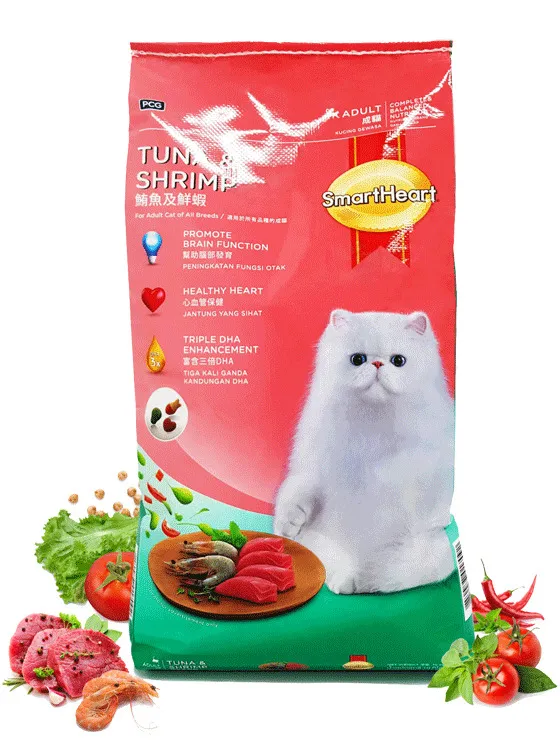
When it comes to efficiently packaging chemical products and raw materials such as fertilizers, plastic pellets, activated carbon, carbon black, and disinfectants, using Form-fill-seal (FFS) Woven bags provides an effective and automated solution. These FFS woven bags are crafted to improve handling, storage, and transportation, while safeguarding the products from contamination and damage.
How Form-fill-seal Woven Bags Enable Automatic Packaging
Form-fill-seal Woven Bags, also known as FFS Woven Sacks, are manufactured using FFS technology, which seamlessly integrates forming, filling, and sealing into one automated packaging process. This type of bag offers a high degree of customization and is ideal for packaging bulk materials due to its structural durability and resistance to tearing.
The FFS Woven Bags are designed for use in specialized machinery, where the bag’s tubular structure is continuously filled and sealed, creating a robust and consistent package ready for immediate handling and transportation. This high-speed packaging system brings multiple advantages for chemical products:
- Efficiency: Automation minimizes human involvement, reducing errors and ensuring consistent packaging quality.
- Safety: Chemical products often pose handling risks; FFS Woven Bags minimize human exposure during packaging.
- Cost Reduction: The process enhances operational speed and reduces labor costs.
- Customization: For specific requirements such as anti-static or UV-resistant materials, these bags can be tailored accordingly.
To read more on VidePak’s commitment to quality and how it manufactures Form-fill-seal Woven Bags, refer to our detailed insights.
Key Considerations for Chemical Packaging Using Form-fill-seal Woven Bags
Packaging chemicals or raw materials requires extra caution due to the properties of the materials being handled. The following attributes of FFS Woven Bags make them suitable for handling chemical products:
- Strength and Durability: Heavy-duty FFS PP Bags are crafted from high-strength woven polypropylene, capable of withstanding abrasion and punctures.
- Barrier Properties: To prevent contamination and moisture ingress, FFS Woven Bags can be manufactured with lamination or added liners for enhanced barrier protection.
- Chemical Resistance: Certain chemicals can react with packaging materials; therefore, polypropylene’s chemical-resistant nature makes it an ideal choice for chemical packaging.
- Customization for Specific Requirements: Depending on the product’s properties, bags can be designed to include features such as UV protection, anti-static treatment, and moisture barriers.
