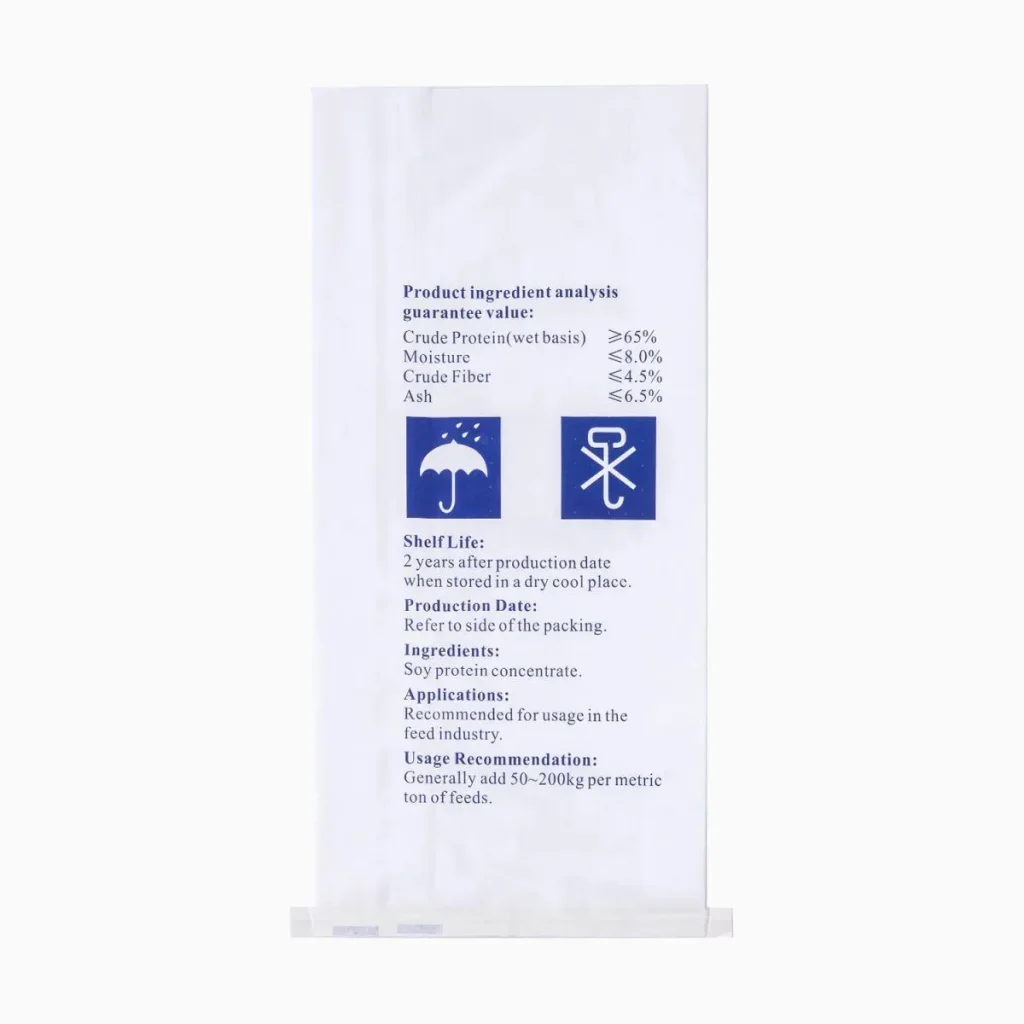
Packaging plays a crucial role in numerous industries, from food and agriculture to chemicals and construction materials. Among the many packaging options available, Multiwall Paper Bags stand out for their strength, versatility, and eco-friendliness. At the same time, woven sacks, particularly Kraft Paper Woven Bags and Kraft Paper PP Bags, are widely used for bulk packaging. One of the most significant challenges for woven bag manufacturers is preventing “burst failures” or “exploding bags,” a serious quality issue that can lead to product loss and customer dissatisfaction.
