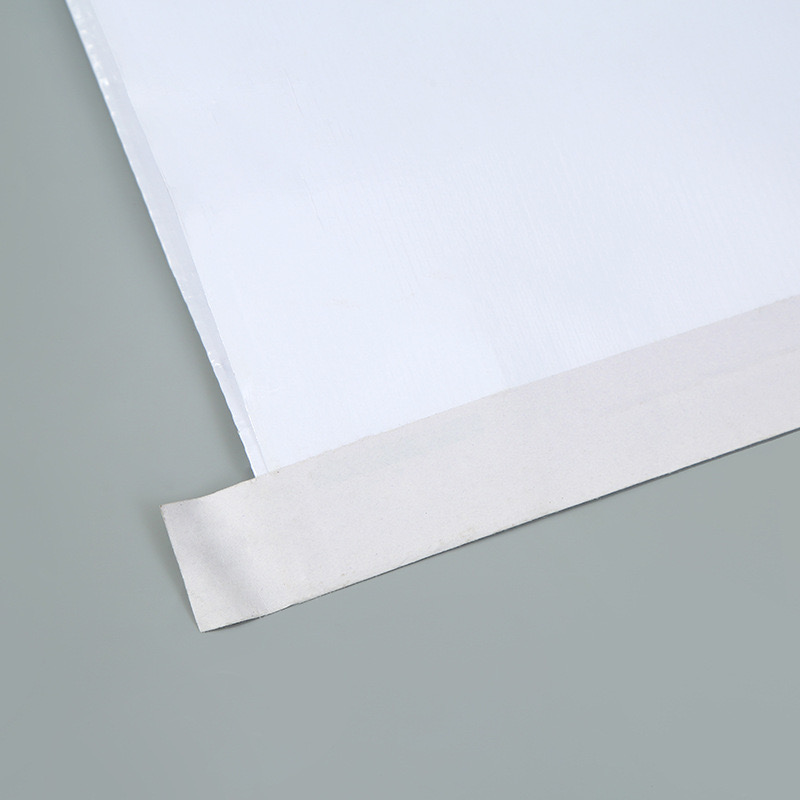
When it comes to industrial packaging, the demand for durable, reliable, and cost-efficient solutions is ever-growing. One of the most popular types of packaging bags used in various industries is the SOS PP fabric bag, also known as Self Opening Sacks, Self Opening Bags, and Self Opening Woven Bags. These bags are known for their unique self-opening feature, which makes them highly efficient for both storage and transportation, especially for bulk products. In this blog, we will explore the quality control process behind the production of SOS bags and the role that high-quality raw materials, sourced from world-renowned manufacturers, play in ensuring their superior performance.
What are SOS Bags?
SOS bags, or Self Opening Sacks, are a type of woven polypropylene (PP) bag that is designed with a self-opening mechanism at the top. This feature is particularly useful for packaging loose products such as grains, powders, chemicals, and other bulk materials. The design of the SOS bag ensures that it can open automatically when it is placed in position, minimizing the need for manual labor and speeding up the filling and sealing processes.
These bags are primarily used in industries such as agriculture, construction, food packaging, and chemicals. Due to their durability, flexibility, and ability to hold large quantities of material, they are increasingly being chosen as a preferred option for bulk packaging solutions.
The Role of Raw Material Quality
The production of high-quality SOS bags starts with the choice of raw materials. At VidePak, we prioritize the use of only the finest polypropylene (PP) and polyethylene (PE) plastic particles, sourced from industry giants like SINOPEC, CNPC, YPC, and Hengli Group. These manufacturers are known for their stringent quality standards and cutting-edge technology, ensuring that only the highest grade materials make it into the final product.
By using 100% new PP and PE plastic particles, we guarantee that our SOS bags are strong, durable, and resistant to wear and tear. The use of recycled plastic is avoided in our manufacturing process, as it can introduce impurities that may affect the bag’s strength and integrity. With the backing of trusted suppliers, VidePak ensures that the raw materials meet international standards, providing customers with bags that offer superior performance.
Quality Control at Every Step
At VidePak, quality control is an integral part of the manufacturing process. The raw materials we receive are first inspected and tested to ensure they meet the required specifications. We perform a series of checks, including melt flow index (MFI) testing, tensile strength testing, and moisture content analysis, to verify the quality of the plastic particles. Only those that pass these tests are allowed to move forward to the production stage.
