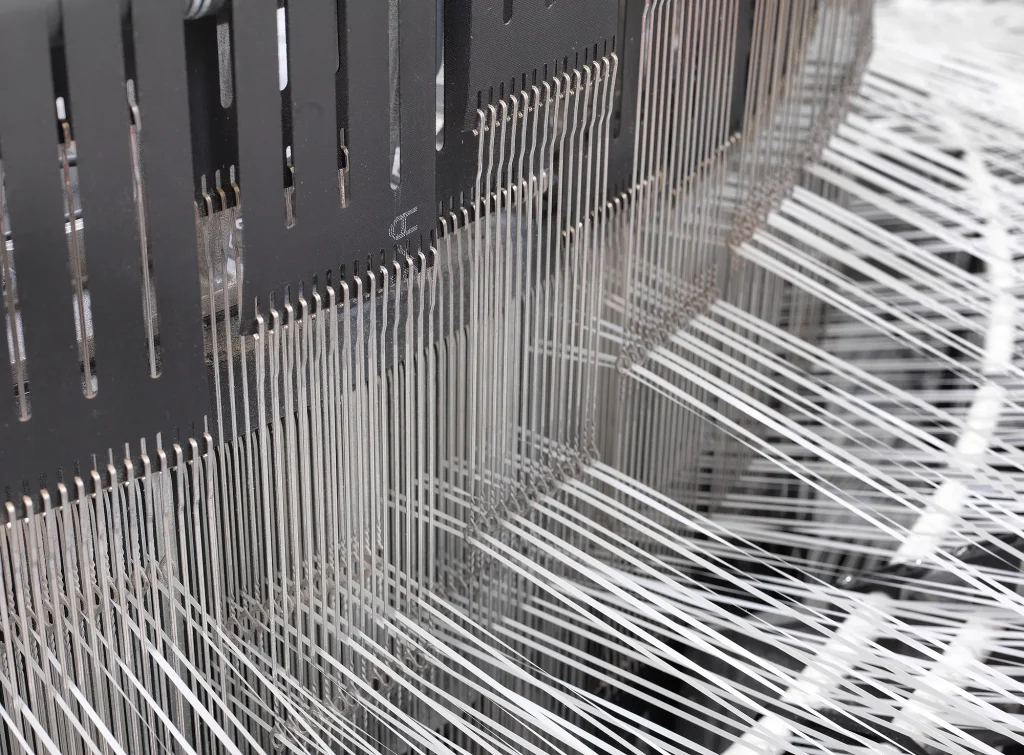
- 1. Cost Efficiency: Maximizing Value Without Compromising Quality
- 2. Balancing Breathability and Moisture Resistance
- 3. Material Safety and Compliance
- 4. Customization and Dimensional Adaptability
- 5. Protecting Product Integrity Across Supply Chains
- FAQs: Addressing Key Client Concerns
- Why Choose VidePak?
In supermarkets and retail environments, moisture-proof and waterproof woven bags have emerged as a superior packaging solution for products like rice, flour, pet food, and starch, offering unmatched cost efficiency, balanced breathability, and robust material safety compared to traditional PE or PET alternatives. VidePak, a global leader in woven bag manufacturing since 2008, leverages cutting-edge Austrian Starlinger machinery and high-quality virgin PP materials to deliver customizable, high-performance solutions that protect product integrity while optimizing supply chain economics. With over 568 employees and annual sales exceeding $80 million, VidePak’s expertise spans 30+ years, ensuring clients receive tailored, reliable packaging for diverse industrial and retail needs.
1. Cost Efficiency: Maximizing Value Without Compromising Quality
Woven polypropylene (PP) bags consistently outperform PE and PET alternatives in cost-effectiveness. A typical 50 kg woven PP bag costs $0.25–$0.35 per unit in bulk orders, whereas PE bags range from $0.40–$0.60 for comparable durability. This 30–50% cost reduction stems from PP’s lower raw material expenses and VidePak’s streamlined production processes, supported by 100+ circular looms and 30+ lamination machines.