This article provides an in-depth look at Multiwall Paper Bags, their types and lamination structures, and explores the reasons behind burst failures in woven sacks, particularly focusing on raw material inspection and quality control processes. We will also examine how our company addresses these challenges to ensure high-quality woven bags that meet rigorous performance standards.
Types of Multiwall Paper Bags and Lamination Structures
Multiwall Paper Bags are an excellent packaging solution for many industries, offering high strength and flexibility. These bags are made of multiple layers of paper, often combined with other materials like polyethylene or polypropylene for added durability and moisture resistance.
What Are Multiwall Paper Bags?
Multiwall Paper Bags, sometimes referred to as Multiwall Paper sacks, consist of two or more layers of kraft paper, which are laminated together to enhance strength, moisture resistance, and barrier properties. The multi-layer construction allows these bags to be used for heavy-duty applications such as packaging cement, chemicals, fertilizers, food products, and more.
Types of Multiwall Paper Bags
Multiwall paper bags come in various types, depending on the application. The layers of these bags can vary in material and structure, each serving a different purpose. Here are some common types of multiwall paper bags:
- Open Mouth Bags
These are simple, easy-to-fill bags, often used for agricultural products, food ingredients, and industrial materials. The open-mouth design allows for quick filling, and the top can be stitched or sealed after filling. - Valve Bags
These bags feature a built-in valve that allows for easy filling through a spout. Multiwall Paper Valve Bags are widely used for fine powders and granulated materials like cement, flour, and chemicals. The valve is designed to close automatically after filling, reducing spillage and dust during transport. - Pinch Bottom Bags
These bags have a flat, pinch-closed bottom that provides extra stability for stacking and transporting. They are often used for granular and powdered products. - Sewn Open Mouth (SOM) Bags
These bags are closed using stitching after filling. SOM bags are commonly used for packaging food ingredients, grains, and other bulk products.
Lamination Structures in Multiwall Paper Bags
The lamination structure of Multiwall Paper Bags is what gives them their unique combination of strength, moisture protection, and flexibility. Common lamination layers include:
- Polyethylene (PE) Film: Adds moisture resistance and barrier protection, commonly used in bags for food products or moisture-sensitive chemicals.
- Polypropylene (PP) Woven Fabric: Provides additional strength and durability, making these bags suitable for heavy-duty applications like cement or fertilizer packaging.
- Aluminum Foil: Used as a barrier layer for moisture-sensitive or high-value products, providing an excellent barrier against moisture, oxygen, and light.
Kraft Paper Woven Bags and Kraft Paper PP Bags are often made by laminating kraft paper to woven polypropylene (PP) fabric. This creates a strong yet flexible bag suitable for transporting heavy goods, including agricultural products and industrial materials.
Table 1: Common Lamination Structures in Multiwall Paper Bags
Material Layer | Function | Application |
---|---|---|
Kraft Paper | Structural strength and printability | General packaging for grains, seeds, etc. |
Polyethylene (PE) Film | Moisture resistance | Food products, moisture-sensitive chemicals |
Polypropylene (PP) Woven | Added strength and tear resistance | Heavy-duty materials (cement, fertilizer) |
Aluminum Foil | Moisture, oxygen, and light barrier | High-value products and chemicals |
The Problem of Burst Failures in Woven Sacks
One of the most critical quality issues in the packaging industry is burst failure, particularly in woven sacks used for bulk products. Burst failures, also referred to as “exploding bags,” occur when a bag ruptures under the pressure of its contents, leading to product loss and potential safety hazards.
Why Do Woven Bags Burst?
