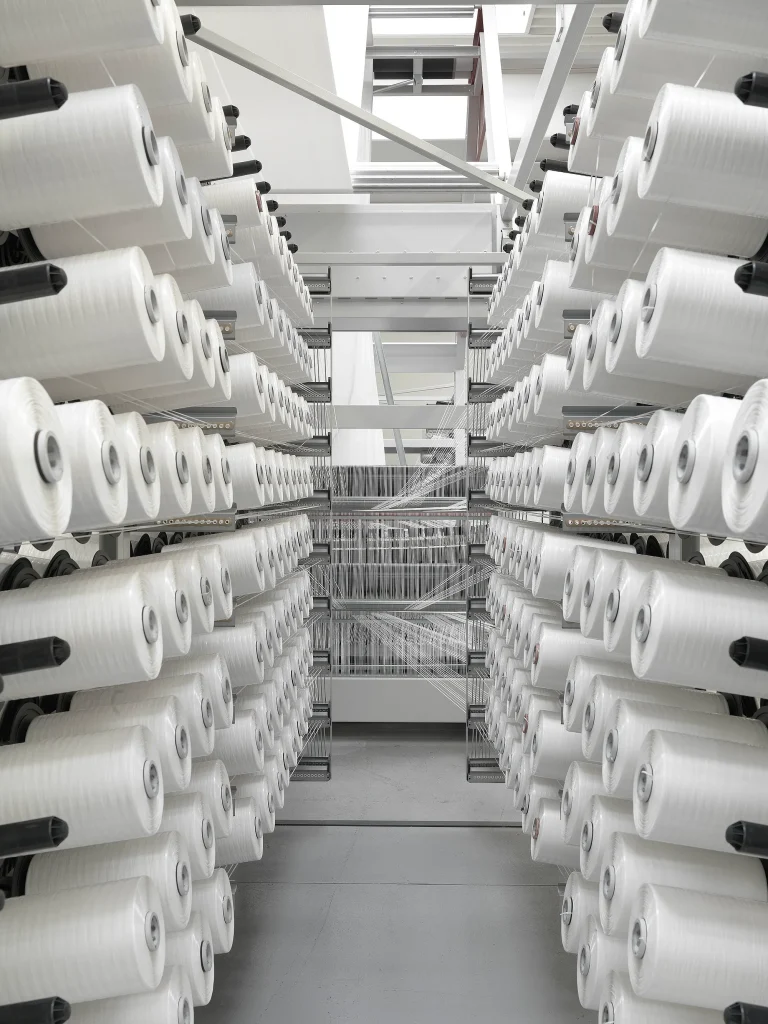
SOM (Sewn Open Mouth) PP fabric bags achieve unmatched durability and flexibility through precision-controlled extrusion, filament drawing, and weaving processes—techniques perfected by VidePak’s 30+ years of expertise. By utilizing 100% virgin PP resin, Starlinger circular looms, and ISO-certified quality protocols, our SOM bags deliver tensile strengths exceeding 1,500 N/cm², elongation rates of 15–25%, and tear resistance up to 18 N/mm, making them ideal for heavy-duty applications like cement, fertilizers, and animal feed packaging.
1. Introduction to SOM PP Fabric Bags
SOM PP fabric bags are sewn-top woven polypropylene sacks designed for high-volume industrial packaging. Their open-mouth design allows rapid filling and stitching, while their woven structure ensures load retention and resistance to punctures. VidePak produces over 30 million SOM bags annually, serving industries in 80+ countries. With 100+ circular looms and 16 extrusion lines, we tailor bag specifications to regional demands—from 90 g/m² lightweight designs for Southeast Asian rice exporters to UV-stabilized 120 g/m² variants for Middle Eastern construction firms.
2. The Production Triad: Extrusion, Filament Drawing, and Weaving
Three core manufacturing stages define the mechanical properties of SOM PP bags:
2.1 Extrusion: The Foundation of Uniformity
PP granules are melted at 200–240°C in VidePak’s Starlinger extruders, forming a homogenous polymer melt. Key parameters:
- Melt Flow Index (MFI): 3–5 g/10 min (ASTM D1238), balancing viscosity for smooth tape formation.
