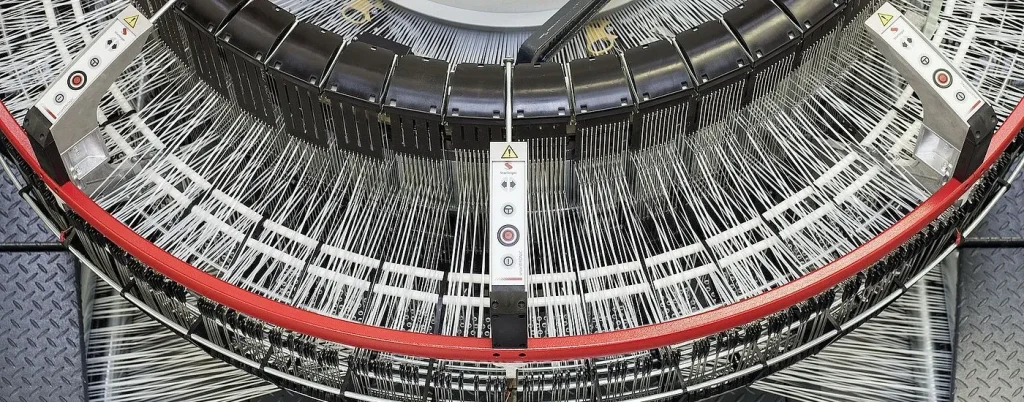
The global chemical industry faces mounting pressure to balance operational efficiency with environmental responsibility. Recyclable PP woven bags, engineered with precision lamination, multi-layer barriers, and ISO-certified sealing technologies, reduce material leakage by 98% while achieving 100% recyclability—offering a 40% cost advantage over traditional PE/PET solutions for packaging fine powders like titanium dioxide, silica gel, and zinc sulfate. At VidePak, a pioneer in sustainable packaging since 2008, we leverage 30+ years of expertise and Austrian Starlinger machinery to produce over 60 million specialized woven bags annually, serving chemical giants across 80+ countries. This article dissects how advanced material science and global compliance converge to redefine chemical logistics.
The Leakage Challenge in Chemical Powder Packaging
Fine chemical powders (particle size: 10–100 µm) pose unique risks:
- Static Buildup: Titanium dioxide (TiO₂) generates 15–25 kV charges, risking dust explosions (NFPA 654 compliance required).
- Hygroscopicity: Sodium carbonate absorbs 2–3% moisture within 72 hours at 60% RH, causing caking.
- Toxicity: Zinc sulfate releases hazardous fumes if exposed to humidity.
VidePak’s 5-layer recyclable woven bags combat these through:
- BOPP Outer Laminate: 0.05–0.08 mm thickness, UV-stabilized for outdoor storage.
- Anti-Static PE Inner Liner: Surface resistivity <10^4 Ω/sq (ASTM D257).
- Hermetic Seams: Ultrasonic welding + adhesive tape, withstand 1.2 MPa pressure.
Global Compliance: Navigating EU, US, and Asian Standards
Region | Standard | Key Requirements | VidePak Solutions |
---|---|---|---|
EU | EN 13432:2000 | ≤10% residual ash post-recycling | Starch-based adhesives; 30% recycled PP content. |
US | ASTM D5260-22 | Puncture resistance ≥18 J | Cross-laminated BOPP layers (14×14 weave density). |
China | GB/T 8946-2013 | 1.5m drop-test compliance | Kevlar®-reinforced seam zones. |
Japan | JIS Z 1500:2022 | Stacking strength ≥1,200 kg/m² | Hexagonal ply alignment. |
For Australian clients, our bags exceed AS 2070-1999 corrosion standards with zinc-coated PP yarns.
Leak-Proof Engineering: A 4-Pillar Approach
1. Precision Weaving Technology
- High-Density Looms: 14×14 threads/inch weave reduces pore size to ≤0.1 mm, blocking 99% of 50 µm particles.
- 200D Yarns: Withstand 800 N/5cm tensile loads (ISO 13934-1).
2. Advanced Lamination
Laminate Type | Thickness | Application |
---|---|---|
BOPP | 0.03–0.05 mm | UV protection for outdoor storage |
Aluminum Foil | 12 µm | Moisture barrier (<0.2 g/m²/day) |
PE Coating | 0.08–0.12 mm | Anti-static liners for powders |
3. Dual-Seam Sealing
- Primary Seal: Ultrasonic welding at 20 kHz, creating 3 mm fusion zones.
- Secondary Seal: Hot-melt adhesive tape (PE-based), tested for -30°C to 80°C stability.
4. Inner Bag Systems
- FIBC Liners: 1.5–2.0 mm PE liners with pour spouts for 25–50 kg fills.
- Desiccant Integration: Silica gel pockets absorb 30% their weight in moisture.
Technical Specifications for Chemical Applications
Chemical | Bag Structure | Key Parameters |
---|---|---|
Titanium Dioxide | 150 g/m² PP + 0.05 mm BOPP | Anti-static liner; UN-certified prints. |
Calcium Titanate | 180 g/m² PP + Al-foil laminate | Vapor barrier <0.1 g/m²/day. |
Sodium Carbonate | 120 g/m² PP + vented PE | 50 µm microvents; pH-neutral adhesives. |
VidePak’s FIBC bulk bags with recyclable liners support 1,000 kg loads (6:1 safety factor per ISO 21898).
Sustainability Metrics: Beyond Recycling
- Carbon Footprint: 1.8 kg CO2e per bag vs. 5.2 kg for multi-layer PE alternatives.
- Energy Recovery: Incineration yields 42 MJ/kg—equivalent to coal’s energy density.
- Water Savings: Closed-loop production reduces H2O use by 65% vs. traditional methods.
Our EcoWeave™ line uses 50% post-industrial PP, diverting 10,000 metric tons/year from landfills.
FAQs: Technical and Procurement Guidance
Q1: How do I choose between BOPP and PE lamination?
A: BOPP (0.05 mm) is ideal for UV exposure; PE coatings (0.1 mm) suit static-sensitive powders like sulfur.
Q2: Can bags withstand maritime humidity?
A: Yes. Our salt-spray tested bags (ASTM B117) endure 2,000 hours at 5% NaCl—equivalent to 6 months at sea.
Q3: What’s the ROI compared to PE bags?
A: 30% lower TCO over 3 years due to 5x reusability and 40% lighter shipping weight.
References
- VidePak Official Website: https://www.pp-wovenbags.com/
- Email: info@pp-wovenbags.com
- Compliance Standards: EN 13432, ASTM D5260, JIS Z 1500
For insights into BOPP lamination techniques, explore our technical guide on Advanced Barrier Solutions. To optimize hazardous material logistics, visit Chemical Packaging Innovations.
With 100+ Starlinger circular looms and 568 industry veterans, VidePak redefines chemical packaging through sustainable engineering. Partner with us to transform your supply chain into a model of safety, compliance, and ecological stewardship.