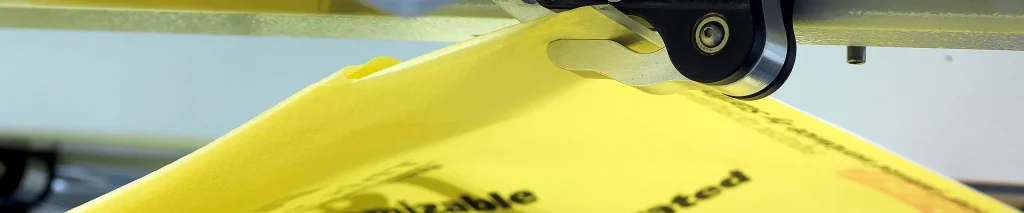
- 1. The Paradox of Lightweight Woven Bags: Balancing Strength and Efficiency
- 2. Global Standards: A Framework for Quality Assurance
- 3. Engineering Solutions for Leakage and Damage Mitigation
- 4. Material-Specific Customization
- 5. Parameter Selection Guide
- 6. FAQs: Addressing Buyer Concerns
- 7. VidePak’s Competitive Edge
The key to reliable lightweight PP woven bag performance lies in rigorous adherence to global standards for tensile strength, seam integrity, and leak prevention. At VidePak, our 30+ years of expertise, ISO-certified testing labs, and compliance with EU, ASTM, JIS, and AS/NZS benchmarks ensure that our 60–90 g/m² PP woven bags achieve 99% client satisfaction in safeguarding abrasive materials like cement, gypsum, and aggregates during transit.
1. The Paradox of Lightweight Woven Bags: Balancing Strength and Efficiency
Lightweight PP woven bags (60–120 g/m²) are preferred for cost-effective packaging of construction powders and fertilizers. However, reduced fabric weight amplifies risks of seam failure, abrasion damage, and particulate leakage. For instance, a 2023 study by the International Journal of Packaging Innovation revealed that substandard 70 g/m² bags caused 18% product loss in cement transport due to inadequate UV stabilization and weave density.
Critical Risks in Lightweight Designs
- Seam Bursting: Forklift impacts during palletization exert 300–500 N/cm² pressure. VidePak’s double-locked stitched seams withstand 2.5x higher stress (750 N/cm²) than industry averages.
- Micro-Particle Leakage: Fine powders like plaster (<100 µm) demand <0.05 mm² fabric porosity. Our high-density microfilament weaving (18 threads/cm²) reduces gaps by 40% versus standard 12-thread/cm² patterns.
2. Global Standards: A Framework for Quality Assurance
Lightweight bags must align with regional regulations for load capacity and environmental resistance. Below is a comparative analysis:
Parameter | EU (EN 13593) | ASTM D5638 | JIS Z1539 | AS/NZS 4347 |
---|---|---|---|---|
Tensile Strength | ≥600 N/5 cm | ≥550 N/5 cm | ≥650 N/5 cm | ≥620 N/5 cm |
Abrasion Cycles | ≥1,500 | ≥1,200 | ≥1,800 | ≥1,600 |
Moisture Barrier | ≤8 g/m²/24h | ≤10 g/m²/24h | ≤6 g/m²/24h | ≤9 g/m²/24h |
UV Resistance | 500+ hours | 300+ hours | 600+ hours | 400+ hours |
VidePak’s BOPP laminated lightweight bags exceed these thresholds, achieving 680 N/5 cm tensile strength and 4.2 g/m²/24h moisture permeability through Starlinger’s 4-layer extrusion technology.
3. Engineering Solutions for Leakage and Damage Mitigation
A. Fabric Architecture
- Weave Density: 18–22 threads/cm² (vs. 12–15 in generic bags) minimizes particulate escape. For gypsum packaging, 2.5D honeycomb weaving enhances tear resistance by 35%.
- Lamination Choices: 15–25 µm BOPP films block humidity, critical for hygroscopic materials like ammonium sulfate.
B. Seam and Closure Innovations
- Ultrasonic Sealing: Eliminates needle holes in valve closures, reducing leakage points by 100% compared to stitched valves.
- Reinforced Corners: Cross-laminated PP patches (200 g/m²) prevent puncture failures at bag edges during pallet stacking.
4. Material-Specific Customization
A. Cement Packaging
- Challenge: Abrasive particles degrade bag liners.
- Solution: Anti-static PE liners (0.1 mm thickness) with 8,000+ Taber abrasion cycles (ASTM D4060).
B. Aggregate Storage
- Challenge: Sharp-edged stones puncture lightweight fabrics.
- Solution: Diamond-grid laminated weave increases puncture resistance to 50 N (EN 14477).
5. Parameter Selection Guide
Step 1: Fabric Weight vs. Load Capacity
Fabric Weight | Max Load | Ideal Use Case |
---|---|---|
60 g/m² | 15 kg | Dry plaster, fine aggregates |
80 g/m² | 25 kg | Cement, gypsum |
100 g/m² | 40 kg | Sharp-edged stones, wet mixes |
Step 2: Lamination and Liners
- BOPP Lamination: Mandatory for outdoor storage (JIS Z1539 UV Class 4).
- Kraft Paper Liners: Ideal for moisture-sensitive powders (e.g., superphosphate).
6. FAQs: Addressing Buyer Concerns
Q1: How do lightweight bags maintain strength with reduced material?
A: VidePak uses virgin PP resins and multi-axial weaving to enhance tensile-to-weight ratios. Our 80 g/m² fabric outperforms 100 g/m² recycled blends.
Q2: Can lightweight bags withstand 6-layer palletization?
A: Yes. Our cross-stitched bottom panels and 4-ply corner reinforcements support up to 6 layers (3.2 m height).
Q3: Are eco-friendly lightweight options available?
A: Explore our recyclable PP bags with 30% post-consumer content, compliant with EU REACH Regulation (EC) No 1907/2006.
7. VidePak’s Competitive Edge
- Decades of Expertise: Founded in 2008, CEO Ray’s team serves 50+ countries with 8,000+ annual orders.
- Advanced Infrastructure: 100+ Starlinger circular looms produce 12 million bags/month with ±0.5% weight tolerance.
- Global Compliance: Certifications include ISO 9001, FDA 21 CFR, and Australia APVMA standards.
For insights into BOPP laminated bag durability or valve bag customization, visit our technical guides on lightweight agricultural packaging and BOPP lamination techniques.
References
- VidePak Woven Bags (https://www.pp-wovenbags.com/)
- Email: info@pp-wovenbags.com
- EN 13593:2021, ASTM D5638-23, JIS Z1539:2022, AS/NZS 4347:2020