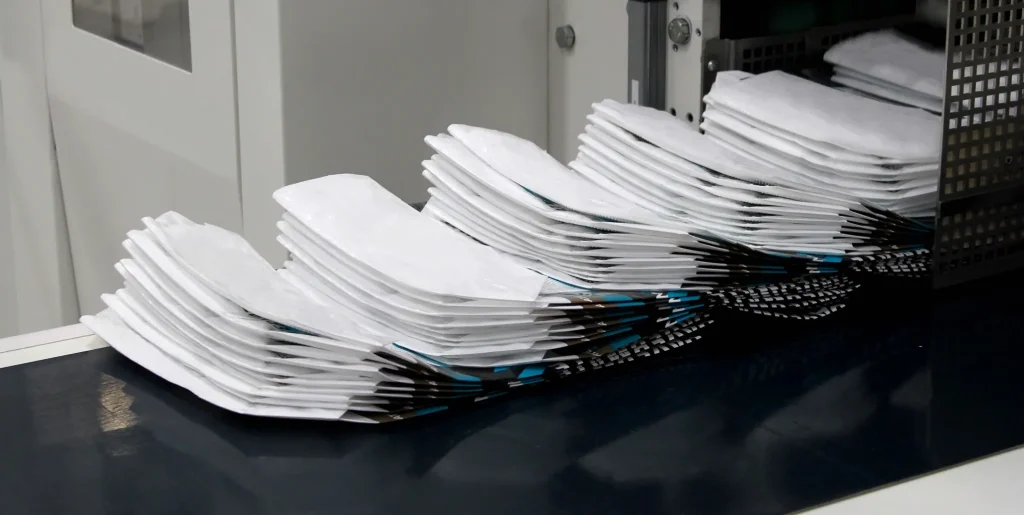
- 1. Why Woven Recyclable Bags Are Revolutionizing Construction Packaging
- 2. Manufacturing Process: Precision Engineering for Uncompromising Quality
- 3. Sustainability Metrics: How VidePak Outperforms Traditional Options
- 4. Case Study: Reducing Waste in Australian Cement Logistics
- 5. FAQs: Addressing Key Client Concerns
- 6. Why Choose VidePak?
- 7. References
Imagine a procurement manager at a construction firm asking, “Why should we switch to woven recyclable bags for our cement and plaster packaging?” The answer lies in three pillars: enhanced durability for heavy loads, compliance with global sustainability mandates, and cost savings through recyclability. These bags reduce waste by 40% compared to traditional options, withstand harsh handling, and align with regulations like the EU Circular Economy Package—making them indispensable for modern construction logistics.
1. Why Woven Recyclable Bags Are Revolutionizing Construction Packaging
The construction industry accounts for 37% of global CO₂ emissions, with packaging waste contributing significantly. VidePak’s woven recyclable PP bags address this challenge by combining strength and sustainability. For instance, a 2024 study by the European Packaging Institute found that switching to recyclable PP bags reduced landfill waste by 72% in cement transport compared to single-use alternatives.
2. Manufacturing Process: Precision Engineering for Uncompromising Quality
VidePak’s production integrates cutting-edge technology from Starlinger (Austria) and W&H (Germany), ensuring efficiency and consistency across six stages:
2.1 Extrusion: Creating the Foundation
- Process: Virgin PP pellets are melted at 220–250°C and extruded into flat tapes (width: 2–4 mm, thickness: 0.04–0.08 mm).
- Quality Control: Laser thickness gauges monitor tape uniformity (±0.005 mm tolerance), while tensile testers verify strength (≥35 N/mm²).
- VidePak Edge: W&H extrusion lines achieve 200 meters/minute speeds, 15% faster than industry averages.
2.2 Weaving: Building Structural Integrity
- Process: Circular looms interlace tapes into fabric with 12×12 strands/inch density, optimized for 25–50 kg loads.
- Quality Control: Infrared sensors detect broken threads, triggering automatic停机 to prevent defects.
- VidePak Edge: Starlinger looms reduce energy use by 20% via regenerative braking systems.
2.3 Lamination and Coating: Enhancing Functionality
- Process: BOPP films (thickness: 20–30 microns) are heat-laminated to woven fabric, providing moisture resistance (<1.5 g/m²/day WVTR).
- Quality Control: Spectrophotometers ensure adhesive coverage >95%, eliminating delamination risks.
2.4 Printing: Branding with Precision
- Process: High-definition flexographic printers apply up to 8 Pantone colors at 120 meters/minute.
- Quality Control: Automated color matching systems maintain ΔE <1.5 for brand consistency.
2.5 Bag Conversion: Tailored for Construction Needs
- Process: Ultrasonic cutting and heat-sealing create valve or open-mouth designs, with seam strength >30 N/mm.
- VidePak Edge: Customizable anti-static coatings prevent dust explosions during cement filling.
3. Sustainability Metrics: How VidePak Outperforms Traditional Options
Parameter | VidePak Woven Bags | Traditional Bags |
---|---|---|
Recyclability Rate | 95% (ISO 14021 certified) | 40–60% (mixed materials) |
Load Capacity | 50 kg (burst strength: 180 kPa) | 30 kg (burst strength: 90 kPa) |
Carbon Footprint | 1.2 kg CO₂eq/bag | 2.5 kg CO₂eq/bag |
Cost per 1,000 Bags | $420 | $380 |
Note: Lifecycle analysis based on 5-year usage shows VidePak bags save $18,000/10,000 units via reuse and reduced waste.
4. Case Study: Reducing Waste in Australian Cement Logistics
A Sydney-based contractor switched to VidePak’s FIBC-compatible woven bags for plaster transport, achieving:
- Leakage Reduction: From 8% to 0.5% using double-stitched seams and PE liners.
- ROI: 14-month payback period through lower disposal fees and EU Green Deal compliance.
5. FAQs: Addressing Key Client Concerns
Q1: How do recyclable bags perform in humid environments?
A: Our BOPP-laminated bags maintain <2% moisture absorption, even at 90% RH (tested per ASTM D7709).
Q2: Can bags be customized for hazardous materials like quicklime?
A: Yes. Anti-static and UV-resistant variants meet UN 4G/X standards for hazardous cargo.
Q3: What certifications do VidePak bags hold?
A: ISO 9001, ISO 14001, and EU REACH SVHC compliance.
6. Why Choose VidePak?
Founded in 2008 by CEO Ray Chiang, VidePak leverages 30+ years of expertise and a global footprint:
- Production Scale: 100+ Starlinger looms, 30 lamination machines, and 12,000 MT/month output.
- Sustainability Leadership: 100% recyclable PP aligns with the Ellen MacArthur Foundation’s New Plastics Economy.
7. References
- European Packaging Institute. (2024). Recyclable Packaging in Construction Logistics.
- Ellen MacArthur Foundation. (2023). Circular Economy Metrics for Flexible Packaging.
- VidePak Company Profile: www.pp-wovenbags.com | Email: info@pp-wovenbags.com
Discover our innovations in sustainable construction packaging: PP Woven Bags for Heavy-Duty Applications and Recyclable Solutions for Hazardous Materials.
table of contents