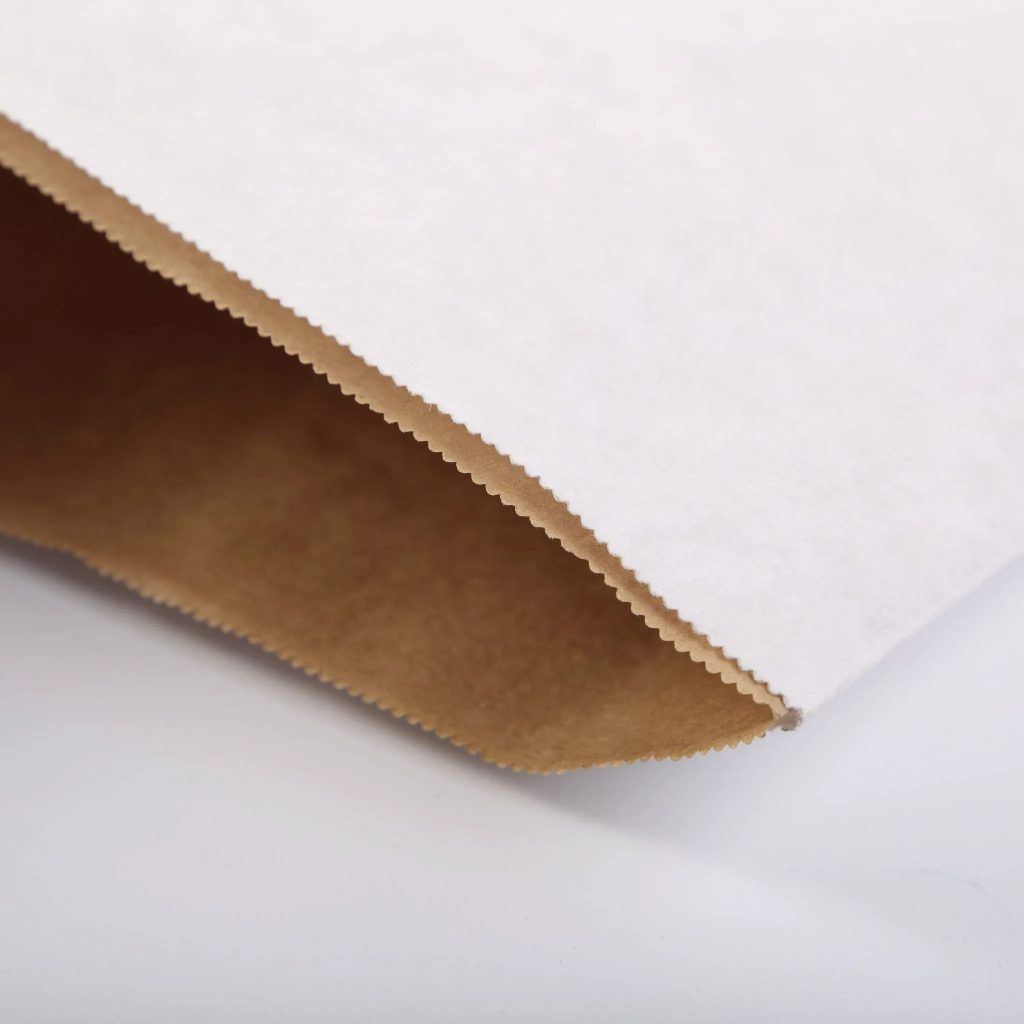
Multiwall Paper Bags have gained significant traction in various industries due to their versatility, strength, and eco-friendliness. These bags are often used for packaging bulk materials like food, chemicals, and construction materials. This article will explore the different types of Multiwall Paper Bags, their structural layers, and the materials used in conjunction with various woven bags, including the unique processes involved in manufacturing them.
Types of Multiwall Paper Bags
Multiwall Paper Bags are designed with multiple layers of paper, providing enhanced strength and durability. The number of layers can vary, typically ranging from two to five or more. Each type serves different purposes based on the specific requirements of the packaged materials.
1. Standard Multiwall Paper Bags
Standard Multiwall Paper Bags are commonly used in packaging applications that require basic protection and structural integrity. They usually consist of two or three layers of kraft paper. The outer layer offers durability and printability, while the inner layers provide additional strength and moisture resistance.
2. Coated Multiwall Paper Bags
Coated Multiwall Paper Bags have a protective coating on the inner or outer surface. This coating can be made from various materials, such as polyethylene (PE) or polypropylene (PP), enhancing the bag’s resistance to moisture and contaminants. These bags are ideal for packaging food products and other sensitive materials.
3. Laminated Multiwall Paper Bags
Laminated Multiwall Paper Bags feature a layer of plastic film bonded to the paper. This laminated layer improves the bag’s barrier properties against moisture, grease, and oxygen. Laminated bags are particularly useful for products that require extended shelf life, such as pet food and bulk grains.