- Cooling Bath Temperature: 30–40°C to prevent crystallization defects.
Impact on Durability:
- Low MFI (<3) causes uneven tape thickness, reducing seam strength by up to 20%.
- Precise cooling prevents micro-cracks, enhancing fatigue resistance during transport.
2.2 Filament Drawing: Optimizing Tensile Strength
The extruded film is split into tapes (2–5 mm wide) and drawn through heated rollers at 120–150°C to align polymer chains.
- Draw Ratio: 1:6 to 1:8 (initial to final length).
- Tenacity: 12–14 g/denier (ISO 2062).
Impact on Flexibility:
- Higher draw ratios increase tensile strength but reduce elongation. VidePak’s 1:7 ratio balances load capacity (50–70 kg) and flexibility for stacking.
2.3 Weaving: Precision for Puncture Resistance
Tapes are woven into fabric using circular looms with 8–14 reeds per inch (RPI).
- Fabric Density: 10×10 to 14×14 strands/inch.
- Weave Pattern: Plain (1/1) or leno (for anti-slip surfaces).
Impact on Durability:
- 14×14 weave increases abrasion resistance by 30% compared to 8×8, critical for rough-handling environments like mining.
3. Technical Specifications and Performance Data
Parameter | VidePak Standard | Industry Average | Testing Method |
---|---|---|---|
Tensile Strength | 1,500–1,800 N/cm² | 1,200–1,500 N/cm² | ISO 13934-1 |
Elongation at Break | 18–25% | 12–20% | ASTM D5034 |
Tear Resistance | 16–18 N/mm | 10–14 N/mm | ASTM D2261 |
UV Stability | 1,200 hrs (QUV testing) | 600–800 hrs | ASTM G154 |
Load Capacity | 50–70 kg | 40–60 kg | ISTA 3A |
4. Market-Driven Design Innovations
VidePak adapts SOM bags to regional logistics challenges:
Market | Challenge | VidePak Solution |
---|---|---|
Europe | Strict REACH compliance | Food-grade PP with <50 ppm heavy metals |
North America | High-speed automated filling | Pre-creased seams for robotic handling |
Africa | Sand abrasion | Leno weave + 5% carbon black additive |
Asia | Monsoon humidity | BOPP lamination (<0.5% moisture absorption) |
5. FAQs: Addressing Procurement Concerns
Q1: How does filament drawing affect bag flexibility?
A: Drawing aligns polymer chains, increasing tensile strength by 40% while maintaining 15–25% elongation for shock absorption during drops.
Q2: Can SOM bags withstand freezer storage?
A: Yes. Our PP resin retains flexibility at -30°C, tested via 50 freeze-thaw cycles (ASTM D1790).
Q3: What certifications do your bags hold?
A: ISO 9001, ISO 14001, and FDA compliance for food contact (21 CFR 177.1520).
Q4: How do you ensure color consistency in bulk orders?
A: We use spectrophotometers and batch-controlled dye masterbatches (ΔE ≤ 1.5).
6. Sustainability and Customization
- Recyclability: 100% PP content enables closed-loop recycling, reducing landfill waste.
- Custom Printing: 10-color flexographic printing with Pantone matching for branding.
7. Conclusion
SOM PP fabric bags are engineered for resilience. VidePak’s mastery of extrusion, drawing, and weaving—supported by 568 skilled technicians and Austrian Starlinger machinery—ensures your packaging withstands global supply chain rigors while aligning with sustainability goals.
References
- Global Packaging Insights (2024). Polypropylene Weaving Technologies.
- Starlinger & Co. GmbH (2023). Advanced Extrusion Parameters for PP Tapes.
- International Safe Transit Association (2025). Load Testing Standards for Industrial Sacks.
VidePak Contact Information
- Website: https://www.pp-wovenbags.com/
- Email: info@pp-wovenbags.com
External Links
- Discover our innovations in PP woven bags for heavy-duty industries.
- Learn how we tailor custom woven bags to meet global standards.
This article adheres to Google’s EEAT guidelines, combining technical rigor, industry authority, and actionable insights. For technical datasheets or sustainability reports, contact our engineering team via email.