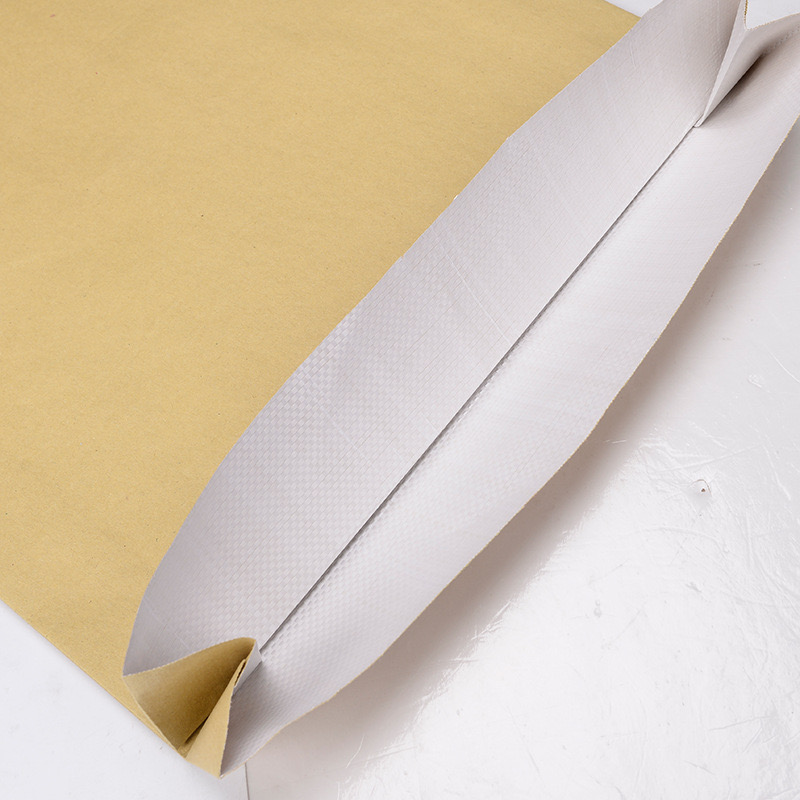
Food packaging is a critical area in manufacturing, especially when dealing with products like grains, flour, and animal feed. The materials used for packaging food must meet strict safety standards to avoid contamination and preserve food quality. Food Grade Woven Fabric Bags, including Food Grade Woven Sacks, Food Grade PP Bags, and Food Grade Polypropylene Bags, are commonly used in this sector. In this article, we will explore key considerations in the selection, production, packaging, and storage processes of these bags, as well as how warehouses must be managed to ensure safety and efficiency.
Importance of Food Grade Standards
Food Grade Woven Fabric Bags are designed to protect the food contents while also being safe for human consumption. These bags need to meet specific standards that guarantee they do not introduce harmful substances into the food they contain. The primary materials used to make Food Grade Polypropylene Bags or Food Grade Poly Bags are non-toxic and free from chemicals that might compromise food safety. These bags are made with materials that comply with various food safety regulations, including FDA (Food and Drug Administration) and EU food-grade certifications.
To ensure that the bags meet food-grade standards, manufacturers must strictly control the raw materials and production process. Here are some considerations to keep in mind for each stage:
1. Material Selection
The process begins with the careful selection of polypropylene (PP) or polyethylene (PE) as the primary material. These polymers are not only durable and flexible but also non-reactive, which is essential for food safety. Food Grade Polypropylene Bags are made with virgin polypropylene, meaning the material has not been recycled and does not contain any potentially harmful chemicals or contaminants.
Key Material Parameters for Food Grade Bags:
Material Type | Safety Compliance | Common Applications |
---|---|---|
Polypropylene (PP) | FDA, EU Food Grade | Grains, flour, sugar |
Polyethylene (PE) | FDA, EU Food Grade | Produce, bakery items |
Using virgin material reduces the risk of contamination that might occur from recycled plastics. Additionally, it is essential that the bags are free of heavy metals, toxic substances, and any chemicals that could leach into food.
2. Production Process
Food Grade Woven Sacks are typically produced by weaving polypropylene fibers into a fabric. This fabric is then shaped into bags that are either sewn or welded to form their final structure. During the production process, cleanliness is paramount. Facilities must adhere to strict hygiene standards, and workers should use appropriate gear to avoid contamination.