Once the raw materials have been approved, they undergo a multi-step process of extrusion, weaving, lamination, and printing. At each stage of production, our experienced quality control team conducts thorough inspections to check for any defects or inconsistencies in the bags. This ensures that the bags meet both our high standards and those of our customers.
Here are some key quality control procedures that are carried out during the production of SOS bags:
Quality Control Procedure | Purpose |
---|---|
Raw Material Testing | Ensures that the polypropylene and polyethylene particles meet industry standards for strength and durability. |
Melt Flow Index Testing | Verifies the flow properties of the raw plastic to ensure smooth processing during extrusion. |
Tensile Strength Testing | Measures the strength of the finished bags to ensure they can withstand heavy loads. |
Moisture Content Analysis | Determines the amount of moisture in the raw materials to prevent issues like weakening of the fabric. |
Visual Inspection | Ensures that the bags are free from defects such as holes, tears, or printing errors. |
Strength Testing | Confirms that the bags can endure stress during transportation and handling. |
With these rigorous testing protocols in place, we ensure that the SOS bags meet the highest standards of quality and performance.
The Manufacturing Process: From Raw Material to Finished Product
The production of SOS PP fabric bags involves several critical steps, from sourcing the raw materials to the final inspection of the finished product. Here is a brief overview of the process:
- Extrusion: The first step involves melting the raw plastic particles and extruding them into thin sheets or films. This process allows the plastic to be formed into the desired shape and thickness.
- Weaving: The extruded plastic sheets are then woven into a fabric using specialized looms. This step creates the sturdy woven structure of the bags, ensuring they can hold heavy loads without breaking or tearing.
- Lamination: To enhance the strength and durability of the bags, a lamination layer is often applied. This step helps to make the bags more resistant to moisture, chemicals, and physical wear.
- Printing and Customization: Many SOS bags are customized with branding, logos, or product information. Our advanced printing technology allows for high-quality, multi-color prints to be applied to the bags, ensuring they are both functional and visually appealing.
- Final Inspection: After the bags are produced, they undergo a final round of inspections to ensure they meet our strict quality standards. This includes testing for any defects and verifying that the self-opening mechanism functions as intended.
Key Benefits of SOS PP Fabric Bags
- Durability: SOS bags are designed to withstand the rigors of transportation and storage, making them ideal for packaging heavy and bulk products.
- Self-opening feature: The self-opening mechanism saves time and labor, allowing for faster filling and sealing.
- Customization: SOS bags can be tailored to meet specific customer needs, including custom sizes, colors, and printing options.
- Environmentally friendly: By using 100% new raw materials and avoiding the use of recycled plastic, we ensure that our bags meet environmental standards and contribute to a cleaner environment.
SOS Bags in Various Industries
SOS PP fabric bags are used in a wide range of industries due to their versatility and reliability. Here are a few industries that benefit from using these bags:
- Agriculture: Farmers often use SOS bags for packaging grains, seeds, and fertilizers. The bags are designed to be both strong and breathable, allowing for the safe storage of agricultural products.
- Construction: The construction industry relies on SOS bags for storing and transporting materials like sand, gravel, and cement. Their durable construction ensures that they can hold heavy loads without tearing or breaking.
- Chemicals: SOS bags are used for packaging and transporting chemical powders, plastics, and other bulk chemicals. Their resistance to moisture and chemicals makes them an excellent choice for this industry.
- Food Packaging: SOS bags are also used in the food industry for packaging grains, flours, and other bulk food products. The bags are designed to maintain the quality and freshness of the product during storage and transportation.
Conclusion
The production of high-quality SOS PP fabric bags relies heavily on the selection of premium raw materials and a rigorous quality control process. By sourcing our materials from trusted suppliers like SINOPEC, CNPC, YPC, and Hengli Group, and adhering to strict testing and inspection protocols, VidePak ensures that our SOS bags meet international standards of strength, durability, and performance.
For more insights into the versatility and benefits of SOS bags, you can read more about them in the following articles:
By choosing VidePak, you can be assured of top-quality, durable, and customizable SOS bags that will meet all of your bulk packaging needs.