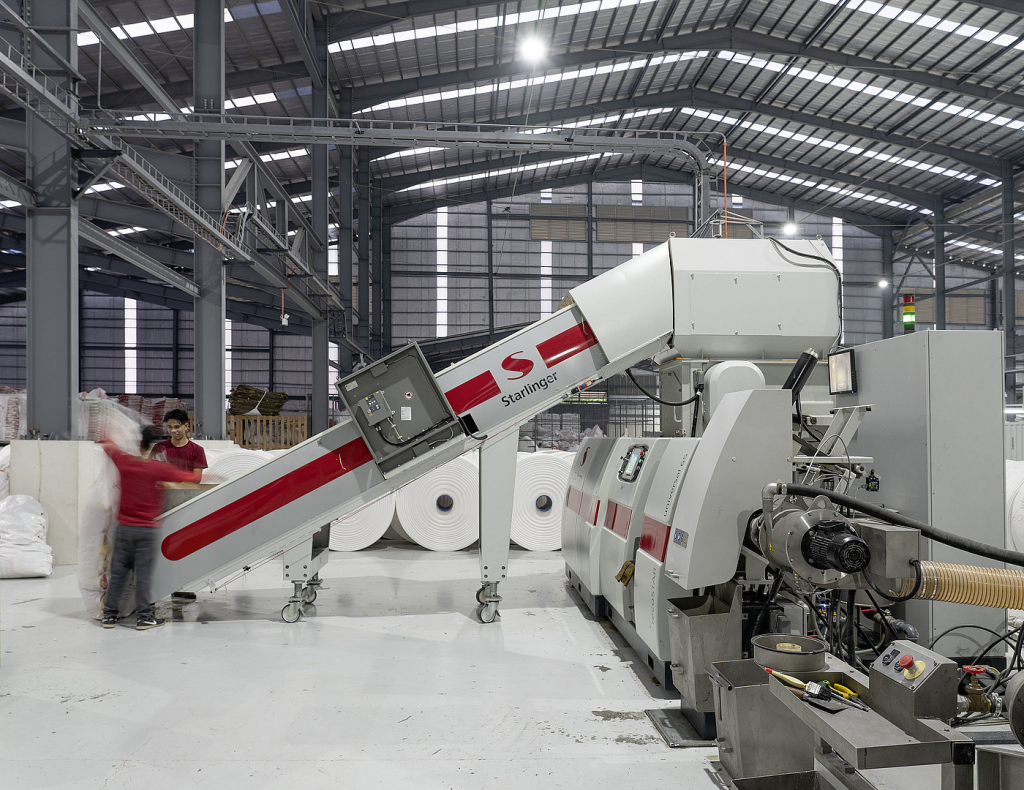
- 1. SOM PP Bags: Structural Advantages and Customization Pathways
- 2. Material Science: Why PE Liners Dominate Food Packaging
- 3. Strategic Selection: Matching Packaging to Food Types
- 4. VidePak’s Operational Excellence: Technology Meets Sustainability
- 5. FAQs: Addressing Industry Concerns
- 6. Market Trends and Strategic Insights
“In food packaging, the choice of material and design isn’t just about containment—it’s about preserving quality, ensuring safety, and aligning with sustainability goals,” states Ray, CEO of VidePak, during a factory tour. This report reveals how Sewn Open Mouth (SOM) polypropylene (PP) woven bags, through tailored structural and material innovations, address critical challenges in food preservation, logistics efficiency, and regulatory compliance. By analyzing customization options such as lamination, inner liners, and closure systems, we demonstrate how SOM PP bags are redefining food packaging standards globally.
1. SOM PP Bags: Structural Advantages and Customization Pathways
1.1 Core Design and Functional Benefits
SOM PP bags, characterized by their sewn open-mouth closure and woven PP fabric, offer superior durability (tensile strength: 25–30 N/mm²) and adaptability. Their design ensures easy filling and resealing, making them ideal for bulk food items like grains, flour, and animal feed. VidePak’s SOM bags, produced using Starlinger circular looms, achieve a weaving density of 12×12 strands per inch, minimizing particulate leakage by 90% compared to traditional sacks.