Comparison of FFS Woven Bags with Traditional Packaging Solutions for Chemicals
Packaging Type | Strength | Barrier Protection | Automation Compatibility | Cost-Effectiveness | Ideal Usage |
---|---|---|---|---|---|
FFS Woven Bags | High | High (with options) | Yes | High | Bulk chemicals, granules |
Paper Sacks | Medium | Medium | Limited | Moderate | Low-moisture products |
Plastic Bags | Low | Variable | Limited | Moderate | Light, low-risk products |
FIBCs (Bulk Bags) | Very High | High | Partial | Low | Large, high-volume products |
Choosing the Right FFS Woven Bags for Chemical Products
Each chemical product has specific packaging requirements based on its composition, handling characteristics, and storage conditions. Below are the main factors to consider when selecting an appropriate FFS Woven Bag:
- Barrier Requirements:
- Fertilizers: Fertilizers are hygroscopic and sensitive to moisture, so they require FFS Woven Bags with a laminated surface or additional inner PE liners for moisture protection.
- Activated Carbon and Carbon Black: These are fine particles, which are highly permeable. Tubular Woven Bags with anti-leak liners ensure minimal product loss and containment of dust.
- Handling Requirements:
- Granules and Pellets (e.g., Plastic Pellets): Plastic pellets require bags that resist tearing and puncturing. FFS PP Bags with reinforced layers ensure that pellets remain intact during transport.
- Disinfectants and Chemicals: Packaging for potentially hazardous chemicals often involves anti-static and leakproof features, minimizing the risk of accidental spills or contamination.
- Customization Based on Product Sensitivity:
- UV Protection: For chemicals stored outdoors, UV-resistant bags extend the life of the packaging.
- Anti-static Properties: For powdered materials like carbon black, anti-static bags prevent static buildup that can result in hazardous conditions during filling and transport.
- Bag Design Choices:
- Tubular Woven Bags: Tubular bags are excellent for powdered products, as they reduce leakage and offer consistent filling.
- FFS Roll Bags: These are continuous rolls of bags ideal for high-speed filling lines, allowing for efficient, large-scale production.
Special Considerations for Safety and Compliance
Chemicals, especially those that are reactive or hazardous, require additional packaging measures to comply with industry safety standards. FFS Woven Bags allow companies to adhere to these standards through their structural integrity and customizability.
1. Moisture Barrier:
Many chemicals, such as fertilizers and some powders, react with water. FFS Woven Bags with a laminated layer or PE liner can effectively provide a moisture barrier, ensuring product quality during transport and storage.
2. Electrostatic Control:
Static buildup during packaging and handling can be dangerous with certain chemicals. Anti-static Tubular Woven Bags prevent this by using specialized materials or coatings that dissipate static electricity.
3. Environmental Protection:
To prevent leaching or contamination, the materials used in FFS Woven Bags must be chemically inert. Polypropylene, the primary material used, provides excellent chemical resistance, ensuring no interaction between the bag and its contents.
The Benefits of Automated Packaging with FFS Woven Bags for Chemical Products
Automated packaging using FFS Woven Bags offers a solution that minimizes exposure to hazardous materials and improves efficiency in handling and storage. For chemical companies, this results in:
- Improved Product Safety: Properly sealed FFS bags reduce the risk of spills or leaks, maintaining the integrity of both the product and the surrounding environment.
- Streamlined Operations: High-speed FFS machines cut down on manual labor, freeing up employees for other essential tasks and reducing human exposure to potentially hazardous substances.
- Enhanced Quality Control: Automated filling and sealing result in consistent, reliable packaging that minimizes variances and meets stringent quality standards.
Why Choose VidePak’s Form-fill-seal Woven Bags for Chemical Packaging?
With years of experience and advanced equipment, VidePak specializes in the production of FFS Woven Bags that meet the unique demands of chemical packaging. Our FFS bags provide top-tier durability, excellent moisture resistance, and are customizable to fit specific product requirements. By choosing VidePak, companies in the chemical sector benefit from quality, efficiency, and safety—ensuring their products remain safe, uncontaminated, and ready for market distribution.
For chemical companies handling sensitive products, the transition to automated packaging solutions like FFS Woven Bags isn’t just an upgrade in efficiency—it’s an investment in quality, safety, and consistency. The choice of the right FFS Woven Bag is essential for optimizing packaging and storage in the chemical industry.