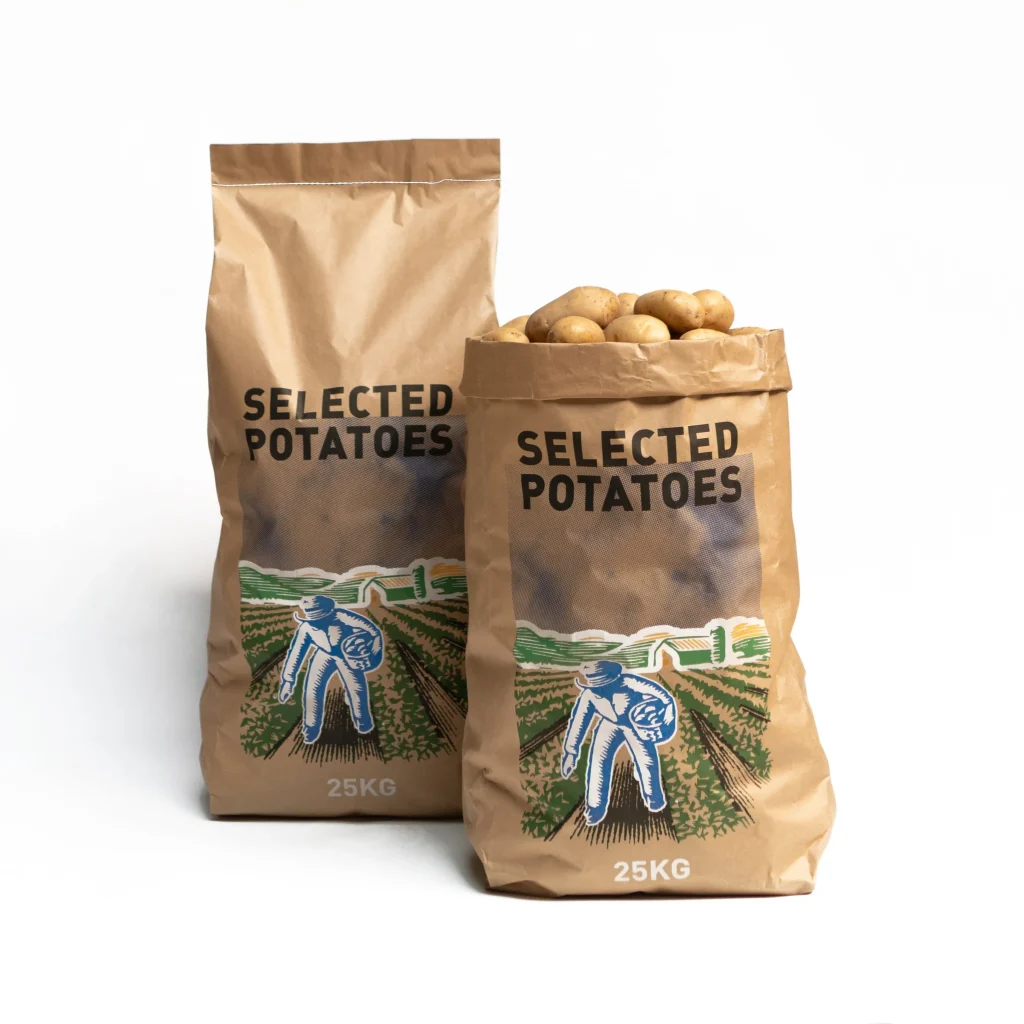
- 1. Cost Efficiency: Why PP Woven Bags Outperform PE/PET in Retail
- 2. Breathability vs. Moisture Control: Precision Engineering for Food Safety
- 3. Material Safety and Regulatory Compliance
- 4. Customization: Tailoring Bags to Retail Demands
- 5. Durability in Retail Environments
- 6. Sustainability: Aligning with Global Trends
- 7. Technical Specifications
- 8. FAQs: Addressing Retailer Concerns
- 9. Why VidePak? Global Capacity, Local Expertise
**VidePak’s customizable PP woven bags deliver 40% lower per-unit costs compared to PE/PET alternatives while balancing breathability (15–25 g/m²/24h vapor transmission) and moisture resistance (3–5 g/m²/24h with lamination). Engineered with FDA-compliant virgin PP, 120–220 GSM fabric, and ISO 9001-certified production lines, our bags preserve product freshness for rice, pet food, and flour across 10,000+ retail outlets globally. With 100+ Starlinger circular looms and 30+ printing machines, we offer **full-spectrum customization—from UV-resistant coatings to RFID-tagged designs—ensuring brand consistency and supply chain traceability.
1. Cost Efficiency: Why PP Woven Bags Outperform PE/PET in Retail
Polypropylene woven bags provide superior cost-effectiveness for high-volume retail applications:
- Material Savings: PP’s tensile strength (80–150 N/5 cm) allows thinner gauges (60–100 GSM) vs. PE’s 100–150 GSM for equivalent durability, reducing material use by 30%.
