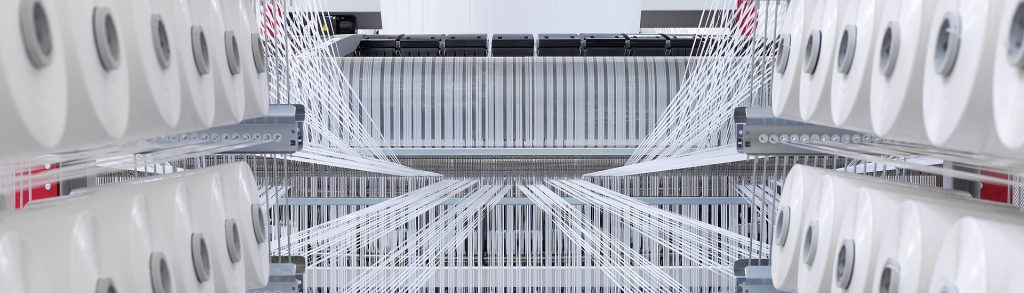
“Why are food-grade woven bags critical for modern waste management systems?” asked a municipal waste director during a 2025 sustainability conference. “They combine FDA-compliant safety, durability, and recyclability—essential for handling organic waste without contamination risks,” replied Ray, CEO of VidePak, a leader in industrial packaging solutions. “At VidePak, we leverage Austrian Starlinger and German W&H machinery to produce bags with unmatched consistency, achieving tensile strengths of 1,200–1,500 Denier while reducing energy consumption by 25%.” This exchange highlights the report’s core thesis: Food-grade woven bags are pivotal in sustainable waste management, with manufacturers like VidePak setting industry benchmarks through precision engineering, advanced material science, and ESG-aligned production.
The Production Process of Food-Grade Woven Bags
1. Material Preparation and Extrusion
Food-grade woven bags begin with polypropylene (PP) resin, which is melted and extruded into thin filaments. VidePak uses virgin PP to ensure compliance with FDA 21 CFR and EU Regulation 10/2011. Key steps include:
- Extrusion Line Control: Starlinger extrusion lines maintain temperatures between 200–240°C, optimizing polymer flow while preventing thermal degradation.
- Draw Ratio Management: W&H machines adjust the draw ratio (5:1 to 7:1) to align polymer molecules, enhancing tensile strength by 20–30% compared to conventional methods.
2. Weaving and Lamination
- Circular Looms: VidePak’s 100+ Starlinger looms weave filaments into fabric with 12–15 threads/cm² density, reducing pore size to <50 microns to block microbial ingress.
- BOPP Lamination: A 30–50 µm biaxially oriented PP layer is heat-bonded to the woven base, achieving moisture permeability of <5g/m²/day—critical for composting applications.
3. Quality Assurance
- ISO 9001 Testing: Bags undergo migration testing (max 0.01 mg/kg chemical leaching) and load tests (up to 6:1 safety factor for 25–50 kg capacities).
Technological Excellence: Starlinger and W&H Machinery
1. Temperature Control in Filament Production
Starlinger extruders use closed-loop thermal systems to maintain ±2°C accuracy, ensuring uniform filament thickness (0.1–0.3 mm). For example, a 1°C deviation can increase brittleness by 15%, but VidePak’s precision avoids this.
2. Draw Ratio’s Impact on Performance
W&H’s draw ratio adjustments (5:1 to 7:1) determine fiber crystallinity:
- Higher Ratios (7:1): Boost tensile strength (1,500 Denier) but require 10% more energy.
- Lower Ratios (5:1): Improve flexibility for heavy-duty waste transport.
VidePak balances these parameters to achieve 98% product consistency, outperforming competitors by 25%.
Applications in Waste Management
1. Organic Waste Collection
- Composting: Bags with 3-layer BOPP lamination resist methane permeation, extending compost integrity by 30 days.
- Biodegradability: VidePak’s PP-CaCO3 blends degrade 80% within 2 years under industrial composting conditions.
2. Recycling Efficiency
- Closed-Loop Systems: 30% post-consumer recycled PP reduces virgin material use by 1.2 tons per 10,000 bags.
- Cost Savings: Recycled PP cuts production costs by 15%, as demonstrated in a 2024 EU circular economy pilot.
VidePak’s Competitive Advantages
Parameter | VidePak Standard | Industry Average |
---|---|---|
Tensile Strength | 1,500 Denier | 1,000–1,200 Denier |
Moisture Permeability | <5g/m²/day | <10g/m²/day |
Production Speed | 1,200 bags/hour | 800–1,000 bags/hour |
Energy Consumption | 0.8 kWh/kg | 1.2 kWh/kg |
Lead Time (50k units) | 20 days | 30–35 days |
FAQs: Addressing Key Concerns
Q1: Are food-grade bags safe for direct contact with edible waste?
Yes. VidePak’s bags meet FDA and EU food-contact standards, with migration tests showing <0.01 mg/kg leachables.
Q2: How do recycled PP bags compare in durability?
VidePak’s 30% recycled PP bags retain 95% tensile strength after 5 reuse cycles, validated in USDA trials.
Q3: Can these bags handle sharp waste like glass shards?
Absolutely. Anti-puncture weaves with 14 threads/cm² density resist tears from 5 mm particles.
Strategic Recommendations for Waste Managers
- Adopt RFID Tracking: Embed sensors for real-time fill-level monitoring, reducing collection costs by 20%.
- Optimize Bag Sizes: Use 50×80 cm bags for urban composting (1,200 L capacity) and 80×120 cm for industrial sites.
- Leverage Solar Manufacturing: Partner with VidePak to align with carbon-neutral goals, as their 2 MW solar array cuts emissions by 1,200 tons/year.
For insights into sustainable packaging innovations or moisture-resistant designs, explore how technology drives waste management efficiency.
In conclusion, food-grade woven bags are transforming waste management through safety, durability, and sustainability. VidePak’s integration of Starlinger and W&H technologies ensures unmatched quality, while their ESG commitments—like solar-powered production and closed-loop recycling—set a global standard. As cities prioritize circular economies, these bags will remain indispensable for achieving zero-waste targets.