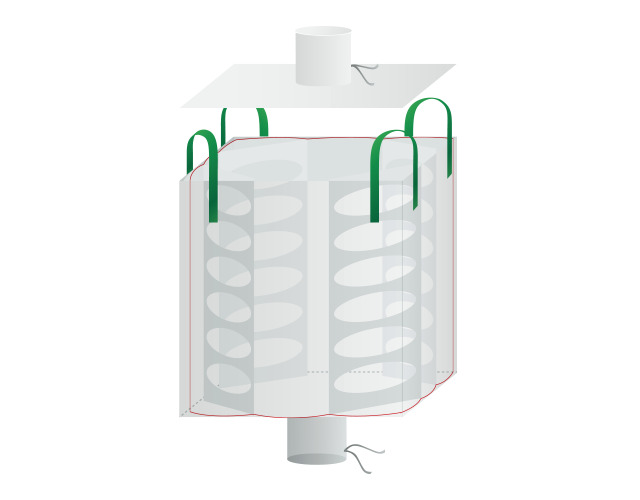
When it comes to industrial packaging solutions, FIBC Jumbo Bags have gained prominence for their versatility, strength, and efficiency. These Bulk bags, also known as Ton bags, are essential for transporting large quantities of products across various industries. Whether you need to store chemicals, agricultural products, or construction materials, FIBC Bags offer a durable, cost-effective solution. At VidePak, we specialize in manufacturing high-quality FIBC Jumbo Bags with advanced features that enhance performance and reliability. In this article, we will delve into the production process of Jumbo Bags, focusing on our use of cutting-edge equipment from renowned suppliers like Starlinger and W&H.
We take pride in the FIBC Jumbo Bags we produce, with each bag designed to withstand heavy loads and extreme conditions. The bags feature a reinforced X-shaped and cross-bottom design, offering extra stability and support. This unique construction ensures that our Bulk bags maintain their shape even when filled with heavy, dense materials. These reinforced Ton bags are built to last, providing both safety and efficiency during transportation and storage. You can learn more about FIBC Jumbo Bags in this detailed article.
Key Features and Technical Specifications of Our FIBC Jumbo Bags
To understand the technical excellence of our FIBC Bags, let’s look at some key product parameters. Below is a table summarizing the specifications of our Jumbo Bags, which highlight their strength and suitability for various industrial applications.
Feature | Description |
---|---|
Bag Type | FIBC Jumbo Bags, Bulk bags |
Bag Shape | X-shaped and cross-bottom reinforced |
Material | High-quality PP (Polypropylene) |
Capacity | 500 kg to 2000 kg |
Dimensions | Customizable (Width, Height, Length) |
Liner | Optional (PE, aluminum, or no liner) |
Printing | Multi-color custom printing available |
Bottom Type | X-shaped or cross-bottom reinforced |
UV Protection | Available for outdoor use |
Certification | ISO 9001, ISO 14001, REACH compliant |
The Production Process of FIBC Jumbo Bags
The production of FIBC Jumbo Bags is a meticulous process that requires state-of-the-art machinery and expertise. Each stage of the production cycle—from extrusion and weaving to coating, printing, and bag manufacturing—plays a crucial role in ensuring the bags’ high-quality standards.
1. Extrusion and Filament Production
The first stage in the production of FIBC Bags is extrusion, where polypropylene (PP) resin is melted and formed into fine filaments. These filaments are the building blocks for the fabric that will make up the bag. At VidePak, we use advanced extrusion lines provided by Starlinger, a globally recognized leader in the production of high-quality equipment. This technology ensures that the PP fibers are strong, durable, and uniform.
2. Weaving the Fabric
Once the filaments are created, they are woven together to form the fabric of the bag. The weaving process involves a series of parallel and perpendicular threads interlacing to create a durable and flexible material. For FIBC Jumbo Bags, the fabric needs to be strong enough to handle the weight of heavy materials, yet flexible enough for easy folding and storage.
Our weaving machines are sourced from Starlinger and are designed to handle the intricacies of industrial-grade fabrics. These circular looms produce a dense, high-strength weave that is key to ensuring the bag’s load-bearing capacity. The FIBC Bags produced using these looms are reinforced to support weights ranging from 500 kg to 2000 kg, making them suitable for a wide variety of applications.
3. Coating the Fabric
In many cases, the woven fabric needs to be coated to enhance its durability and protect it from external elements. This is especially true for bags intended for outdoor use or those requiring resistance to moisture and UV rays. At VidePak, we offer various coating options for our Bulk bags, including polyethylene (PE) or aluminum film coatings.
The coating process is managed by our high-precision W&H machines. These machines ensure that the coating is applied uniformly, providing an extra layer of protection against external factors like UV light, water, and chemicals.
4. Printing and Customization
One of the unique aspects of our FIBC Bags is the ability to customize them with high-quality printing. Whether you need logos, brand names, or instructions, our advanced printing machines ensure vibrant and durable designs. The printing process uses multi-color systems that can handle intricate designs and large-scale runs.
Our FIBC Jumbo Bags offer not only strength but also customization to enhance your brand’s presence in the market. The printing capabilities ensure that your bags are not only functional but also a promotional tool for your business.
5. Bag Manufacturing and Final Testing
Once the fabric has been woven and coated, and the printing is complete, the fabric is cut and sewn into the final Jumbo Bag shape. This step is where the bags are fitted with handles, lifting loops, and other accessories needed for safe handling.
Before the FIBC Bags are shipped out, each bag undergoes rigorous quality control testing. This includes load testing, seam strength tests, and checks for defects. At VidePak, we work closely with Starlinger to ensure that our bags meet the highest standards for safety, strength, and durability.
6. Storage and Shipping
Once the FIBC Jumbo Bags pass all tests, they are packaged and stored ready for shipment. With a capacity ranging from 500 kg to 2000 kg, these bags are typically stacked in warehouse areas or transported via trucks and containers. Whether for domestic or international shipping, our Ton bags are designed for efficient handling and long-lasting performance.
Advanced Equipment and Technology from Starlinger and W&H
At VidePak, we are committed to using the most advanced equipment available in the market to produce our FIBC Jumbo Bags. Our partnership with equipment suppliers like Starlinger and W&H is a key factor in ensuring the quality and consistency of our products.
Starlinger is a leader in the design and manufacture of woven fabric machinery, and their circular looms are renowned for their durability and precision. The high-efficiency machines help us create strong, flexible woven fabrics that meet the most demanding specifications for FIBC Bags.
W&H provides us with the advanced extrusion lines and coating systems that are critical to the durability of our Bulk bags. These machines allow us to apply coatings that offer UV protection and moisture resistance, ensuring the bags perform optimally in various conditions.
Conclusion
The production of FIBC Jumbo Bags is a complex process that requires high-quality materials, advanced machinery, and strict quality control procedures. At VidePak, we are proud to offer Bulk bags that are both strong and versatile, designed to meet the needs of industries ranging from agriculture to construction. By leveraging cutting-edge technology from Starlinger and W&H, we ensure that every Ton bag is manufactured to the highest standards, offering reliable and safe transportation solutions.
For more information on FIBC Bags, please refer to our in-depth article on FIBC Jumbo Bags. If you’re interested in learning more about the benefits of Bulk bags for your business, be sure to check out our article on Bulk bags and their versatile applications.