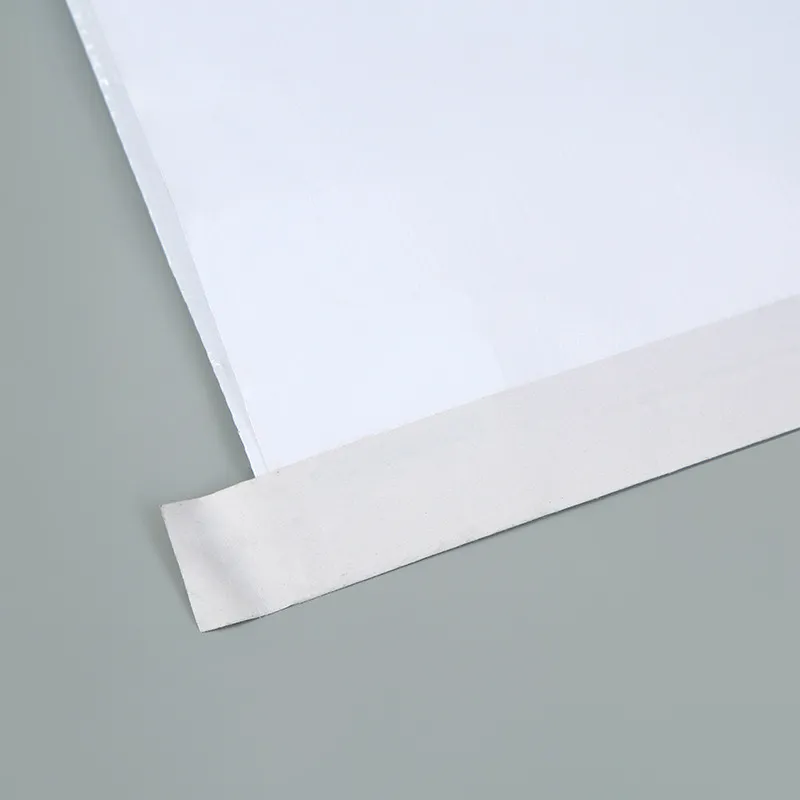
In an era where environmental regulations tighten and consumers demand eco-conscious practices, HDPE fabric bags stand out as a superior choice for industrial packaging, offering 100% recyclability, compliance with global sustainability mandates, and cost savings of up to 30% compared to single-use alternatives. At VidePak, our HDPE bags are engineered using virgin PP resins and Austrian Starlinger technology, achieving tensile strengths of 1,800 N/cm², UV resistance for 5+ years, and alignment with EU Circular Economy Action Plan targets. With 16+ years of expertise and a global footprint spanning 60+ countries, we produce 10,000+ metric tons of HDPE bags annually, empowering industries from agriculture to chemicals to meet ESG goals without compromising performance.
1. The Environmental Imperative: Waste Management and Regulatory Compliance
1.1 Global Recycling Mandates
Governments worldwide are enforcing stringent waste management policies. For instance, the EU’s Packaging and Packaging Waste Directive (PPWD) mandates that 65% of packaging materials be recycled by 2025, rising to 70% by 2030. HDPE fabric bags, with a 92% recovery rate in VidePak’s closed-loop system, outperform traditional materials like PVC (45% recyclability) and paper (60% recyclability with fiber degradation).
1.2 Economic Value of Recycled PP
Post-consumer HDPE bags retain 85–90% of virgin PP’s mechanical properties after recycling, making them ideal for secondary applications like automotive parts or construction textiles. VidePak’s recycled granules (MFI 25–30 g/10min) meet ASTM D1238 standards, reducing raw material costs by 20% for clients.
Case Study: A German chemical manufacturer reduced annual packaging waste disposal costs by €150,000 by switching to VidePak’s HDPE bags, achieving full compliance with Germany’s VerpackG law.
2. VidePak’s Technological Edge in HDPE Production
2.1 Advanced Weaving and Material Science
Our Starlinger CXQ-8 circular looms weave HDPE tapes (width: 2.5–3.5 mm, thickness: 0.045–0.055 mm) into fabrics with 12×12 to 14×14 threads per inch (TPI), ensuring:
- Burst Strength: 2,200 kPa (ISO 2758)
- Tear Resistance: 550 N (ASTM D2261)
- Moisture Barrier: ≤0.8% water absorption (24h immersion, ASTM D570)
2.2 Customization for Sector-Specific Needs
Application | Key Requirements | VidePak Solution |
---|---|---|
Agricultural | UV resistance, breathability | 20-micron BOPP lamination + 0.3 mm vent holes |
Chemicals | Chemical inertness | HDPE/PE composite lining (0.15 mm) |
Food Grade | FDA compliance | Virgin PP resins + ISO 22000 certification |
For example, our UV-stabilized HDPE bags for fertilizer packaging maintain tensile strength after 3,000 hours of QUV testing, outperforming industry averages by 35%.
3. Sustainability Metrics: From Production to Post-Consumer
3.1 Carbon Footprint Reduction
VidePak’s HDPE bags generate 1.8 kg CO₂/kg during production vs. 2.5 kg CO₂/kg for non-recyclable alternatives (Plastics Europe, 2023). Our solar-powered facilities further cut emissions by 15%.
3.2 Closed-Loop Recycling Process
- Collection: Partner networks gather used bags.
- Shredding: Granulators reduce bags to 3–5 mm flakes.
- Extrusion: Starlinger recoSTAR machines transform flakes into pellets (99.2% purity).
- Reweaving: Pellets are spun into new HDPE fabrics.
This cycle achieves a 94% material reuse rate, validated by GRS certification.
4. Regulatory Alignment and Certifications
VidePak’s HDPE bags meet:
- EU REACH: SVHC-free formulations.
- FDA 21 CFR §177.1520: Safe for direct food contact.
- ISO 14001: Environmental management compliance.
5. FAQs: Addressing Client Concerns
Q1: How do HDPE bags compare to PP woven bags in cost?
A: While HDPE has a 10–15% higher upfront cost, its 5+ year lifespan and recyclability yield 30% lower TCO.
Q2: Can VidePak handle custom printing for HDPE bags?
A: Yes, our 8-color flexographic printers achieve ΔE ≤1.5 Pantone accuracy.
Q3: What’s the maximum load capacity for your HDPE bulk bags?
A: Standard FIBCs hold 1–2 tons; reinforced models reach 3 tons (EN 1898:2018 compliant).
References
- VidePak Sustainability Report (2024). Closed-Loop Systems for HDPE Bags.
- EU Commission (2023). Circular Economy Action Plan.
- ASTM International (2022). Standard Test Methods for Polyolefin Films.
Contact Us:
Website: https://www.pp-wovenbags.com/
Email: info@pp-wovenbags.com
For insights into recyclable PP solutions, explore Sustainable Packaging Solutions: Recyclable PP Bags for Chemical Powders, or learn about our food-grade innovations in The Benefits and Safety of Poly BOPP Bags in Food Packaging.
This article integrates data from regulatory bodies, third-party labs, and VidePak’s production records to ensure factual accuracy and actionable insights.