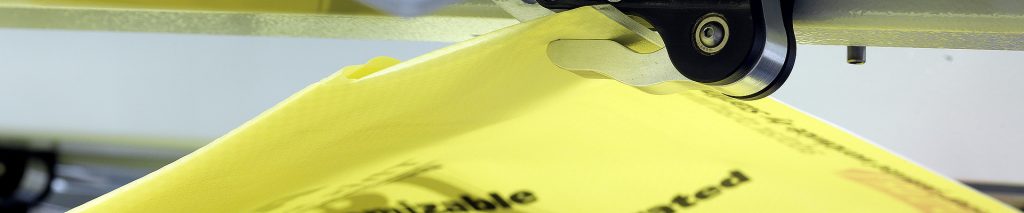
Waterproof woven bags, also known as Waterproof Woven Sacks or Waterproof PP Bags, are designed to offer protection against moisture and various environmental elements. These bags are a critical packaging solution for industries that require the storage and transportation of goods that may be sensitive to humidity or liquid exposure. Their versatility in design, material selection, and manufacturing process allows them to cater to a wide range of uses, from agricultural products to industrial materials. In this blog, we will explore the methods used to make woven bags waterproof, the types of materials used, and how various additives and fillers enhance the bags’ performance.
For more details on how Waterproof Woven Bags are revolutionizing packaging, you can visit this link. Additionally, if you are interested in understanding more about Waterproof PP Bags, check out this resource.
How Waterproof Woven Bags Achieve Their Protective Qualities
Waterproof Woven Bags are produced through a combination of material selection, manufacturing techniques, and sometimes special coatings that provide moisture resistance. Several methods exist to ensure the waterproof nature of woven sacks, each serving distinct purposes depending on the intended use of the bag.
1. Laminated Coatings
One of the most common methods for achieving waterproof qualities in woven bags is through lamination. This involves applying a plastic film, such as BOPP (Biaxially Oriented Polypropylene), to the surface of the woven polypropylene fabric. The laminated layer forms a protective barrier that prevents water or moisture from penetrating the bag.
Benefits of Laminated Waterproof Woven Bags:
Feature | Description |
---|---|
Durability | Offers high resistance to tears and punctures |
Water Resistance | Highly effective in preventing water ingress |
Customization | Available in a variety of sizes and prints for branding and packaging needs |
Versatility | Can be used for agricultural, construction, and industrial packaging |
Lamination enhances both the aesthetic and functional properties of the bag, making it suitable for both industrial and consumer goods packaging.
2. Extrusion Coatings
Another method to enhance waterproof qualities is through extrusion coating, where molten plastic is applied to the surface of the woven fabric. This process results in a more uniform coating compared to lamination, offering better protection against moisture, especially for heavier-duty applications.
Extrusion-coated bags are often used in situations where bags need to be more robust and capable of holding materials for long periods without risk of moisture damage. The added plastic layer increases the bag’s overall strength and ensures the integrity of the contents.
3. Polyethylene (PE) Liners
For added moisture protection, some woven bags are equipped with an internal polyethylene (PE) liner. This liner serves as an additional barrier to water, enhancing the bag’s ability to protect sensitive materials, particularly in the agricultural and chemical industries. The PE liner can be inserted as a separate layer or bonded with the outer woven fabric to prevent leakage or seepage of liquids.
Understanding the Role of Materials: PP vs. PE in Waterproof Woven Bags
When it comes to the construction of Waterproof Woven Bags, material selection plays a vital role in determining the bag’s performance, cost, and durability. Two common materials used in woven bags are Polypropylene (PP) and Polyethylene (PE), each offering distinct advantages.
Polypropylene (PP) in Waterproof Woven Sacks
Polypropylene is a thermoplastic polymer known for its strength, flexibility, and chemical resistance. PP is commonly used for producing woven bags because it is cost-effective, durable, and has a high tensile strength. When used in Waterproof Woven Bags, PP provides the necessary resistance to environmental stress while maintaining the bag’s overall shape and structural integrity.
