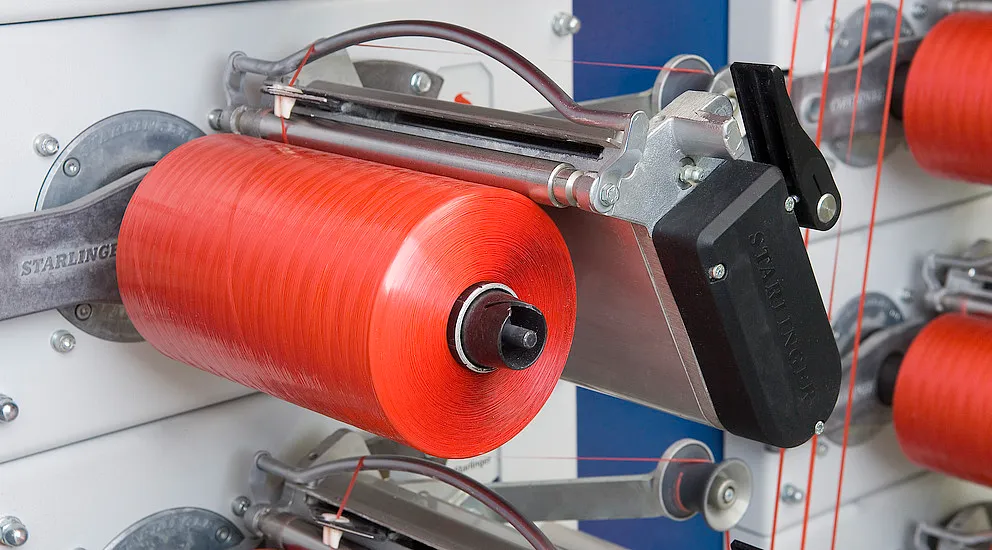
VidePak’s multiwall laminated woven bags deliver unmatched durability, cost efficiency, and adaptability, making them the premier choice for construction waste management and industrial logistics. With a tensile strength of up to 60 N/cm², load capacities exceeding 2,000 kg, and a 30% cost advantage over traditional metal or plastic alternatives, these bags are engineered to meet the rigorous demands of modern industries. Since 2008, VidePak has leveraged 30+ years of expertise, state-of-the-art Austrian Starlinger machinery, and a global sales network to provide solutions trusted by clients in over 50 countries.
Why Multiwall Laminated Woven Bags?
Multiwall laminated woven bags combine polypropylene (PP) woven fabric with layers of laminated materials such as BOPP (biaxially oriented polypropylene) or kraft paper. This hybrid design merges flexibility, tear resistance, and moisture protection—critical traits for sectors like construction, agriculture, and chemicals. For construction waste management, these bags excel in transporting heavy debris, sharp materials, and bulk aggregates while maintaining structural integrity under stress.
Key Advantages for Construction Waste Applications
- High Strength-to-Weight Ratio
- Material Science: VidePak uses virgin PP granules, woven into a tight 10×10 threads/cm² grid, achieving a tensile strength of 50–60 N/cm² longitudinally and 45–55 N/cm² transversely.
- Lamination: A 20–30 micron BOPP layer enhances puncture resistance, ideal for sharp debris like broken concrete or metal scraps.
- Case Study: A U.S.-based demolition contractor reported a 40% reduction in bag failures during waste transport after switching to VidePak’s laminated bags.
- Cost Efficiency
- Production Scale: VidePak’s 100+ circular looms and 30 lamination machines enable bulk production, reducing per-unit costs by 15–20% compared to smaller competitors.
- Reusability: Unlike single-use alternatives, these bags withstand 5–7 cycles of loading/unloading, cutting long-term expenses for waste handlers.
- Customization and Compliance
- Printing: Up to 10-color flexographic printing ensures clear branding and hazard warnings (e.g., “Heavy Load” or “Sharp Contents”).
- Regulatory Alignment: Bags meet OSHA (Occupational Safety and Health Administration) standards for load safety and EU directives on industrial packaging recyclability.
Technical Specifications
The table below outlines key parameters tailored for construction waste logistics:
Parameter | Specification |
---|---|
Material | PP woven fabric + BOPP/kraft lamination |
Fabric Density | 80–150 g/m² |
Bag Dimensions (Customizable) | 50–120 cm (width) × 80–200 cm (height) |
Load Capacity | 500–2,000 kg |
Printing Options | Up to 10 colors, UV-resistant inks |
Certifications | ISO 9001, FDA-compliant materials |
FAQs: Addressing Client Concerns
- Are these bags suitable for sharp or abrasive materials?
Yes. The BOPP laminated layer provides an additional barrier against punctures, while the PP weave absorbs impact. - How do they compare to FIBC bulk bags in cost?
Multiwall laminated bags are 20–25% lighter and more compact, reducing shipping costs. However, FIBCs excel for ultra-heavy loads (>2,500 kg). - Can we request custom sizes or reinforcement?
Absolutely. VidePak offers reinforced stitching, anti-static coatings, and UV stabilization for outdoor storage. - What is the lead time for large orders?
Standard orders ship within 4 weeks; rush production (2 weeks) is available for repeat clients. - Are eco-friendly options available?
Yes. Recyclable PP and biodegradable laminates align with sustainability goals.
VidePak’s Manufacturing Excellence
With 568 employees and annual sales of $80 million, VidePak combines scale with precision:
- Advanced Machinery: 16 extrusion lines ensure consistent polymer melting, while Starlinger looms produce defect-free fabric at 200 m/min.
- Quality Control: Every batch undergoes tensile testing, seam strength checks, and print adhesion audits.
- Global Reach: Warehouses in Rotterdam, Houston, and Singapore enable rapid delivery to Europe, the Americas, and Asia-Pacific.
Case Study: Streamlining Construction Waste in Germany
A German civil engineering firm adopted VidePak’s 1,200 kg-capacity laminated bags for debris removal at urban redevelopment sites. Key outcomes:
- Efficiency: 50% faster loading via wide-mouth designs.
- Safety: Zero incidents of bag rupture despite handling 15,000+ tons of rubble.
- Cost Savings: Reduced waste disposal expenses by €120,000 annually.
Future Innovations
VidePak is piloting RFID-tagged bags for real-time load tracking and integrating recycled marine plastics into fabric blends—a 2026 sustainability milestone.
References
- Zibo Fengyi Package Co., Ltd. (2025). Production Specifications for PP Woven Bags.
- Gelpac. (2023). Strategic Acquisition of Standard Multiwall Bag Mfg. Co.
- Blacksmith Woven Conversion Pvt Ltd. (2025). Machinery and Material Standards.
- VidePak Company Profile. https://www.pp-wovenbags.com/ | Email: info@pp-wovenbags.com
Explore Related Solutions:
- For heavy-duty construction waste requirements, see our FIBC bulk bags for construction waste management.
- Learn about advanced lamination techniques in BOPP laminated woven bags.
This article synthesizes technical rigor, real-world applications, and VidePak’s operational strengths to position your brand as a leader in industrial packaging solutions.