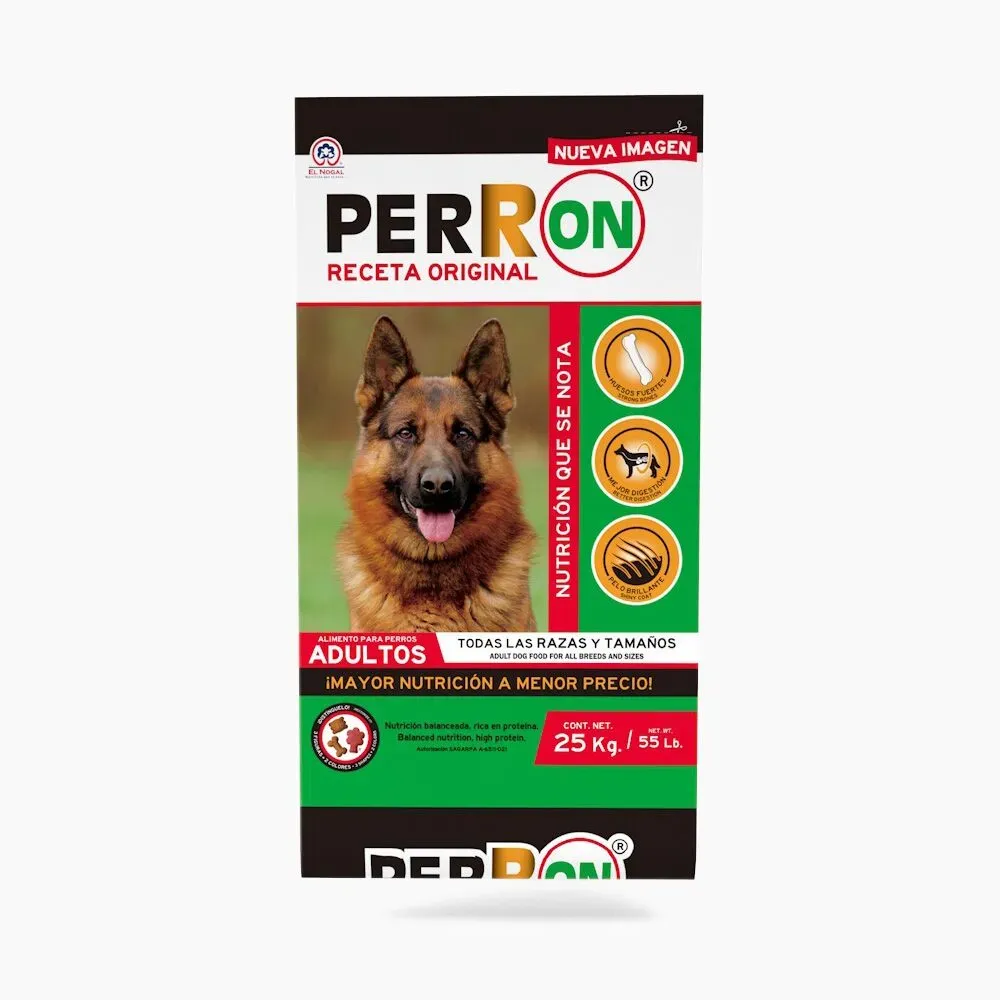
In the packaging industry, the choice of materials is crucial for ensuring product safety, durability, and efficiency. Two popular options that often come into play are BOPP laminated woven bags and multi-wall woven bags. Each has its unique characteristics and advantages, making them suitable for different applications. This blog will explore the distinctions between these two types of bags while delving into the manufacturing processes and technologies used to ensure quality and efficiency, specifically those from the renowned equipment supplier Starlinger.
What Are BOPP Laminated Woven Bags?
BOPP Laminated Woven Bags are made from woven polypropylene (PP) fabric that has been laminated with a layer of Biaxially Oriented Polypropylene (BOPP). This lamination enhances the bag’s appearance, durability, and moisture resistance. BOPP bags are often used in applications requiring a strong, visually appealing packaging solution.
Key Features of BOPP Laminated Woven Bags
- High-Quality Printability: The BOPP layer allows for high-quality, vibrant printing, making them ideal for branding and marketing.
- Moisture Resistance: The lamination provides a barrier against moisture, making these bags suitable for storing food products, chemicals, and other moisture-sensitive materials.
- Durability: The combination of woven fabric and BOPP lamination results in a strong bag capable of holding heavy loads without tearing.
- Versatility: BOPP laminated woven bags are suitable for various applications, including agriculture, food packaging, and construction materials.
What Are Multi-Wall Woven Bags?
Multi-Wall Woven Bags consist of multiple layers of woven fabric, often including both polypropylene and paper layers. These bags are designed to provide enhanced strength and protection for their contents, making them suitable for bulk packaging.
