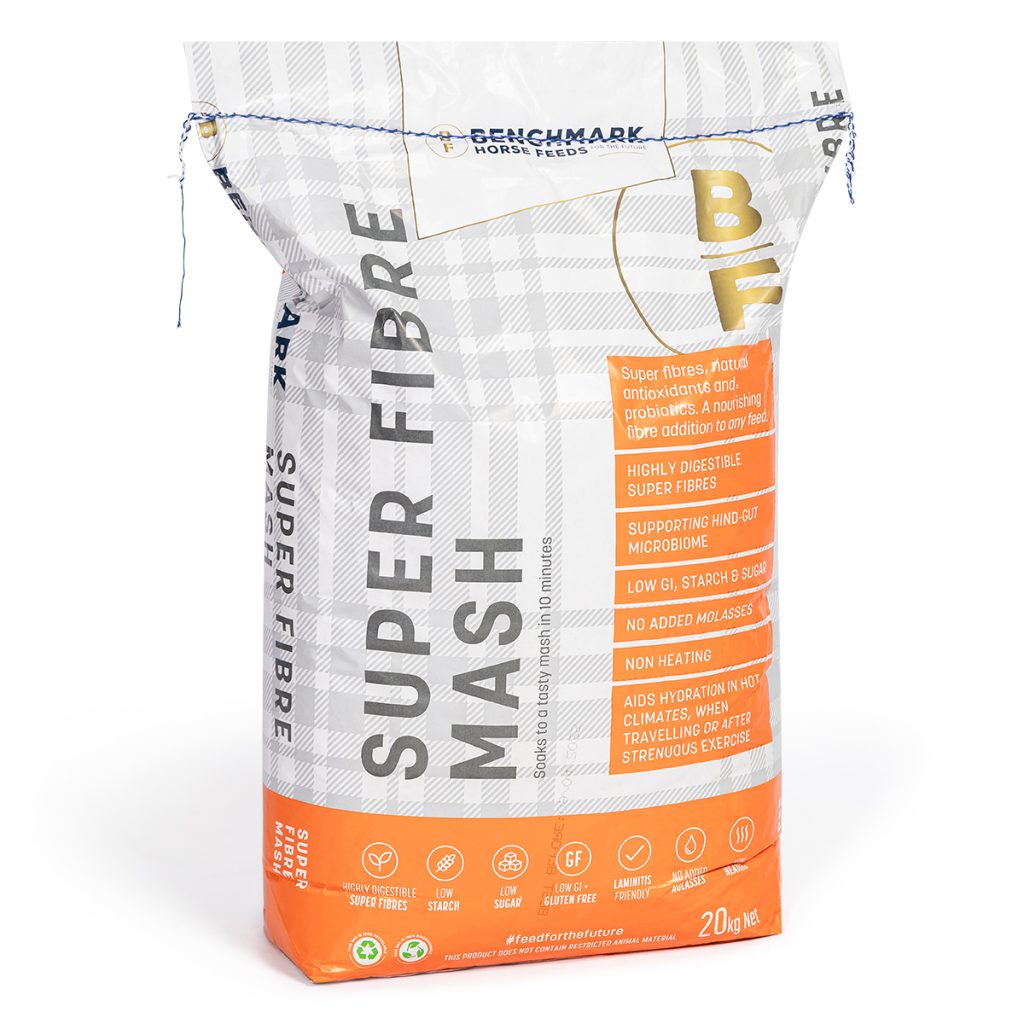
When it comes to packaging solutions for food products, maintaining hygiene and quality is paramount. The demand for Food Grade Woven Fabric Bags has surged due to their ability to safely transport and store food products while offering durability and versatility. These bags, also known as Food Grade Woven Sacks, Food Grade PP Bags, Food Grade Polypropylene Bags, and Food Grade Poly Bags, must meet strict standards to ensure they do not compromise food safety.
In this article, we will delve into the various stages involved in the manufacturing process of Food Grade Woven Fabric Bags, from material selection to production, packaging, and transportation. We will also explore how the right equipment and technology, such as those provided by renowned suppliers like Starlinger and W&H, play a crucial role in producing high-quality bags that meet food safety standards.
Material Selection for Food Grade Woven Bags
The first and most crucial step in ensuring the quality and safety of Food Grade Woven Fabric Bags is the selection of the right materials. Polypropylene (PP) is the most common material used for these bags due to its excellent strength, flexibility, and resistance to moisture. However, not all PP materials are suitable for food packaging. Food-grade PP is specifically manufactured to meet stringent safety and regulatory standards.
Key considerations during material selection include:
- Purity of Polypropylene: The raw PP used in food-grade bags must be free of contaminants and toxins that could leach into food products. Food-grade PP is made from virgin materials, not recycled PP, to ensure it meets food safety standards.
- Compliance with Food Safety Regulations: In many countries, packaging used for food must comply with regulations set by agencies such as the FDA (U.S. Food and Drug Administration) or EFSA (European Food Safety Authority). These standards govern the materials’ potential interaction with food.
