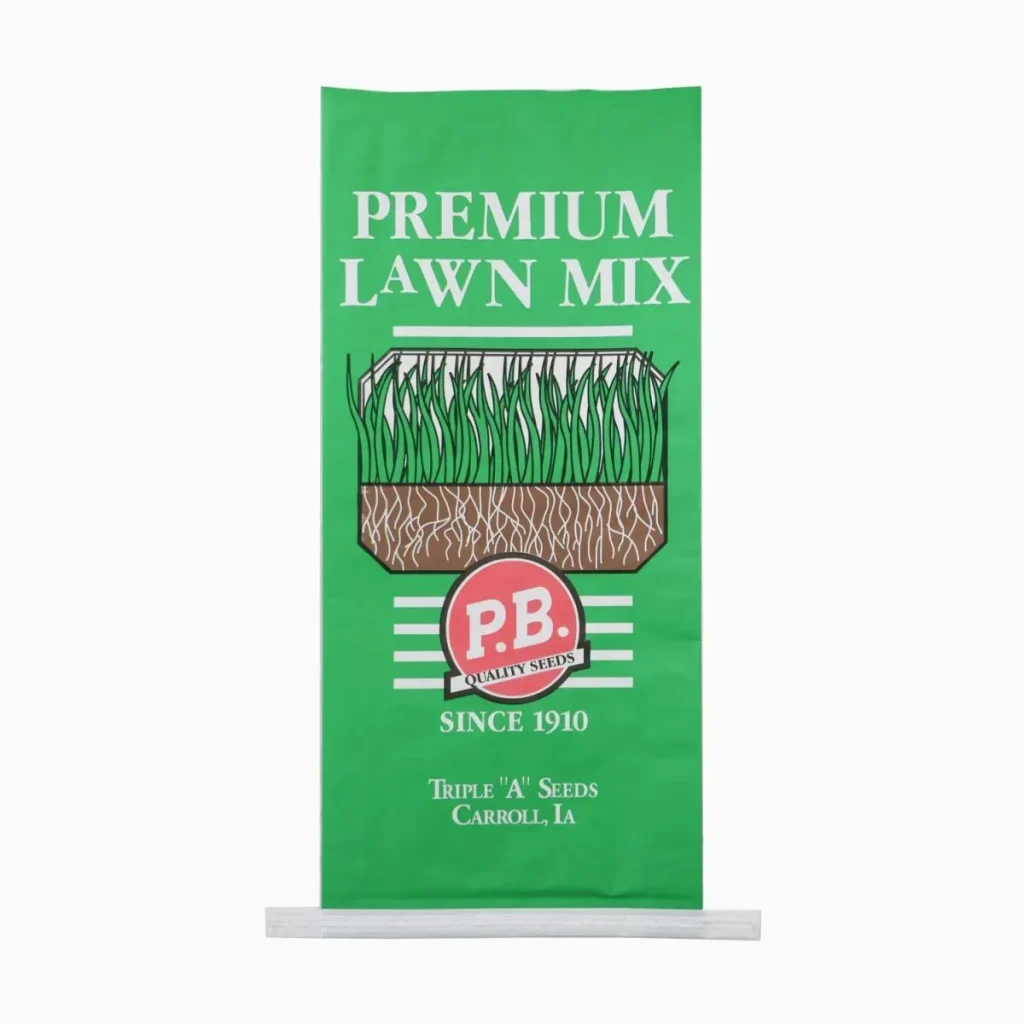
Kraft paper bags laminated with woven fabric represent a robust packaging solution tailored for a variety of industrial applications. These bags are especially valuable in the chemical industry, where they are used for packaging raw materials such as titanium dioxide, color pigments, calcium titanate, silicone powder, latex powder, sodium carbonate, and zinc sulfate. In this blog, we will explore the features of Kraft Paper PP Bags, discuss how they prevent leakage of fine powder particles, and delve into their manufacturing and design techniques.
What Are Kraft Paper Bags Laminated with Woven Fabric?
Kraft Paper Bags laminated with woven fabric combine the durability of woven polypropylene (PP) with the natural strength and moisture resistance of Kraft paper. This combination results in a packaging solution that is not only sturdy but also environmentally friendly.
Key Features of Kraft Paper PP Bags
- Strength and Durability: The woven fabric provides excellent tensile strength, making these bags capable of withstanding heavy loads.
- Moisture Resistance: The Kraft paper layer acts as a barrier against moisture, protecting the contents from environmental conditions.
- Versatile Applications: These bags can be used for a wide range of products, particularly in the chemical industry, where fine powders are common.
- Eco-Friendly: Kraft paper is biodegradable, and when combined with recyclable polypropylene, it represents a more sustainable packaging option.
