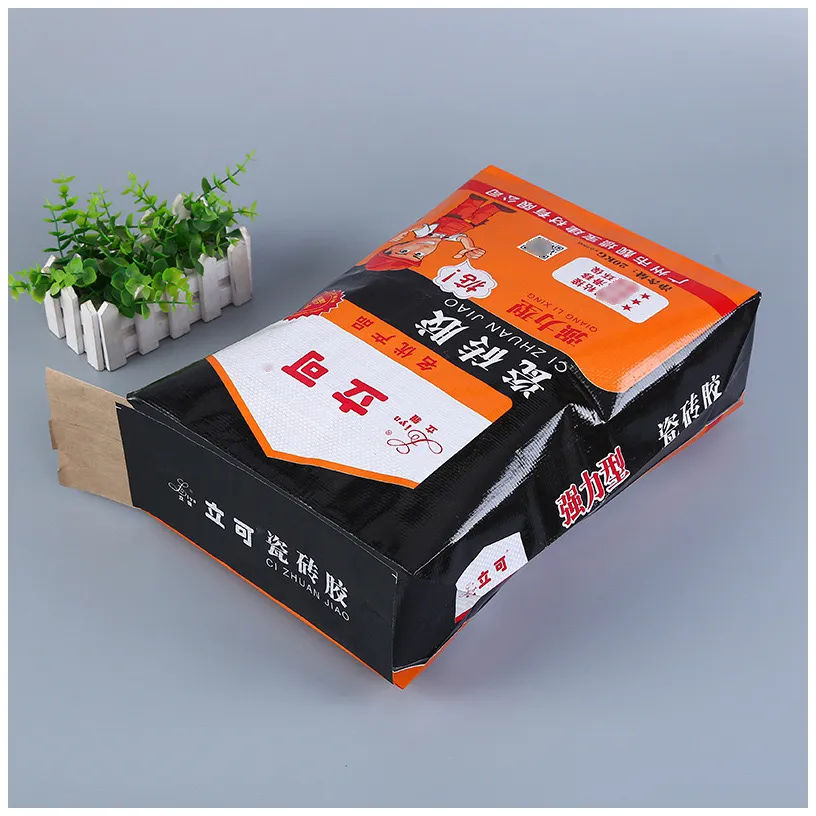
Custom woven bags are widely used for a variety of industries due to their durability, strength, and versatility. These bags, including custom woven sacks, are made from high-quality polypropylene, ensuring they meet the most demanding packaging requirements. With the growing demand for packaging that provides both security and efficiency, custom woven bags with options like printed woven bags and BOPP bags with custom printing have become key solutions for companies seeking both functional and branded packaging. However, optimizing the use of these bags goes beyond production — proper storage and warehousing practices are crucial to maximizing efficiency, reducing costs, and maintaining the quality of the bags during transportation.
The Role of Custom Woven Bags in Modern Packaging
Custom woven bags are designed to meet the specific needs of various sectors, from food and agriculture to construction and chemicals. Their customizability allows companies to tailor bags to their unique requirements, including size, strength, and printing options. For example, custom woven bags can feature logos, barcodes, and specific branding details, enhancing brand visibility and customer engagement.
These bags are made using polypropylene (PP) or Biaxially Oriented Polypropylene (BOPP), which is a strong, flexible material ideal for high-stress environments. The printed versions, known as printed woven bags, offer a wide range of customization options for marketing purposes. Whether it’s for food-grade packaging or for industrial products, the durability of the woven fabric ensures that goods remain secure throughout the supply chain.
The benefits of Custom woven sacks extend to their utility in different industries. In agriculture, these bags can be used to store everything from grains to fertilizers, providing secure containment for various goods. In the construction industry, woven sacks are used for packaging raw materials, while in the chemical industry, they help ensure safe and efficient transportation of hazardous materials.
Essential Considerations for Warehousing Custom Woven Bags
Once produced, custom woven bags are shipped to warehouses for distribution, where proper storage practices play a vital role in maintaining product integrity. Warehousing these bags involves several key factors to maximize their efficiency and to ensure they stay in optimal condition. Below, we discuss how factors like temperature, humidity, and packaging are essential for proper storage.