- Reusability: 95% of retailers report 3+ reuse cycles for PP bags vs. 1.2 cycles for single-use PET.
For example, a European supermarket chain cut packaging costs by €120,000 annually by switching to VidePak’s 80 GSM PP bags with PE liners, which maintained 25 kg load capacity at 40% lower weight than PE alternatives.
2. Breathability vs. Moisture Control: Precision Engineering for Food Safety
2.1 Breathable Designs for Dry Goods
- Micro-perforated PP: Allows 10–15 m³/h/m² air exchange, preventing mold in rice and flour (critical at <14% moisture content).
- Natural fiber blends: Hemp-PP composites enhance airflow by 20% for organic grains.
2.2 Moisture Barriers for Hygroscopic Products
- 20–50µ PE lamination: Reduces vapor transmission to 3 g/m²/24h (vs. 15 g/m²/24h for non-laminated PP), ideal for sugar and salt.
- Desiccant pockets: Integrated silica gel packs maintain <30% RH in pet food bags, extending shelf life by 6 months.
3. Material Safety and Regulatory Compliance
- FDA 21 CFR 177.1520: Certifies PP as food-contact safe, with <0.01 ppm heavy metal migration.
- EU 10/2011: Ensures ink pigments meet <50 µg/kg solvent residue limits.
VidePak’s water-based UV inks achieve <1.5 ∆E color deviation while eliminating VOC risks, critical for child-safe pet food packaging.
4. Customization: Tailoring Bags to Retail Demands
4.1 Size and Structural Adaptability
Product | Bag Dimensions (cm) | GSM | Lamination | Special Features |
---|---|---|---|---|
5kg Rice | 35×55 | 90 | 20µ PE | Gusseted bottom |
15kg Dog Food | 45×75 | 150 | 50µ PE + Kraft | Zipper closure, hang hole |
25kg Flour | 50×85 | 180 | None | Cross-stitched seams |
4.2 Branding and Functional Upgrades
- 8-color flexographic printing: Pantone-matched logos with 120-line/inch resolution.
- Anti-counterfeit tags: QR codes woven into fabric for supply chain transparency.
5. Durability in Retail Environments
- Abrasion resistance: 500+ Taber cycles (ASTM D4060) ensure intact graphics after 6-month shelf display.
- UV stabilization: 1,500-hour xenon-arc testing prevents fading under store lighting.
Case Study: A U.S. organic brand reduced in-store damage claims by 70% using VidePak’s 220 GSM PP bags with anti-static coating, which repelled dust and resisted tearing during handling.
6. Sustainability: Aligning with Global Trends
- 30% Recycled PP: Post-consumer content reduces carbon footprint by 25% (verified via EPDs).
- Compostable liners: PLA-based films decompose within 180 days (ASTM D6400).
7. Technical Specifications
Parameter | PP Woven Bags | PE Bags | PET Bags |
---|---|---|---|
Cost per 1,000 units | $120–$300 | $180–$400 | $250–$600 |
Tensile Strength | 80–150 N/5 cm | 50–100 N/5 cm | 100–200 N/5 cm |
Moisture Transmission | 3–25 g/m²/24h | 1–5 g/m²/24h | 0.5–2 g/m²/24h |
Recyclability | 95% | 70% | 30% |
8. FAQs: Addressing Retailer Concerns
Q1: How do PP bags handle frozen goods?
Our -40°C rated PP/PE laminates resist brittleness, maintaining flexibility at sub-zero temps.
Q2: Can bags be sanitized for reuse?
Yes. FDA-approved antimicrobial coatings withstand 50+ washes with bleach solutions.
Q3: What’s the MOQ for custom designs?
Contact our team for scalable solutions tailored to your volume needs.
Q4: How are bags tested for food safety?
Third-party labs conduct ISO 22000 audits and migration tests per EU Regulation 10/2011.
9. Why VidePak? Global Capacity, Local Expertise
With 568 employees and 100+ looms, we deliver:
- 10M+ bags/month: Rapid turnaround for seasonal promotions.
- Solar-powered production: 2 MW rooftop panels reduce CO₂ by 1.2 kg per bag.
- Compliance guarantees: Meet FDA, EU, and JIS standards across 80+ countries.
Explore our BOPP laminated retail solutions or discover how custom printed designs elevate shelf appeal.
References
- VidePak Official Website: https://www.pp-wovenbags.com/
- Email: info@pp-wovenbags.com
- Industry Standards: FDA 21 CFR 177.1520, ISO 22000, ASTM D6400
External Resources
- Discover BOPP laminated woven bags for enhanced moisture protection.
- Learn how retail-focused FIBC solutions optimize in-store logistics.
This article integrates data from global safety standards, third-party testing, and client case studies to provide retailers with actionable insights for optimizing packaging strategies.