Applications in the Chemical Industry
Kraft Paper PP Bags are widely used in the chemical industry for packaging various powder materials. Here are some examples of these applications:
- Titanium Dioxide: A widely used white pigment in paints and coatings.
- Color Pigments: Used in a variety of applications, including plastics and coatings.
- Calcium Titanate: Utilized in various chemical processes.
- Silicone Powder: Important for its properties in sealants and adhesives.
- Latex Powder: Used in a range of products, including paints and coatings.
- Sodium Carbonate: Commonly known as soda ash, used in glass manufacturing.
- Zinc Sulfate: Important in agriculture and various chemical processes.
Preventing Powder Leakage: Key Strategies
Packaging fine powders presents unique challenges, primarily due to their tendency to leak. Here are several methods used in Kraft Paper Bags to prevent the escape of powder particles:
1. Outer Lamination
Laminating Kraft paper with woven fabric not only enhances durability but also provides a protective barrier against moisture and environmental factors. The lamination process creates a smooth, sealed surface that minimizes the potential for leakage.
Feature | Benefits |
---|---|
Moisture Barrier | Protects contents from humidity and moisture. |
Enhanced Strength | Increases the tensile strength of the bag. |
Smooth Surface | Reduces friction and prevents powder clumping. |
2. Internal Liners
Incorporating internal liners made from polyethylene (PE) or other moisture-resistant materials can further enhance the bag’s protective qualities. These liners act as an additional barrier against leakage and contamination, ensuring that the chemical powders remain secure.
Liner Type | Material | Benefits |
---|---|---|
Polyethylene (PE) | Flexible and moisture-resistant | Prevents leakage and moisture ingress. |
BOPP (Biaxially Oriented Polypropylene) | Strong and durable | Adds an extra layer of protection against leakage. |
3. Tight Weaving Techniques
The manufacturing process of woven fabrics can be adjusted to improve the tightness and density of the weave. A tighter weave reduces the size of the gaps between fibers, minimizing the risk of powder leakage.
Weaving Technique | Description | Benefits |
---|---|---|
Standard Weave | Basic weaving pattern with moderate density. | Suitable for lightweight applications. |
Reinforced Weave | Tighter interlacing of fibers for added strength. | Ideal for heavy-duty applications with fine powders. |
4. Sealing Technologies
Proper sealing of the bags is crucial for preventing leakage. Advanced sealing techniques ensure that the bags remain intact during transport and handling.
Sealing Method | Description | Benefits |
---|---|---|
Heat Sealing | Using heat to fuse the edges of the bag. | Provides a strong, leak-proof seal. |
Stitching | Sewing the edges with durable thread. | Adds an extra layer of security against leakage. |
Parameters of Kraft Paper PP Bags
To further understand the specifications of Kraft Paper PP Bags, here is a table detailing key parameters:
Parameter | Typical Value | Description |
---|---|---|
Material | Kraft Paper + Woven PP | Combination of Kraft paper and polypropylene. |
Weight Capacity | 5 – 50 kg | Varies based on size and material thickness. |
Thickness | 60 – 120 microns | Depending on the application and material used. |
Dimensions | Customized (e.g., 50×80 cm) | Size can be tailored to specific requirements. |
Closure Type | Valve or sewn | Various closure options available. |
Quality Control in Manufacturing
Maintaining high quality is crucial in the production of Kraft Paper PP Bags. Manufacturers often implement strict quality control measures throughout the production process to ensure that every bag meets industry standards.
- Material Selection: Using high-quality Kraft paper and polypropylene ensures durability and reliability in the final product.
- Production Standards: Manufacturers follow established guidelines and standards to maintain consistent quality and performance.
- Testing Procedures: Regular testing for tensile strength, seal integrity, and moisture resistance ensures that bags are suitable for their intended applications.
Sustainability and Environmental Impact
As environmental concerns continue to grow, the packaging industry is shifting towards more sustainable solutions. Kraft Paper PP Bags are an eco-friendly choice as they are made from renewable resources and can be recycled.
- Biodegradability: Kraft paper is biodegradable, contributing to reduced landfill waste when disposed of properly.
- Recyclability: The combination of Kraft paper and polypropylene can often be recycled, reducing environmental impact.
Conclusion
Kraft Paper Bags laminated with woven fabric provide an effective solution for packaging a wide range of chemical powders. Their unique design, coupled with advanced features such as moisture resistance, tight weaving, and secure sealing, ensures that they meet the rigorous demands of the chemical industry. By understanding how these bags prevent leakage and the customization options available, businesses can make informed decisions about their packaging needs, enhancing both performance and sustainability.
In summary, whether for Kraft Paper PP Bags, Kraft Paper Woven Bags, or Paper Valve Woven Bags, the right packaging solution can significantly impact product quality, safety, and environmental responsibility.