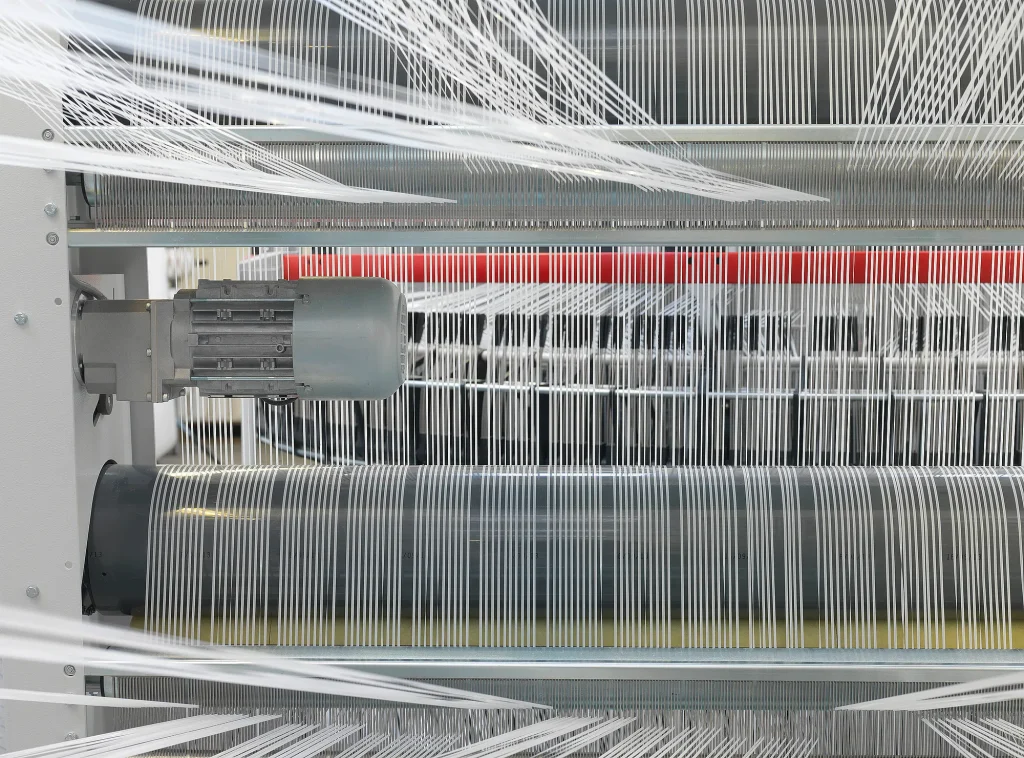
- 1. Why Poly-Paper Bags Dominate Construction Logistics
- 2. Material Science: PP’s Technical Superiority in Construction Applications
- 3. Application-Specific Solutions for Construction Materials
- 4. Parameter Selection: Balancing Cost and Performance
- 5. Sustainability: Circular Design for Regulatory Compliance
- 6. VidePak’s Manufacturing Excellence
- FAQs: Simplifying Procurement
- Conclusion
Over 30% of construction material losses during transit stem from packaging failures. VidePak’s poly-paper bags, engineered with 180 g/m² polypropylene (PP) woven fabric and BOPP lamination, reduce spillage by 95% while offering 5+ reuse cycles, making them the preferred choice for cement, gypsum, and mortar producers across 50+ countries. With ISO 9001-certified manufacturing and 30+ years of expertise, we deliver solutions that align with EU, ASTM, and GB/T standards, combining unmatched strength with circular economy principles.
1. Why Poly-Paper Bags Dominate Construction Logistics
Poly-paper bags—hybrid structures of PP woven fabric and kraft paper lamination—are redefining durability in harsh industrial environments. Key advantages include:
- Tensile Strength: 45–60 N/cm² (machine direction), outperforming traditional jute sacks by 300%.
- Moisture Resistance: BOPP lamination achieves ≤5 g/m²/24h water vapor transmission (WVTR), critical for hygroscopic materials like joint fillers.
