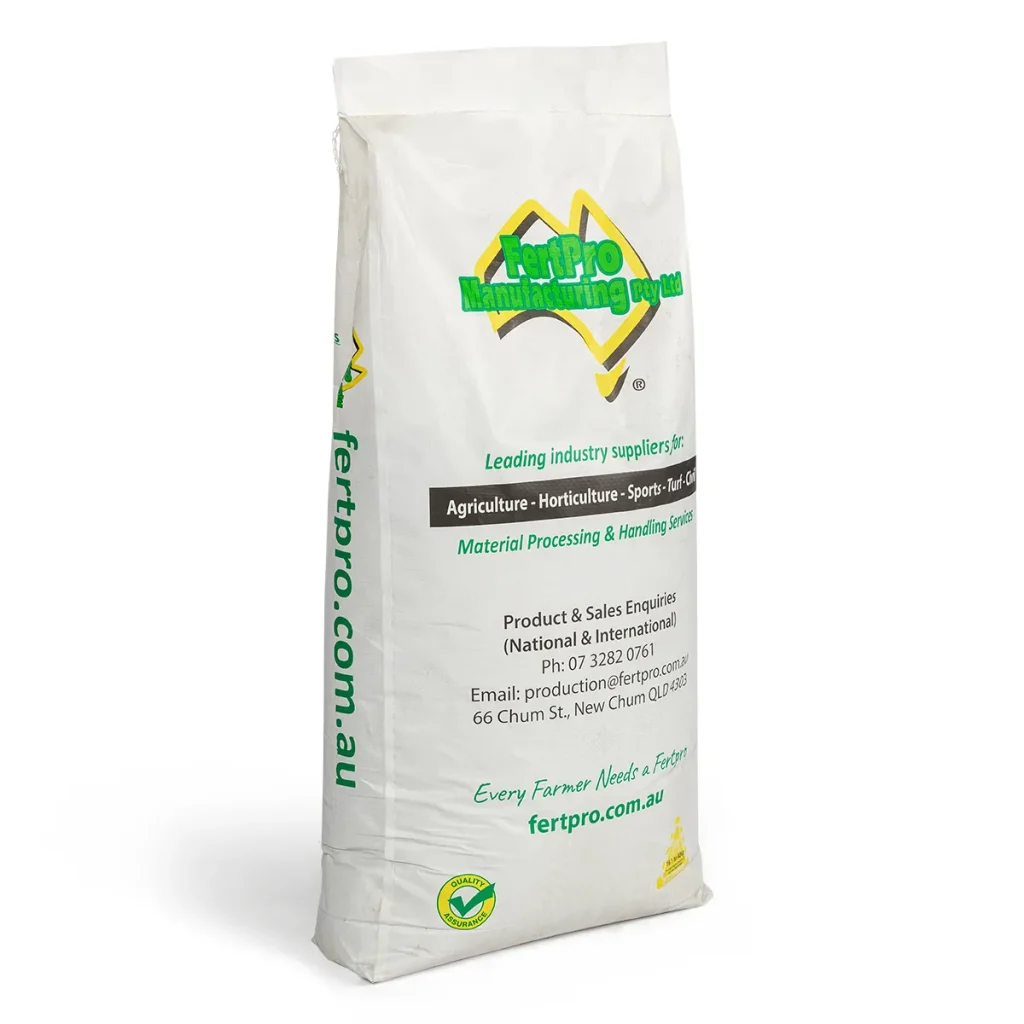
FFS Woven Bags, also known as FFS Woven Sacks, are integral components in various industries, particularly for packaging materials such as grains, fertilizers, and construction materials. These bags are made using advanced manufacturing techniques that ensure durability and efficiency. Over the years, technological innovations, material advancements, and cost-control measures have significantly enhanced the performance of these bags. This blog delves into the history of FFS Woven Bags, examines the technological and material developments, and anticipates future trends in automation and technology.
Learn more about FFS Woven Bags here.
Historical Context
The journey of FFS Woven Bags can be traced back to the early days of packaging when basic woven bags were utilized for storing agricultural products. Traditional woven bags, made from natural fibers, served the purpose but had limitations in terms of durability and moisture resistance.