Key Features of Multi-Wall Woven Bags
- Increased Strength: The multi-layer design offers enhanced strength and puncture resistance, making them suitable for heavy and sharp-edged products.
- Superior Protection: The layers help protect the contents from external factors such as moisture, dust, and UV rays.
- Customizable Design: Multi-wall bags can be customized in terms of size, thickness, and the number of layers, allowing for specific applications.
- Eco-Friendly Options: Some multi-wall bags can be made from biodegradable materials or recycled paper, appealing to environmentally conscious consumers.
Differences Between BOPP Laminated Woven Bags and Multi-Wall Woven Bags
Feature | BOPP Laminated Woven Bags | Multi-Wall Woven Bags |
---|---|---|
Material Composition | Woven PP with BOPP lamination | Multiple layers of PP and/or paper |
Moisture Resistance | High | Moderate (depends on materials used) |
Print Quality | Excellent | Good (usually lower quality than BOPP) |
Strength | Strong, but limited by lamination | Very strong due to multiple layers |
Weight Capacity | Suitable for lighter to medium loads | Ideal for heavy and bulk items |
Customization | Custom designs available | Highly customizable |
The Manufacturing Process
To ensure the quality and efficiency of both BOPP laminated woven bags and multi-wall woven bags, state-of-the-art manufacturing processes are employed. Starlinger, a leading global supplier of packaging machinery, provides equipment for every step of the production process. Here’s a closer look at the stages involved in producing these bags:
1. Extrusion
The first step in manufacturing woven bags is the extrusion of polypropylene. This process involves melting plastic pellets and forming them into a continuous sheet. The quality of the extruded material is crucial, as it affects the strength and durability of the final product.
2. Circular Loom Weaving
Once the polypropylene is extruded, it is fed into circular looms, where it is woven into fabric. Starlinger’s advanced circular looms are known for their efficiency and precision, allowing manufacturers to create strong, high-quality woven fabric.
3. Printing
For BOPP laminated woven bags, the next step is printing. The woven fabric is printed with high-quality inks, allowing for vibrant colors and intricate designs. The BOPP lamination process then follows, sealing the printed fabric to enhance durability and moisture resistance.
4. Lamination
In the lamination stage, a layer of BOPP is applied to the woven fabric. This layer adds additional strength and creates a barrier against moisture, ensuring the contents are well-protected.
5. Multi-Wall Formation
For multi-wall woven bags, the manufacturing process involves stacking multiple layers of woven fabric (PP and/or paper). These layers are sewn or glued together, providing the added strength and protection needed for heavy products.
6. Quality Control
Throughout the manufacturing process, quality control measures are in place to ensure that each bag meets industry standards. This includes testing for strength, moisture resistance, and print quality.
Advantages of Using Starlinger Equipment
Using equipment from Starlinger comes with numerous benefits:
- Efficiency: Their machines are designed to optimize production speeds, reducing lead times.
- Precision: The advanced technology used in Starlinger’s equipment ensures that each bag is produced with precision, maintaining consistent quality.
- Flexibility: Starlinger machines can accommodate various bag designs and sizes, making it easy to switch between different product lines.
- Sustainability: Starlinger is committed to producing machinery that minimizes waste and energy consumption, contributing to a more sustainable packaging industry.
Product Parameters of BOPP and Multi-Wall Woven Bags
The following table summarizes the typical parameters for BOPP laminated woven bags and multi-wall woven bags:
Product Parameter | BOPP Laminated Woven Bags | Multi-Wall Woven Bags |
---|---|---|
Material | Woven polypropylene + BOPP | Multi-layer PP and/or paper |
Thickness | 70-150 gsm | 90-300 gsm |
Weight Capacity | Up to 50 kg | Up to 100 kg |
Dimensions | Customizable | Customizable |
Moisture Resistance | High | Moderate to High |
Print Quality | High-quality, vibrant colors | Good quality, typically lower than BOPP |
Closure Type | Heat sealed or stitched | Stitched or glued |
Usage | Food packaging, chemicals, etc. | Heavy-duty products, construction, etc. |
Conclusion
In summary, both BOPP laminated woven bags and multi-wall woven bags offer unique benefits and applications in the packaging industry. Understanding the differences between these two types of bags, as well as the advanced manufacturing processes employed, can help businesses make informed decisions about their packaging needs. With the expertise and technology provided by Starlinger, manufacturers can ensure high-quality, efficient production of these essential packaging solutions.
Final Thoughts
As a leading BOPP Bags Manufacturer, BOPP Woven Bags Supplier, and BOPP Sacks Manufacturer, it is crucial to stay ahead in the industry by adopting the best practices and equipment. Understanding the differences between various bag types and utilizing advanced technology will not only enhance product quality but also contribute to a sustainable and efficient packaging industry.