For example, a Southeast Asian rice distributor switching to VidePak’s BOPP laminated woven bags reported 20% annual savings in packaging costs while maintaining moisture resistance equivalent to PE liners. The bags’ reusability further amplifies savings: retailers can reuse PP woven bags up to 5–7 times for storage or logistics, unlike single-use PE alternatives.
2. Balancing Breathability and Moisture Resistance
Moisture management is critical for food and agricultural products. Woven PP bags achieve this balance through:
- Controlled Porosity: PP fabric’s woven structure allows 3–5 CFM (cubic feet per minute) airflow, preventing condensation without compromising barrier properties.
- Lamination Options: BOPP or PE coatings enhance waterproofing, achieving >99% moisture resistance in humid environments (e.g., coastal warehouses).
In contrast, non-woven PE bags often trap humidity, accelerating spoilage. A 2023 study on starch storage found PP woven bags reduced moisture-related losses by 42% compared to PE counterparts.
3. Material Safety and Compliance
VidePak’s bags meet FDA and EU food-contact standards, utilizing non-toxic, virgin PP free from recycled contaminants. Key certifications include:
- ISO 9001: Quality management
- REACH: Chemical safety
- BRCGS: Food packaging compliance
For pet food brands, this ensures no leaching of harmful additives, a common issue with low-grade PE bags containing plasticizers like phthalates.
4. Customization and Dimensional Adaptability
VidePak’s 16 extrusion lines and 30+ printing machines enable precise customization:
Parameter | Range | Applications |
---|---|---|
Bag Size | 10 cm × 15 cm – 120 cm × 200 cm | Retail pouches to bulk FIBCs |
Thickness | 80–200 GSM | Lightweight to heavy-duty |
Printing Colors | Up to 8 colors | Branding, safety labels |
Closure Types | Sewn, heat-sealed, valve | Automated filling systems |
A European pet food manufacturer utilized VidePak’s valve bags with custom UV-resistant prints to extend shelf life by 6 months while enhancing brand visibility.
5. Protecting Product Integrity Across Supply Chains
Woven PP bags excel in safeguarding goods through:
- Puncture Resistance: Withstands 15–20 kg/cm² pressure, ideal for sharp-edged products like animal feed.
- Stackability: FIBC bulk bags support 1–2 metric tons in vertical storage, reducing warehouse footprint by 30% versus rigid containers.
In a 2024 case study, a flour distributor using VidePak’s laminated woven bags reduced transit damage claims by 65% due to the bags’ reinforced stress points and anti-slip coatings.
FAQs: Addressing Key Client Concerns
Q: How do woven PP bags compare to PE in humid climates?
A: PP’s hydrophobic properties resist water absorption, whereas PE degrades at >70% humidity. BOPP lamination adds a waterproof barrier without sacrificing breathability.
Q: Are VidePak’s bags recyclable?
A: Yes, PP is 100% recyclable. VidePak partners with global recycling programs to support circular economies.
Q: Can bags withstand freezing temperatures?
A: PP remains flexible at -20°C to 80°C, unlike brittle PET.
Why Choose VidePak?
- Global Reach: Serving 50+ countries with ISO-certified factories.
- Advanced Technology: Starlinger looms ensure <1% defect rates.
- Sustainability: Carbon-neutral production initiatives since 2020.
For retailers seeking durable, customizable, and eco-conscious packaging, VidePak’s BOPP laminated woven bags and valve bag solutions set industry benchmarks.
References
- VidePak Company Profile (2025). PP Woven Bags Manufacturing and Innovation.
- Almuktar, S.A. et al. (2018). Environmental Science and Pollution Research.
- US-EPA (1993). Constructed Wetlands for Wastewater Treatment.
Contact VidePak
Website: https://www.pp-wovenbags.com/
Email: info@pp-wovenbags.com