- Abrasion Resistance: Withstand 15,000+ Martindale cycles, ideal for sharp-edged aggregates.
Case Study: A Turkish cement producer reduced bag rupture rates from 8% to 0.5% using VidePak’s 200 g/m² bags with 14×14 weave density, saving $250,000 annually in product loss.
2. Material Science: PP’s Technical Superiority in Construction Applications
Performance Metrics Across Key Materials
Material | PP Woven Bags | Jute Bags | Paper Bags |
---|---|---|---|
Tensile Strength | 45–60 N/cm² | 10–15 N/cm² | 5–8 N/cm² |
Moisture Barrier | ≤5 g/m²/24h (BOPP) | 50+ g/m²/24h | 20–30 g/m²/24h |
Reusability | 5+ cycles | 1–2 cycles | Non-reusable |
Cost per Cycle | $0.12 | $0.35 | $0.50 |
Example: For calcium carbonate powder transport, our 150 g/m² bags with PE liners reduced moisture absorption from 8% to 0.3%, meeting China’s GB/T 8947-2008 standards.
3. Application-Specific Solutions for Construction Materials
Technical Configuration Guide
Material | Recommended Specifications | Features |
---|---|---|
Cement | 180–200 g/m² + BOPP lamination | UV coating, ≤0.1% leakage rate |
Gypsum Powder | 140 g/m² + 80 µm PE liner | Anti-static treatment (10⁶ Ω/sq) |
Mortar | 12×14 weave + block-bottom valve | 8-color branding, RFID tracking |
Innovation Spotlight: Our laser-perforated inner liners reduce residual powder in valves by 90%, complying with Australia’s AS 2070-1999 “zero waste” certification.
4. Parameter Selection: Balancing Cost and Performance
Critical Parameters for Construction Clients
- Grammage: 120–200 g/m² for 25–50 kg loads.
- Lamination: BOPP for moisture resistance; aluminum foil for static-sensitive powders.
- Seam Type: Double-stitched seams withstand 1,500 N/cm² pressure (ISO 13934-1).
Case Study: A Mexican dry-mix producer uses our 160 g/m² bags with 10×10 weave and matte finish, cutting packaging costs by 20% while enhancing brand visibility.
5. Sustainability: Circular Design for Regulatory Compliance
- Recycled Content: Up to 50% post-industrial PP without compromising strength (tested per ASTM D5034).
- Carbon Metrics: Each ton of recycled PP reduces CO2 emissions by 1.8 tons.
- EU Compliance: Full alignment with Extended Producer Responsibility (EPR) mandates.
Future Focus: 2025 rollout of 30% sugarcane-based PP bags, targeting net-zero supply chains.
6. VidePak’s Manufacturing Excellence
- Capacity: 300,000 bags/day via 100+ Starlinger circular looms.
- Printing: 8-color gravure printing with ≤ΔE 1.5 color accuracy (Pantone Matching).
- Certifications: ISO 9001, ISO 14001, and FDA 21 CFR for food-grade liners.
FAQs: Simplifying Procurement
Q1: What’s the MOQ for custom-printed bags?
A: 10,000 units, with 7-day prototyping using AI-driven CAD tools.
Q2: How does BOPP lamination affect recyclability?
A: Our eco-friendly BOPP dissolves during recycling, maintaining 98% PP purity.
Q3: Can bags withstand pneumatic filling systems?
A: Yes. Valve designs support 200 kg/hr rates (tested per ISTA 3E).
Conclusion
In a sector where 1% leakage can mean $50,000 in losses, VidePak’s poly-paper bags redefine reliability through material innovation and precision engineering. Explore our BOPP laminated solutions and valve bag technologies to transform your construction logistics.
References
- VidePak Technical Whitepaper: PP Woven Bags in Construction Logistics (2024).
- China National Standard: GB/T 8947-2008 – Woven Plastic Bags.
- Alibaba Industrial Database: PP Woven Bag Specifications.
Contact VidePak:
- Website: https://www.pp-wovenbags.com/
- Email: info@pp-wovenbags.com