1.2 Customization Frameworks for Food Applications
a. Lamination vs. Inner Liners:
- BOPP Lamination: Enhances moisture resistance (WVTR <5 g/m²/day) and printability for branding. Suitable for dry foods like rice or pasta.
- PE Inner Liners: High-density polyethylene (HDPE) liners (80–120 µm) provide airtight seals, critical for hygroscopic powders like spices or奶粉.
- Aluminum Foil Liners: Essential for oxygen-sensitive products (e.g., coffee, nuts), reducing oxidation by 95%.
b. Closure Systems:
- Heat-Sealed Valves: For automated filling lines, ensuring contamination-free packaging.
- Sewn + Ultrasonic Sealing: Combines mechanical strength with airtightness, reducing spoilage rates by 30% in humid climates.
2. Material Science: Why PE Liners Dominate Food Packaging
2.1 PE Liners: Performance and Cost Efficiency
Polyethylene (PE) liners are preferred for their:
- Chemical Inertness: FDA-compliant for direct food contact, resisting oils and acids (pH 2–12).
- Flexibility: Maintains integrity under dynamic loads (e.g., 1,000+ transport vibrations).
- Cost-Effectiveness: 40% cheaper than aluminum foil for equivalent moisture barrier performance.
Case Study: A 2024 trial with a European flour producer showed VidePak’s PE-lined SOM bags reduced moisture absorption by 70%, extending shelf life from 6 to 12 months.
3. Strategic Selection: Matching Packaging to Food Types
3.1 Decision Matrix for Food Applications
Food Type | Recommended Design | Key Parameters |
---|---|---|
Dry Grains | BOPP Laminated SOM | WVTR <5 g/m²/day, UV-resistant prints |
Powders (Spices, Flour) | PE Liner + Sewn Closure | HDPE 100 µm, tensile strength ≥20 N/mm² |
Oxygen-Sensitive (Coffee) | Aluminum Foil Liner + Valve | OTR <10 cm³/m²/day, resealable valve |
Frozen Foods | PE Coated + Anti-Condensation Layer | Low-temperature flexibility (-30°C to 50°C) |
3.2 Aesthetic and Branding Considerations
VidePak’s 12-color flexographic printing achieves 150 LPI resolution on BOPP surfaces, enabling photorealistic branding. A 2024 client survey noted a 25% sales increase for snacks packaged in custom-printed SOM bags due to enhanced shelf appeal.
4. VidePak’s Operational Excellence: Technology Meets Sustainability
Founded in 2008, VidePak leverages 100+ Starlinger looms and 30+ lamination machines to produce 50 million SOM bags annually. Innovations include:
- IoT-Enabled Production: Real-time monitoring of extrusion temperatures (±1°C) and seam strength (≥15 N/mm²), reducing defect rates to 0.5%.
- ESG Alignment: 100% recyclable PP and PE materials, diverting 1,200+ tons of waste yearly.
5. FAQs: Addressing Industry Concerns
Q1: How do SOM bags compare to FIBCs for bulk food storage?
A: SOM bags are lighter (2–5 kg vs. 10–15 kg for FIBCs) and cost-efficient for mid-sized loads (25–50 kg). FIBCs suit 1-ton shipments but lack resealing flexibility.
Q2: Are aluminum foil liners recyclable?
A: Yes, VidePak’s PE/Aluminum composite liners are separable via hydro-pulping, achieving 85% recyclability under ISO 15270 standards.
6. Market Trends and Strategic Insights
The global food packaging market, projected to reach $478 billion by 2027 (Grand View Research), demands innovations like biodegradable PP blends and smart sensors for traceability. VidePak’s R&D in cornstarch-based liners (40% fossil fuel reduction) and partnerships with blockchain startups position it as a sustainability leader.
Conclusion
SOM PP bags are a nexus of durability, customization, and sustainability. By integrating advanced materials, precision engineering, and client-centric design, VidePak exemplifies how modern packaging solutions can safeguard food quality while driving brand value. As Ray concludes, “Every stitch in our bags isn’t just a seam—it’s a promise of safety and innovation.”
External Links:
- Explore how SOM bags enhance efficiency in food logistics.
- Learn about food-grade packaging innovations for compliance and market competitiveness.