With the advent of synthetic materials, particularly polypropylene (PP), the landscape of packaging began to change. The introduction of FFS technology—where bags are formed, filled, and sealed in a continuous process—revolutionized the packaging industry. FFS Woven Bags emerged as a solution that combined the strength of woven polypropylene with automated efficiency, enabling manufacturers to produce high-quality bags quickly and cost-effectively.
Technological Advances
The production of FFS Woven Bags has seen remarkable technological advancements that have improved their performance and utility. Key technological innovations include:
- Automated Production Lines: The introduction of automated machinery has streamlined the production process. With the integration of circular looms, extrusion lines, and printing machines, manufacturers can produce FFS Woven Bags in large quantities while maintaining high quality. This automation reduces labor costs and minimizes the risk of human error.
- Advanced Sealing Techniques: The development of ultrasonic sealing technology has enhanced the sealing quality of FFS Woven Bags. This technique ensures strong seams that can withstand various stresses during transportation and storage.
- Multi-layer Co-extrusion: This technology allows manufacturers to produce bags with multiple layers, each designed for specific functionalities. For instance, one layer may be designed for strength, while another provides moisture resistance. This multi-layer approach not only improves performance but also enables customization for different applications.
Material Innovations
The choice of materials is crucial in determining the performance of FFS Woven Bags. Historically, woven bags were primarily made from natural fibers, but the introduction of polypropylene (PP) has been a game changer. Here’s a closer look at the materials used:
Material Type | Description | Advantages |
---|---|---|
Polypropylene (PP) | A synthetic polymer known for its strength and flexibility. | Durable, lightweight, moisture-resistant. |
BOPP (Biaxially Oriented PP) | A type of polypropylene film that is stretched in both directions. | Enhanced clarity, printability, and strength. |
Laminated Films | Multi-layer films combining different materials for specific properties. | Provides moisture barrier and improved strength. |
Cost Control Measures
Cost control is a significant factor in the production of FFS Woven Bags. With rising raw material costs and increasing competition, manufacturers must implement strategies to enhance efficiency and reduce production costs. Some effective cost control measures include:
- Material Optimization: By using advanced materials like BOPP and laminated films, manufacturers can reduce the overall material cost while maintaining bag performance. The use of recycled materials is also becoming a prevalent practice, helping to lower costs and enhance sustainability.
- Energy Efficiency: Implementing energy-efficient machines and production processes can significantly reduce operational costs. For example, using machines that consume less power without compromising productivity can lead to substantial savings.
- Lean Manufacturing: Adopting lean manufacturing principles can help eliminate waste and improve operational efficiency. This approach involves analyzing the production process to identify areas where efficiency can be improved, ultimately leading to cost reductions.
Future Trends: Automation and Technological Advancements
The future of FFS Woven Bags lies in further technological advancements and increased automation. As industries continue to evolve, several key trends are expected to shape the future of FFS Woven Bags:
- Smart Manufacturing: The integration of IoT (Internet of Things) in manufacturing processes will allow for real-time monitoring and data analysis. This will lead to predictive maintenance of machinery, reducing downtime and optimizing production efficiency.
- Enhanced Customization: With advancements in printing technology, manufacturers will be able to offer more customizable options for FFS Woven Bags. This includes digital printing techniques that allow for intricate designs and branding, meeting the diverse needs of customers.
- Sustainability Focus: The demand for sustainable packaging solutions is on the rise. Manufacturers are expected to invest in eco-friendly materials and processes, such as biodegradable films and recyclable woven bags. This focus on sustainability will not only meet regulatory requirements but also cater to the growing consumer demand for environmentally friendly products.
Conclusion
The evolution of FFS Woven Bags from basic woven materials to advanced packaging solutions illustrates the impact of technology and innovation on the industry. As manufacturers continue to embrace automation and advanced materials, the efficiency, durability, and customization of FFS Woven Bags are set to improve. By focusing on cost control measures and sustainability, the future of FFS Woven Bags appears bright, promising to meet the changing needs of various industries while contributing to a more sustainable packaging solution.