- Food Safety Certifications: Manufacturers must obtain certifications that validate their products’ compliance with food safety standards. Common certifications include ISO 22000, which ensures that food safety management systems are followed during production.
Once the material is selected, the production process can begin.
The Production Process of Food Grade Woven Bags
The production of Food Grade Woven Polypropylene Bags involves multiple steps, each critical to ensuring the end product is of the highest quality. From extrusion and weaving to coating and printing, each stage plays a role in maintaining the integrity and safety of the bags.
1. Extrusion and Drawing of Polypropylene Yarn
The first step in the production process is the extrusion of polypropylene (PP) resin into filaments. These filaments are then drawn into yarn, which will later be woven into fabric.
- Extrusion Quality: The quality of the extrusion process directly affects the strength and flexibility of the yarn. Modern extrusion lines, like those provided by Starlinger, ensure precise control over the thickness and consistency of the yarn.
- Filament Thickness: The yarn’s thickness and texture are critical for the durability of the bags. Food Grade PP Bags typically use finer filaments to ensure the bags are lightweight yet durable.
2. Weaving the Fabric
Once the yarn is produced, it is woven into fabric. The weaving process involves interlacing the polypropylene filaments to form a tight, durable weave that provides the bags with their characteristic strength.
- Weaving Machines: High-quality weaving machines, such as those from Starlinger and W&H, are essential for producing uniform, high-density fabric. These machines allow for precise control over the weave pattern, which can impact the bag’s strength, breathability, and overall performance.
- Customization: For food-grade applications, manufacturers may also customize the fabric’s weave to enhance its resistance to moisture, contaminants, and UV rays, ensuring the food stays fresh during transportation and storage.
3. Coating the Fabric
In many cases, the woven fabric is coated with a layer of polyethylene (PE) or another suitable material to improve its resistance to water, dirt, and other external factors. This coating enhances the protective properties of the Food Grade Poly Bags.
- Coating Materials: The coating material must be food-safe and not contain any harmful chemicals that could migrate into the food. Companies like VidePak ensure that only high-quality, certified coatings are used.
- Coating Techniques: Coating techniques such as lamination are employed to provide the fabric with an additional barrier against moisture, ensuring that food products remain fresh during transportation.
4. Printing and Branding
Once the woven fabric is coated, the next step is printing. Printing is not just for branding but also for ensuring that the bag meets regulatory requirements, such as labeling food content, usage instructions, and safety guidelines.
- Printing Quality: The inks used for printing must be food-safe and non-toxic. Advanced printing machines, such as those from Starlinger, ensure that the designs are sharp, vibrant, and long-lasting without compromising food safety.
- Customization: Custom printing allows companies to include branding or product information on the bags, providing both marketing and regulatory benefits.
5. Bag Formation and Quality Control
The final step in the production of Food Grade Woven Sacks is the formation of the bags. This process involves cutting the woven fabric into the appropriate sizes, then sewing or heat-sealing the edges to form the bags.
- Sealing Techniques: Advanced heat-sealing machines ensure that the bags are tightly sealed, preventing any contaminants from entering.
- Quality Control: Rigorous quality control checks are performed at every stage of the process to ensure that the bags meet the required standards for food safety. This includes testing for strength, moisture resistance, and the absence of harmful chemicals.
Packaging and Transportation
Once the Food Grade Polypropylene Bags are produced, they are packaged for transport. During this stage, maintaining the integrity of the bags is crucial to avoid contamination during shipping and handling.
- Packaging Materials: Food-grade bags should be packaged in clean, non-toxic materials. Often, bags are packed in cardboard boxes or wrapped in plastic to protect them from dust, dirt, and moisture.
- Storage Conditions: The bags must be stored in a dry, clean environment before they are shipped to prevent contamination or degradation of the material.
- Transportation Considerations: During transport, the bags should be handled with care to avoid damage that could lead to contamination. Proper stacking and securing of the bags are important to maintain the quality of the packaging until it reaches the customer.
Why VidePak Chooses Starlinger and W&H Equipment
At VidePak, we prioritize the use of the best equipment to produce high-quality Food Grade Woven Bags. We rely on machinery from Starlinger and W&H, two of the most respected names in the industry, to ensure that our production processes are efficient and meet the highest standards.
- Starlinger provides advanced circular looms and extrusion lines that produce consistent and durable yarn, essential for creating strong and reliable bags.
- W&H supplies cutting-edge printing and lamination machines that allow us to customize bags with vibrant designs while maintaining food safety standards.
Conclusion
The production of Food Grade Woven Fabric Bags involves a rigorous process that requires careful attention to detail at every stage, from material selection to final quality control. By using high-quality raw materials, state-of-the-art machinery from suppliers like Starlinger and W&H, and adhering to strict food safety regulations, manufacturers can ensure that these bags meet the highest standards for food safety and quality. At VidePak, we are committed to delivering the best food-grade packaging solutions to our customers worldwide.
For more information, check out our detailed guides on Food Grade Woven Fabric Bags and Food Grade PP Bags.