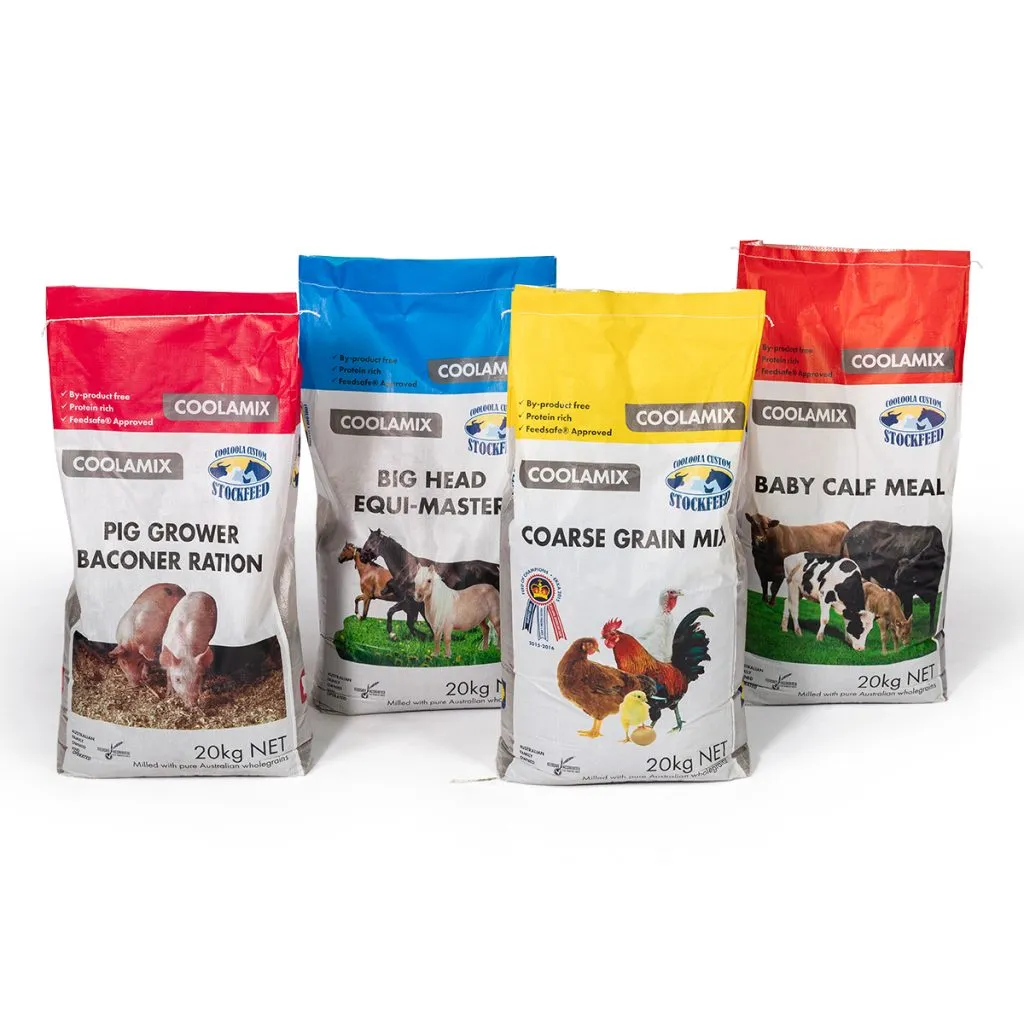
Poly-BOPP Bags, or Polypropylene Biaxially Oriented Polypropylene Bags, are gaining popularity in various industries due to their exceptional strength, durability, and versatility. At VidePak, we specialize in producing high-quality BOPP Woven Bags that meet diverse packaging needs. Our commitment to quality is evident in our comprehensive quality control measures, ensuring that every bag we produce meets the highest standards. This article will delve into the benefits of Poly-BOPP sacks and analyze common quality issues associated with woven bags, emphasizing VidePak’s rigorous testing procedures.
The Advantages of Poly-BOPP Bags
Poly-BOPP Bags offer several advantages that make them suitable for a wide range of applications:
- Durability: The biaxial orientation of the polypropylene material enhances its strength, making these bags resistant to tearing and puncturing.