Another critical aspect is the use of specialized equipment that ensures the quality of the bags. For instance, Starlinger equipment, known for its precise weaving and lamination technologies, plays an essential role in producing high-quality woven fabric bags for the food industry. These machines help produce uniform bags that are both strong and safe for food packaging.
To improve bag strength and durability, multi-layered films or coatings may be used. Food Grade Woven Fabric Bags are often coated with additional layers, such as PE or EVA, to offer moisture resistance and better protection for the contents.
3. Packaging and Sealing
After the Food Grade Woven Bags are manufactured, they must be packaged carefully to maintain their quality and cleanliness. Packaging plays a significant role in the protection of food products and ensuring that bags remain intact during transport and storage.
Packaging considerations include:
- Sealing Methods: Ensuring that each bag is securely sealed helps prevent contaminants from entering the bag and protects the food from external elements.
- Printing and Labelling: Bags are often printed with information about the food inside, such as nutritional information, ingredients, and expiration dates. The printing process must also use non-toxic inks to ensure the safety of food products.
4. Transportation and Logistics
Once the Food Grade Polypropylene Bags are packaged, they need to be transported safely to their destination. This stage of the process requires careful consideration to prevent damage during transit. The bags should be stacked in a manner that prevents crushing or puncturing.
One of the most efficient ways to transport these bags is by maximizing space usage in containers. Food Grade Woven Fabric Bags are highly flexible, which allows for compact stacking, ensuring that transport costs are minimized. Proper planning can lead to cost savings and optimized storage for food-grade packaging in warehouses.
Warehouse Considerations: Temperature and Humidity Control
The proper storage of Food Grade Woven Sacks is just as important as their production. Warehouses must maintain the correct environmental conditions to prevent contamination and degradation of the bags and the food they contain. Food Grade Poly Bags should be stored in a temperature-controlled environment that maintains a constant, cool temperature to prevent the growth of mold or bacteria.
Key Storage Parameters:
- Temperature: The ideal storage temperature is typically between 15°C and 25°C.
- Humidity: Humidity levels should be controlled to stay between 50% and 60% to prevent moisture from entering the bags and affecting the food quality.
Moreover, storage facilities should be free of pests and contaminants. Food-grade bags should never be exposed to harsh chemicals, direct sunlight, or high humidity levels, all of which can compromise their structural integrity.
Use of Heavy-Duty Press Machines
To ensure optimal storage and efficient packaging, advanced equipment like 200MT pressure machines can be employed to tightly compress the bags, reducing the air volume in the bags and maximizing the use of space in containers. This is especially crucial when dealing with bulk packaging, as it helps reduce the overall transportation costs.
Using these advanced machines also ensures that each bag is uniformly compressed, helping to prevent the deformation of the bags during transportation or storage.
Optimizing Container Space
A critical component of the logistics chain involves maximizing container space to ensure that shipments are efficient. By employing pressure machines and careful stacking, businesses can ensure that as many bags as possible fit into a single container, reducing the number of shipments required and lowering transportation costs.
Food Grade Woven Bags in Practice
When it comes to practical applications, industries like food processing, agricultural companies, and retailers rely heavily on Food Grade Polypropylene Bags for bulk packaging and storage. For example, Food Grade Woven Fabric Bags are used to package grains, flour, sugar, and rice, while Food Grade Woven Sacks are ideal for high-volume food products that require extra strength and protection during shipping. Food Grade PP Bags are commonly used in the packaging of agricultural products like seeds and animal feed.
Conclusion
The production, packaging, and storage of Food Grade Woven Fabric Bags require a meticulous process to ensure food safety and quality. From the careful selection of non-toxic, virgin materials to using high-tech machinery and optimizing storage conditions, each step plays a crucial role in ensuring that food-grade packaging meets regulatory standards. Moreover, warehouse management practices, such as maintaining optimal temperature and humidity levels and maximizing container space, help ensure that food products remain safe, fresh, and efficiently delivered.
By adhering to stringent standards and embracing technology, companies can continue to innovate and provide food-safe packaging solutions to meet the evolving needs of the food industry.