1. Maintaining Ideal Environmental Conditions
Custom woven bags should be stored in a controlled environment to prevent any damage caused by moisture or extreme temperatures. Ideally, a constant temperature and humidity level should be maintained. If exposed to excessive moisture, polypropylene bags can absorb water, weakening the material and reducing its strength. Furthermore, high humidity levels can lead to mildew growth on the bags.
Storing woven bags in an environment with a constant temperature of around 20°C to 25°C (68°F to 77°F) and relative humidity levels between 45% and 60% helps keep the bags in peak condition. To ensure proper storage, warehouses must have systems in place to regulate both temperature and humidity.
2. Using Advanced Packaging Techniques
Once custom woven bags are produced, ensuring that they are packed tightly and securely during storage is key. One of the ways to achieve this is by using high-pressure machinery, such as a 200MT press machine, to compact the bags into tight bundles. This compression reduces the overall storage space needed and helps prevent bags from being exposed to environmental factors, such as moisture or dust, for prolonged periods.
Another benefit of using compression is that it maximizes container space during transportation. Efficiently packing woven bags allows for more goods to be shipped in a single container, reducing shipping costs and improving overall logistics.
3. Optimizing Warehouse Space
A well-organized warehouse layout is essential for storing woven bags efficiently. With the tight packing of custom woven sacks, the warehouse space utilization can be optimized. Forklifts and automated storage systems should be used to manage large volumes of woven bags, ensuring easy access and reducing the time spent moving goods.
Additionally, stacking custom woven bags in a manner that allows air circulation between layers will help preserve their integrity. This prevents the risk of mildew formation, particularly in areas with higher humidity.
The Role of Printed PP Bags and Custom Printing
In industries where branding is key, printed PP bags offer an excellent way to enhance the visibility of products. Printed woven bags are popular for retail packaging and are widely used to showcase a company’s logo, tagline, and other essential information. With BOPP Bags with Custom Printing, companies can further customize their packaging by incorporating vibrant graphics, making their products stand out on store shelves.
Printed woven bags are made by laminating a layer of BOPP film to the woven polypropylene fabric, creating a surface suitable for high-quality printing. This is especially beneficial for businesses looking to maintain a professional image while ensuring their bags remain durable and functional. With advancements in printing technology, companies can now produce these bags in various designs, meeting the diverse demands of their customers.
Key Storage Parameters for Custom Woven Bags
To ensure the durability of custom woven sacks, especially when used for long-term storage, it is essential to consider certain key parameters. The table below outlines some of these critical parameters:
Storage Factor | Ideal Condition | Impact on Quality |
---|---|---|
Temperature | 20°C to 25°C (68°F to 77°F) | Prevents material degradation and moisture absorption. |
Humidity | 45% to 60% | Reduces the risk of mildew and material deterioration. |
Pressure (Compression) | 200MT Press | Maximizes storage space and maintains bag integrity. |
Stacking Configuration | Balanced air circulation between layers | Helps avoid moisture buildup and bag deformation. |
Packaging Type | Tight and compact bundling with plastic wrap | Ensures maximum space utilization and reduces exposure to elements. |
By adhering to these parameters, businesses can ensure that their custom woven bags remain in excellent condition throughout the storage and shipping process. In doing so, they also ensure that products remain safe, protected, and efficient to handle when needed.
Maximizing Container Space and Reducing Shipping Costs
A significant benefit of proper packaging and storage is maximizing container space. By utilizing high-pressure machinery, as mentioned earlier, custom woven sacks can be tightly packed to minimize unused space. This practice reduces the number of containers needed for transportation, lowering logistics costs and making the process more efficient.
Moreover, ensuring the tight packing of bags allows for smoother handling during unloading and stacking, thus improving warehouse operations and reducing potential damage during transport.
Conclusion
In conclusion, the storage and warehousing of custom woven bags are just as crucial as their production. To maximize the potential of these bags, companies must take into account factors such as temperature, humidity, and packaging techniques. By leveraging advanced technologies such as high-pressure presses and optimizing warehouse space, businesses can ensure the integrity of custom woven sacks and reduce transportation costs.
The versatility of custom woven bags and printed woven bags makes them an essential component of modern packaging solutions. Their strength, durability, and ability to be customized for a wide range of applications make them ideal for various industries. Proper storage and handling practices further enhance their value, ensuring that they continue to serve their intended purpose efficiently throughout the supply chain.