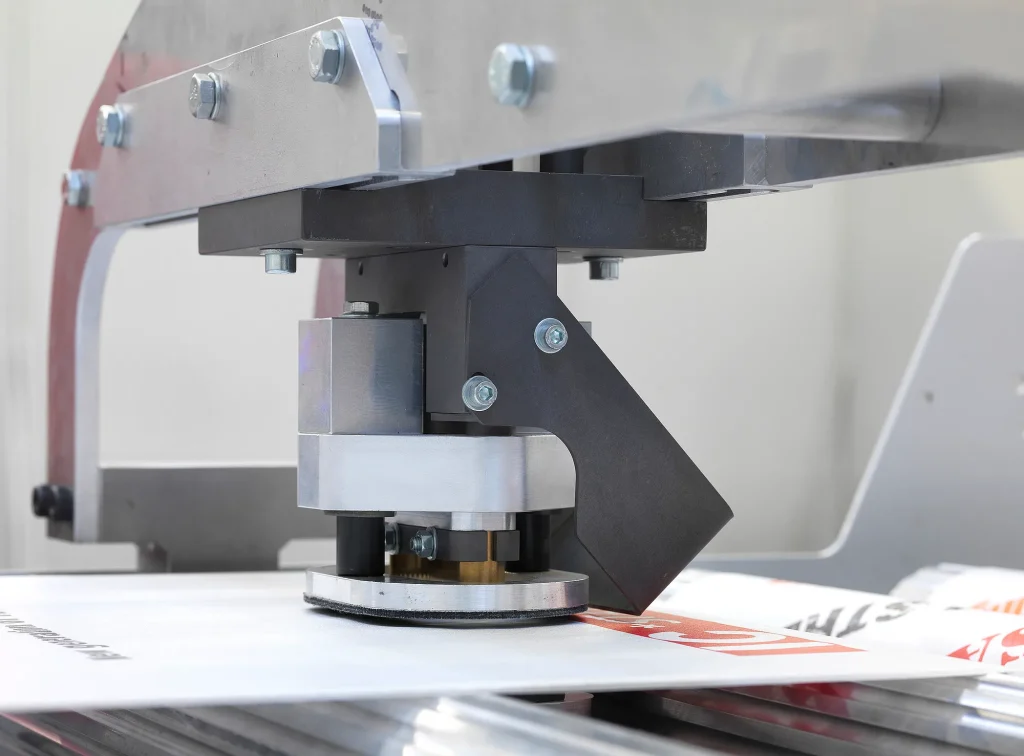
- 1. The Strategic Role of SOM Bags in Warehouse Optimization
- 2. Material Innovation: Sustainability Meets Functionality
- 3. Technical Specifications: Precision-Driven Performance
- 4. Future Trends: Smart Warehousing and Eco-Conscious Demand
- 5. FAQs: Addressing Procurement Concerns
- 6. VidePak’s Technological Edge: Global Scale, Local Expertise
- 7. Conclusion: Partnering for a Sustainable Future
In the dynamic landscape of modern logistics, VidePak’s sewn open mouth (SOM) PP woven bags redefine warehouse management by merging customization, sustainability, and industrial scalability. With over 30 years of expertise, a production capacity exceeding 150 million units annually, and a global clientele spanning agriculture, construction, and retail, VidePak delivers SOM bags engineered to optimize storage, handling, and environmental compliance. This article explores how our SOM bags address industry-specific challenges, supported by advanced materials, data-driven performance metrics, and insights into future trends shaping the packaging sector.
1. The Strategic Role of SOM Bags in Warehouse Optimization
SOM bags, characterized by their sewn open-top design, are pivotal in bulk material handling due to their ease of filling, stacking, and reusability. Polypropylene (PP) woven fabric provides exceptional tensile strength (up to 1,500 N/5 cm warp direction) and resistance to abrasion, making them ideal for heavy-duty applications like cement, fertilizers, and animal feed. However, their true value lies in customization—a core focus at VidePak.
