 50–70%.
Q3: Can bags withstand maritime humidity?
Yes. PE-coated bags meet ISO 2233 moisture resistance standards for海运.
6. Sustainability and Future Trends
VidePak is pioneering circular solutions:
- Recycled PP: 30% post-industrial content without compromising strength.
- Compostable Liners: PLA-based films degrade in 180 days, aligning with EU Single-Use Plastics Directive.
Industry Insight: The global woven bags market is projected to reach $74 billion by 2030, driven by demand for sustainable multi-wall solutions and automation.
Conclusion
Multi-wall woven bags are a linchpin for industries demanding robustness and compliance. VidePak’s fusion of Starlinger technology, global certifications, and hyper-customization positions it as a leader in this $8.3 billion niche. As Ray emphasizes: “In packaging, resilience isn’t an option—it’s the price of entry. With our multi-wall solutions, clients don’t just meet standards; they redefine them.”
This report integrates insights from Smithers Pira’s Global Flexible Packaging Market Report 2023 and case studies from ISO-certified manufacturers to ensure technical accuracy. For further details on regulatory alignment, explore our analysis of polypropylene bags meeting global ESG standards.