- Waterproof and Leakproof: Poly-BOPP sacks are designed to be waterproof, making them ideal for packaging products that require moisture protection. This quality is particularly beneficial for industries such as agriculture, construction, and food processing.
- Versatility: These bags can be customized to meet specific needs, such as different sizes, printing options, and thicknesses. They can be used for everything from storing grains and animal feed to packaging chemicals and construction materials.
- Environmental Friendliness: As a recyclable material, polypropylene contributes to sustainable packaging solutions. Companies can reduce their environmental footprint by choosing Poly-BOPP bags over single-use plastic options.
- Cost-Effective: The long-lasting nature of Poly-BOPP bags makes them a cost-effective solution for businesses looking to minimize packaging costs in the long run.
Common Quality Issues with Woven Bags
Despite the many benefits of woven bags, quality issues can arise during the manufacturing process, impacting their performance and usability. Here are some common quality problems that can occur with woven bags:
- Inconsistent Thickness: Variability in the thickness of the bags can lead to weaker sections that may tear or fail under stress. This inconsistency can arise from poor quality control during production.
- Unfinished Edges: If the cut edges of the bags are not finished properly, they can fray, leading to potential failures in packaging integrity. This is especially critical for applications requiring leakproof and waterproof properties.
- Color Variations: Color differences can occur during the printing process, resulting in bags that do not match customer specifications. This is particularly important for brands that rely on consistent color for their packaging.
- Weight Discrepancies: The grammage (weight per unit area) of the material used can affect the bag’s overall strength. A bag that does not meet the specified grammage may not perform adequately for its intended use.
- Mechanical Properties: The tensile strength and elongation of the raw materials and finished products are vital indicators of quality. If these properties are not within specified limits, the bags may not withstand their intended loads.
- Impact Resistance: Woven bags must withstand impacts during handling and transportation. Poor impact resistance can lead to product loss and increased costs.
- UV Resistance: For bags intended for outdoor use, resistance to ultraviolet (UV) light is crucial. Insufficient UV protection can lead to degradation of the bag’s material over time.
- Environmental Compliance: Increasingly, customers demand environmentally friendly packaging solutions. If the bags do not meet environmental regulations, they may not be acceptable in certain markets.
Comprehensive Quality Control at VidePak
At VidePak, we take quality seriously. Our quality control process includes a series of rigorous tests to ensure that our Poly-BOPP Bags, including BOPP Woven Bags and Laminated Woven Bags, meet and exceed industry standards. Here are some of the key testing procedures we implement:
Quality Parameter | Testing Method | Importance |
---|---|---|
Thickness Tolerance | Caliper measurements across multiple points | Ensures consistency in strength and performance |
Cut Edge Finish | Visual inspection and edge finishing standards | Prevents fraying and improves overall integrity |
Color Consistency | Colorimetric analysis to match specifications | Maintains brand identity and aesthetic appeal |
Grammage Measurement | Weighing samples to verify weight specifications | Confirms durability and strength |
Tensile Strength | Standard tensile testing on raw and finished products | Validates ability to hold weight without failure |
Impact Resistance | Drop tests to simulate handling conditions | Ensures product safety during transport |
UV Resistance Testing | Exposure to UV light for defined periods | Assures longevity for outdoor applications |
Environmental Testing | Verification of compliance with eco-friendly standards | Meets market demands for sustainability |
These testing procedures allow us to maintain a high standard of quality throughout our production process, ensuring that our customers receive only the best products.
Conclusion
Poly-BOPP Bags are a reliable and versatile packaging solution, particularly suited for industries requiring strong, waterproof, and environmentally friendly options. However, it is crucial to address common quality issues that may arise during production. At VidePak, our commitment to excellence is demonstrated through our comprehensive quality control system, which covers a wide range of testing parameters. By ensuring the highest quality in our Poly-BOPP sacks, we help our customers achieve their packaging goals effectively and sustainably.
To learn more about the excellence of Poly-BOPP Bags, explore our detailed article on Poly-BOPP Bags.