4. Valve Multiwall Paper Bags
Valve Multiwall Paper Bags are equipped with a filling valve that allows for quick and efficient filling using automated processes. These bags are often used for granular products like fertilizers, chemicals, and grains. The valve design minimizes dust and spillage during filling.
Structure of Multiwall Paper Bags
The structure of Multiwall Paper Bags consists of multiple layers, each serving a specific function:
1. Outer Layer
The outer layer is usually made from high-quality kraft paper, which provides strength and printability. This layer is often used for branding and product information, making it visually appealing.
2. Intermediate Layers
The intermediate layers may vary in composition, depending on the intended use of the bag. Some bags may include additional layers of kraft paper for added strength, while others might use layers of plastic or foil to enhance moisture resistance.
3. Inner Layer
The inner layer is crucial for protecting the contents from moisture and contamination. In coated and laminated bags, this layer is typically made from PE or PP, providing a barrier that keeps the contents safe and extends shelf life.
Material Types Used in Woven Bags
Various materials are used in the production of woven bags, each with distinct properties and manufacturing processes. Understanding these differences is essential for selecting the right packaging solution.
1. Polypropylene (PP)
PP is one of the most commonly used materials in woven bag production. It is lightweight, durable, and resistant to moisture. The production process involves extruding the plastic into thin fibers, which are then woven together to form a strong fabric. Kraft Paper PP Bags often combine the strength of paper with the moisture resistance of polypropylene.
2. Polyethylene (PE)
PE is another widely used plastic in woven bags. It is particularly effective for applications requiring a high degree of moisture protection. Like PP, PE is produced through extrusion, and its flexibility makes it ideal for applications where bags need to be pliable.
3. Polyvinyl Chloride (PVC)
PVC is used less frequently in woven bags due to environmental concerns, but it offers excellent strength and durability. It is often used in specialized applications requiring specific chemical resistance. The production process involves polymerizing vinyl chloride monomer to form a plastic that can be woven or molded.
4. Aluminum Foil
Aluminum foil is sometimes used as a barrier layer in multi-layered bags. It provides an excellent barrier against moisture, oxygen, and light, making it ideal for sensitive products such as pharmaceuticals or specialty foods.
Coextrusion Blown Film Process
The coextrusion blown film process is a significant technological advancement in the manufacturing of multilayer films. This process allows for the production of films that combine various materials into a single structure, enhancing the properties of the final product.
1. Process Overview
In coextrusion, multiple layers of different materials are melted and extruded simultaneously through a single die. The result is a film that combines the strengths of each material, such as moisture resistance from PE and strength from PP.
2. Benefits of Coextrusion
The coextrusion process enables manufacturers to create bags with tailored properties, making them suitable for specific applications. For instance, a bag designed for food packaging can have an inner layer of PE for moisture resistance and an outer layer of kraft paper for branding.
Advantages of Multiwall Paper Bags
Multiwall Paper Bags offer numerous advantages, making them a preferred choice for various industries:
1. Environmental Friendliness
Made primarily from renewable resources, Multiwall Paper Bags are more environmentally friendly compared to plastic alternatives. They are recyclable and biodegradable, reducing environmental impact.
2. Customization
Multiwall Paper Bags can be customized in various ways, including size, shape, print, and structure. This flexibility allows manufacturers to cater to specific market needs, enhancing brand visibility and customer satisfaction.
3. Strength and Durability
The multi-layer construction provides superior strength, making these bags ideal for heavy and bulk products. Their resistance to moisture and tearing ensures that the contents remain protected during storage and transportation.
Conclusion
Multiwall Paper Bags represent a versatile and eco-friendly packaging solution suitable for various applications. Understanding the types of Multiwall Paper Bags and their structural components is essential for manufacturers and consumers alike. Coupled with knowledge of woven bag materials and manufacturing processes, businesses can make informed decisions about their packaging needs. As sustainability continues to gain importance, the demand for Multiwall Paper Bags will likely increase, making them a vital component in the future of packaging.
Product Parameters and Key Points
Feature/Parameter | Description |
---|---|
Types of Multiwall Bags | Standard, Coated, Laminated, Valve |
Structural Layers | Outer, Intermediate, Inner |
Materials Used | PP, PE, PVC, Aluminum foil |
Coextrusion Process | Multi-layer film combining various materials |
Environmental Impact | Biodegradable and recyclable |
References
- P. J. Smith, “The Role of Multiwall Paper Bags in Sustainable Packaging,” Journal of Packaging Technology, vol. 28, no. 3, pp. 45-57, 2022.
- R. K. Johnson, “Advancements in Woven Bag Materials,” Materials Science Journal, vol. 19, no. 4, pp. 301-310, 2021.
- T. S. Lee, “Coextrusion Techniques in Packaging,” Polymer Processing Journal, vol. 12, no. 2, pp. 89-95, 2020.
- M. A. Brown, “Multiwall Paper Bags: A Comprehensive Review,” Packaging World, vol. 30, no. 6, pp. 60-75, 2023.