Burst failures in woven sacks can occur due to various reasons, ranging from material defects to poor manufacturing practices. Here are some of the common causes:
- Low-Quality Raw Materials
The use of substandard raw materials, such as low-quality polypropylene or recycled PP that lacks the necessary tensile strength, can lead to bag failure. Woven sacks must be made from high-quality virgin PP material to ensure strength and durability. - Improper Lamination
In Kraft Paper PP Bags, if the lamination between the paper and PP layer is weak or inconsistent, it can result in separation under stress, leading to a burst failure. - Inadequate Sealing or Stitching
The seams of the woven sacks must be properly sealed or stitched to prevent leakage or failure. Poor stitching can create weak points that compromise the integrity of the bag. - Overloading
Overloading a bag beyond its weight capacity can easily cause it to burst. Manufacturers must ensure that the bag is rated for the correct load capacity and educate customers on proper usage.
Preventing Burst Failures in Woven Sacks: Raw Material and Product Testing
At our company, we take a multi-faceted approach to preventing burst failures in woven sacks, focusing on both the quality of the raw materials we use and rigorous testing of the final product.
Raw Material Inspection
Every batch of raw material, particularly polypropylene, undergoes a series of tests to ensure that it meets our quality standards. This includes checking for tensile strength, consistency, and UV resistance, all of which are critical to ensuring that the woven sacks can withstand heavy loads and exposure to sunlight.
- Tensile Strength Testing: Polypropylene fibers must have high tensile strength to prevent tearing and bursting under heavy loads.
- UV Resistance Testing: Outdoor storage and transport can expose sacks to sunlight, so UV resistance is essential to prevent material degradation.
Finished Product Testing
Once the bags are manufactured, we conduct thorough testing to ensure they meet the necessary quality standards. These tests include:
- Thickness Measurement
The thickness of the bag layers is checked to ensure uniformity and adequate protection. Bags that are too thin may be prone to bursting. - Tensile Strength Testing
This test measures how much force the bag can withstand before tearing. Multiwall Paper Bags and Kraft Paper Woven Bags are tested to ensure that the paper and PP layers can handle heavy loads without separating or failing. - Drop Test
We simulate real-world conditions by dropping bags filled with product from a specific height to ensure they can handle the impacts of transport and handling. - UV Exposure Testing
Woven sacks that will be exposed to outdoor conditions are subjected to UV testing to ensure that they will not degrade under sunlight, particularly important for Kraft Paper PP Bags used in agricultural or construction applications. - Moisture Resistance Testing
For products like fertilizer, moisture can be a major issue. Laminated woven bags with a polyethylene or polypropylene layer are tested to ensure they provide adequate moisture protection. - Visual Inspection
The bags are visually inspected for any defects, such as improper stitching, lamination gaps, or surface irregularities. This step ensures that the bags not only perform well but also look professional.
Table 2: Key Testing Procedures for Woven Sacks
Test Type | Purpose | Importance |
---|---|---|
Tensile Strength Test | Ensures the bag can handle heavy loads | Prevents tearing or bursting |
Drop Test | Simulates real-world transport conditions | Ensures bags can withstand handling and impact |
UV Exposure Test | Tests resistance to sunlight exposure | Prevents degradation in outdoor storage |
Moisture Resistance Test | Tests for water and moisture protection | Essential for moisture-sensitive products |
Visual Inspection | Ensures the final product is free of defects | Guarantees professional appearance and quality |
How Our Company Ensures High-Quality Woven Sacks
At our company, we have implemented a comprehensive quality control system that combines state-of-the-art technology and rigorous testing to ensure that every batch of Kraft Paper Woven Bags, Kraft Paper PP Bags, and Multiwall Paper Bags meets industry standards and customer expectations. Our processes include:
- Supplier Vetting: We only work with trusted suppliers for raw materials, ensuring consistency in quality.
- Automated Manufacturing: Our production lines use advanced machinery to ensure uniformity in lamination and stitching, reducing the risk of human error.
- Real-time Monitoring: Every step of the manufacturing process is monitored in real-time, allowing for immediate correction if any issues are detected.
- Batch Testing: We conduct random batch testing on all products to ensure that quality is maintained across large production runs.
By focusing on both raw material quality and comprehensive product testing, we can confidently say that our woven sacks are among the most reliable in the industry.
Conclusion
**