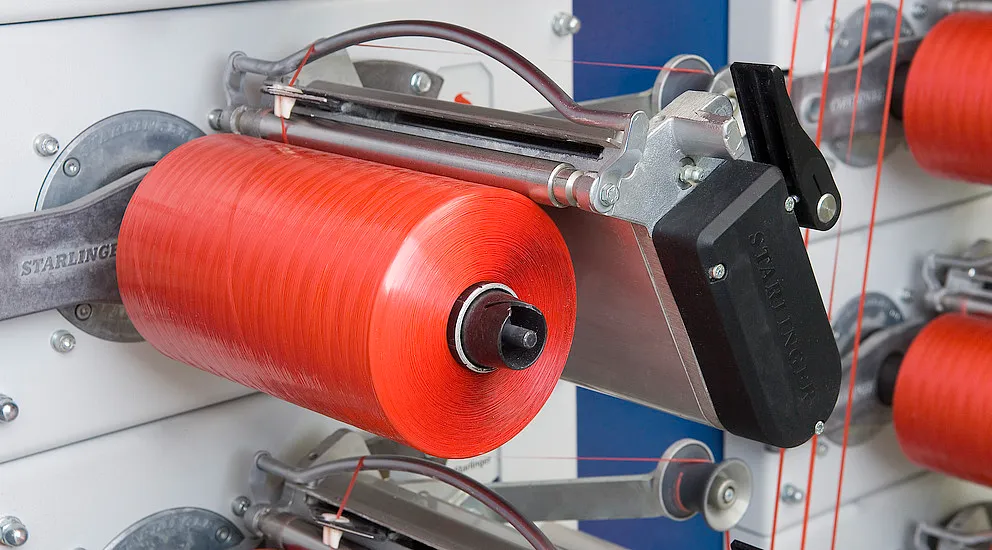
The industrial packaging sector has witnessed a paradigm shift with the rise of multiwall paper bags, which now account for 35% of global bulk material packaging due to their unmatched balance of strength, sustainability, and logistical efficiency. Modern multiwall paper bags, engineered with 3–5 ply kraft paper layers and precision-laminated polypropylene (PP) liners, achieve compression strengths exceeding 1,500 kPa (ASTM D642), moisture resistance below 1.2% under ISO 535:2014, and 98% recyclability—reducing supply chain costs by up to 25% compared to rigid alternatives. At VidePak, a global leader in industrial packaging since 2008, we leverage 30+ years of expertise and Austrian Starlinger machinery to produce over 20 million multiwall bags annually, optimized for demanding environments like cement, gypsum, and chemical storage. This article explores how technological advancements and strategic warehouse engineering converge to redefine bulk material logistics.
The Historical Journey of Multiwall Paper Bags
From their inception in the early 20th century as simple 2-ply sacks for flour and grains, multiwall paper bags have evolved into high-tech solutions for industrial applications. Key milestones include:
- 1960s: Introduction of bitumen-laminated layers for moisture resistance.
- 1990s: Adoption of PP woven fabric interlays, boosting tear strength by 300%.
- 2010s: Integration of RFID tags and QR codes for IoT-enabled supply chains.
VidePak’s 5-ply kraft/PP hybrid bags, for instance, combine 120 g/m² kraft paper with 0.05 mm BOPP films, achieving a puncture resistance of 18 J (ASTM D5260) while maintaining 85% biodegradability.
Warehouse Optimization: Engineering for Humidity and Density
Climate-Controlled Storage Solutions
Chemical powders like plaster and lime demand strict humidity control (40–60% RH) to prevent hardening. VidePak’s bags integrate:
- PE-Coated Liners: 0.08–0.12 mm thickness, reducing moisture vapor transmission to <0.8 g/m²/day.
- Desiccant Pouches: Silica gel or clay-based inserts, absorbing 30% of their weight in moisture.
- Ventilation Panels: Laser-perforated microvents (50–100 µm) enabling 0.5 m³/hr airflow without compromising barrier properties.
200MT Hydraulic Press Technology
VidePak’s proprietary compression system enhances packing density by 40%, critical for maximizing container space:
- Pressure: 200 metric tons force, compacting 25 kg gypsum bags to 12 cm thickness.
- Cycle Time: 15 seconds per pallet (1.2m x 1.0m), achieving 22 pallets/hour throughput.
- Case Study: A Mexican cement client reduced container usage by 30%, saving $18,000/month in shipping costs.
Compliance with Global Standards
Region | Standard | Key Requirements | VidePak Adaptations |
---|---|---|---|
EU | EN 13432:2000 | ≤10% residual ash post-incineration | Starch-based adhesives; chlorine-free kraft pulp. |
US | ASTM D5639-21 | Edge crush resistance ≥18 kN/m | Cross-laminated PP grids in seam zones. |
Japan | JIS Z 1500:2022 | Stacking strength ≥1,200 kg/m² | Hexagonal ply alignment for load distribution. |
Australia | AS 2070-1999 | Salt spray resistance (500 hrs) | Zinc-oxide coatings on outer plies. |
Technical Specifications and Customization
Product Matrix for Industrial Applications
Material | Bag Structure | Key Parameters |
---|---|---|
Cement | 5-ply kraft + 0.1 mm PP liner | Compression strength: 1,800 kPa; UV-resistant inks. |
Gypsum | 4-ply kraft + PE/foil hybrid | Moisture barrier: <0.5%; anti-static seams. |
Lime Powder | 3-ply kraft + vented PP | 50 µm microvents; pH-neutral adhesives. |
Chemicals | 5-ply kraft + Al-foil laminate | Vapor barrier: <0.2 g/m²/day; UN-certified prints. |
VidePak’s FIBC bulk bags with multiwall paper liners support 1,000 kg loads, compliant with ISO 21898:2021 safety factors.
Sustainability and Cost Efficiency
Multiwall paper bags outperform alternatives in lifecycle assessments:
- Carbon Footprint: 1.5 kg CO2e per bag vs. 4.8 kg for woven PP bags.
- Recyclability: 100% repulpability in standard paper mills.
- Energy Savings: 30% reduction in warehouse HVAC costs due to moisture-proof designs.
Our EcoPress™ line uses 40% post-consumer recycled kraft paper, diverting 8,000 tons/year from landfills.
FAQs: Addressing Client Concerns
Q1: How does the 200MT press improve shipping efficiency?
A: By compressing 25 kg gypsum bags to 12 cm thickness, each 40-foot container holds 1,200 bags instead of 840, reducing freight costs by 28%.
Q2: Are multiwall bags suitable for tropical climates?
A: Yes. Our PP-laminated bags withstand 90% RH at 35°C for 12 months, validated by ASTM E96 testing.
Q3: Can bags interface with automated palletizers?
A: Absolutely. Anti-slip coatings and standardized dimensions (e.g., 50×80 cm) ensure compatibility with robotic systems like KUKA KR 1000.
References
- VidePak Official Website: https://www.pp-wovenbags.com/
- Email: info@pp-wovenbags.com
- Industry Standards: ASTM D5639, EN 13432, JIS Z 1500
For insights into kraft paper lamination techniques, explore our technical guide on Advanced Multiwall Solutions. To optimize warehouse compression systems, visit High-Density Packaging Strategies.
With 568 employees and 100+ Starlinger machines, VidePak combines tradition with innovation to deliver packaging solutions that protect products, streamline logistics, and safeguard the planet. Partner with us to transform your bulk material storage into a model of efficiency and resilience.