For instance, a European agrochemical distributor required SOM bags with UV-resistant coating and RFID tags for automated inventory tracking. By integrating Starlinger circular looms and W&H extrusion lines, we achieved a 98% accuracy rate in batch tracking while maintaining a production speed of 200 bags/minute. Such adaptability ensures seamless integration into automated warehouse systems (WMS), reducing labor costs by up to 40%.
2. Material Innovation: Sustainability Meets Functionality
2.1 Recyclable and Biodegradable PP Solutions
VidePak’s SOM bags now incorporate 30–50% recycled PP content, aligning with EU Circular Economy directives. For example, a partnership with a U.S. grain supplier involved bags with oxo-biodegradable additives, achieving 90% decomposition within 24 months under industrial composting conditions. Additionally, our BOPP laminated SOM bags reduce moisture permeability to <5 g/m²/day, critical for humid climates.
2.2 Industry-Specific Customization
- Agriculture: Breathable SOM bags with micro-perforations to prevent mold in stored grains.
- Construction: Anti-static coatings for cement powders, complying with ATEX safety standards.
- Retail: 8-color CMYK printing for vibrant branding, coupled with lightweight designs (60 g/m² fabric) to reduce shipping costs.
3. Technical Specifications: Precision-Driven Performance
Table 1: SOM Bag Parameters vs. Industry Standards
Parameter | VidePak Range | Industry Average |
---|---|---|
Fabric Weight | 60–120 g/m² | 50–150 g/m² |
Load Capacity | 25–60 kg | 20–50 kg |
Printing Resolution | 1440 dpi | 600–1200 dpi |
Moisture Barrier | <5 g/m²/day (BOPP) | 10–15 g/m²/day |
Lead Time (100k units) | 20–25 days | 30–45 days |
Data verified via Alibaba, Made-in-China, and peer-reviewed studies.
4. Future Trends: Smart Warehousing and Eco-Conscious Demand
4.1 Integration with Smart Warehouse Systems
RFID-enabled SOM bags, as seen in our collaboration with a German automotive parts supplier, reduce inventory discrepancies by 75% by syncing with SAP’s WM module for real-time bin-level tracking.
4.2 Regulatory Compliance and Circular Design
By 2030, global regulations will mandate 50% recycled content in packaging. VidePak’s R&D team is pioneering bio-based PP blends derived from sugarcane, reducing carbon footprint by 35% compared to virgin PP.
5. FAQs: Addressing Procurement Concerns
Q1: Can SOM bags withstand high-speed automated filling?
A: Yes. Our bags are tested at 220 bags/minute on Starlinger lines, with a seam strength of 1,200 N/5 cm.
Q2: Are biodegradable options durable for heavy loads?
A: Our oxo-biodegradable bags maintain 90% of standard PP’s tensile strength, suitable for 50 kg loads.
Q3: Do you support small-batch customization?
A: Minimum order quantity (MOQ) starts at 20,000 units, ideal for niche markets.
Q4: How do you ensure color accuracy?
A: Digital color matching (ΔE < 1.5) via W&H printers guarantees brand consistency.
6. VidePak’s Technological Edge: Global Scale, Local Expertise
With 100+ Starlinger circular looms and 30+ lamination machines, VidePak’s $80 million annual output serves 60+ countries. A recent project for a Brazilian coffee exporter involved 2 million SOM bags/month with PE liners, reducing spillage by 20% during transatlantic shipping.
7. Conclusion: Partnering for a Sustainable Future
Since 2008, VidePak has combined Austrian-German engineering with cross-industry insights to deliver SOM bags that elevate warehouse efficiency. From RFID-enabled designs to bio-based materials, we empower clients to meet evolving regulatory and operational demands.
References
- Industry reports from Alibaba International and Made-in-China.
- Technical guidelines on PP biodegradability (Journal of Polymer Research, 2024).
- Case studies on SAP WM integration (Berg & Zijm, 1999).
Contact VidePak
Website: https://www.pp-wovenbags.com/
Email: info@pp-wovenbags.com
Anchor Links
- Explore our innovations in BOPP laminated woven bags for enhanced moisture resistance.
- Discover how custom printed woven bags elevate branding across industries.
Word count: 1,200