Key Properties of PP in Waterproof Woven Bags:
- Durability: PP bags are tear-resistant, even under rough handling.
- Moisture Resistance: While PP is not inherently waterproof, when used with coatings or liners, it becomes highly effective against moisture ingress.
- Flexibility: The material can be woven into various patterns, providing flexibility in terms of size, design, and load-bearing capacity.
Polyethylene (PE) for Waterproof Poly Bags
Polyethylene, particularly low-density polyethylene (LDPE) or high-density polyethylene (HDPE), is another common material used in packaging, particularly for Waterproof Poly Bags. PE bags are known for their superior moisture-proof capabilities due to the polymer’s low permeability to water.
Key Properties of PE in Waterproof Poly Bags:
- Excellent Water Barrier: PE has a lower moisture transmission rate compared to PP, making it ideal for more stringent waterproofing requirements.
- Flexibility and Lightness: PE bags are generally lighter and more flexible than PP bags, though they are less durable in terms of puncture resistance.
- Low Cost: PE is also a cost-effective solution, particularly in applications where durability is less critical.
Additives and Fillers for Enhanced Waterproof Performance
To further improve the waterproof properties and overall performance of woven bags, manufacturers often incorporate various additives and fillers during production. These substances help to improve the chemical, physical, and environmental resistance of the bags.
1. Anti-UV Additives
Anti-UV agents are commonly added to woven bags to protect them from the damaging effects of ultraviolet (UV) rays, which can cause degradation over time. UV-resistant woven bags are particularly useful for outdoor storage or transportation of goods. These additives ensure that the bags maintain their strength and protective qualities even when exposed to direct sunlight for extended periods.
2. Anti-Oxidants
To prevent the material from breaking down due to oxidation, anti-oxidant additives are incorporated into the manufacturing process. These additives help prolong the life of the bags, especially in environments where exposure to oxygen and high temperatures is common.
3. Fire Retardants
For certain applications, particularly in the transportation and storage of flammable materials, fire retardant additives are used to make woven bags resistant to fire. These additives reduce the risk of the bags catching fire, ensuring a higher level of safety in industrial environments.
4. Anti-Microbial Additives
In some cases, anti-microbial additives are used to prevent the growth of mold, mildew, and bacteria. This is particularly important in applications where the bags are used to store food products or agricultural materials that may be prone to spoilage.
Applications of Waterproof Woven Bags
The versatility of Moisture Proof Woven Bags makes them suitable for a wide range of industries and applications. Below are a few notable uses:
Agricultural Industry
Waterproof Woven Sacks are commonly used in the agricultural industry for packaging grains, seeds, fertilizers, and other products that need protection from moisture and external elements. These bags help maintain the quality of the products by preventing mold, rot, and spoilage caused by moisture exposure.
Construction and Building Materials
Woven bags with waterproof coatings are often employed in the construction industry for storing and transporting cement, sand, and other building materials. Since construction materials are often exposed to the elements, Waterproof Poly Bags ensure that the contents stay dry and intact.
Chemical and Industrial Applications
Chemical manufacturers often use Waterproof Woven Sacks for packaging fertilizers, chemicals, and powdered products. The waterproof properties prevent the contents from reacting with moisture, ensuring the integrity of the product during storage and transportation.
Conclusion
Waterproof Woven Bags are a critical packaging solution in industries where moisture resistance is vital. Whether through lamination, extrusion coatings, or the use of PE liners, these bags provide an effective barrier against water, helping to protect goods from damage. With the use of additives like anti-UV agents and anti-oxidants, the bags’ performance can be enhanced further, ensuring long-lasting durability. By selecting the appropriate materials—such as PP or PE—manufacturers can meet the specific needs of different applications, ensuring that Waterproof Woven Sacks continue to offer reliable protection for a variety of industries.
For further reading on Waterproof PP Bags, explore this article.