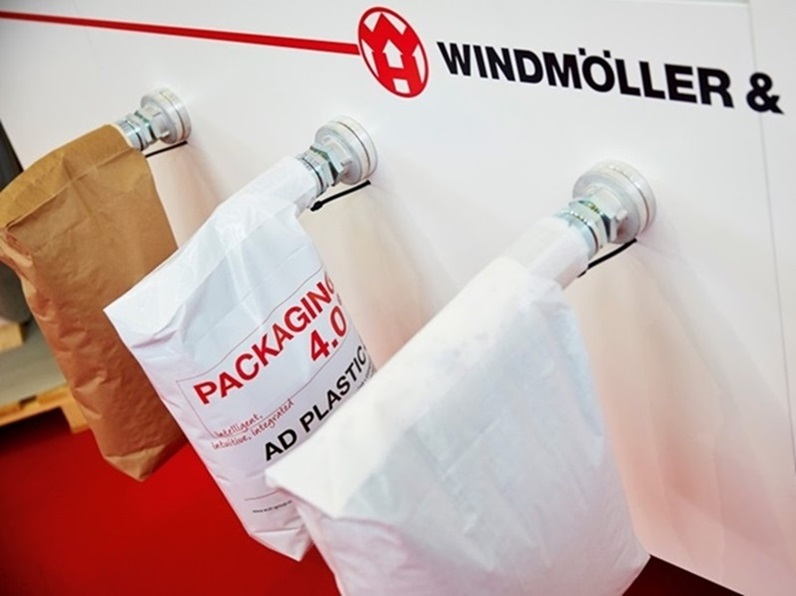
In the world of packaging, Printed BOPP Woven Bags are increasingly becoming the go-to choice for industries looking for durability, aesthetic appeal, and high-quality performance. These bags, often used in sectors ranging from agriculture to chemicals, are created using advanced technologies that ensure high resistance, moisture protection, and longevity. But what truly sets them apart is their ability to combine practical design with excellent printing capabilities. As manufacturers, we pay close attention not only to the design but also to the raw materials used in creating these bags. With the right raw materials and a rigorous quality control system, manufacturers can ensure that Printed BOPP Woven Sacks meet the highest standards in the market.
One of the most essential elements that influence the quality of Printed PP Bags is the quality of the raw materials, specifically the polypropylene (PP) and polyethylene (PE) pellets used in production. The quality control measures in place at our company ensure that only the best materials are used, contributing directly to the strength, durability, and print quality of the finished products. As such, our collaboration with top-tier suppliers like SINOPEC, CNPC, YPC, and Hengli Group guarantees a steady supply of high-quality materials, sourced only from reputable manufacturers in the plastic industry.
Table: Key Specifications of Printed BOPP Woven Bags
Parameter | Value |
---|---|
Material | Polypropylene (PP) and Polyethylene (PE) |
Bag Type | BOPP Woven Bags, PP Woven Sacks |
Size Range | Custom sizes available |
Printing | Up to 6 colors, custom designs |
Durability | High strength, UV resistant |
Capacity | Varies from 5 kg to 50 kg |
Applications | Agricultural products, chemicals, food grains, construction, etc. |
Raw Material Sourcing and Quality Control
The process of manufacturing Printed PP Woven Bags begins with the careful selection of raw materials. These materials are crucial because they determine the performance of the final product in various applications. At VidePak, we source our plastic pellets from renowned suppliers such as SINOPEC, CNPC, YPC, and Hengli Group. These are some of the most trusted names in the industry, providing top-tier polypropylene and polyethylene pellets that meet international standards.
We use only virgin (new) plastic pellets for our bags, ensuring that the final products are free from contaminants and defects commonly associated with recycled materials. This is particularly important when creating Printed BOPP Woven Bags, as the quality of the material impacts not just the strength and durability but also the print quality, ensuring vibrant and long-lasting colors.
Batch Inspection and Material Testing
Once the raw materials arrive at our facility, they undergo rigorous quality control checks. Each batch of polypropylene and polyethylene pellets is tested according to international standards. This includes tests for:
- Melt Flow Index (MFI): Ensures that the polymer flows at the right rate during processing, contributing to the consistency and quality of the bag.
- Tensile Strength: Measures the material’s ability to withstand pressure and load, which is crucial for Printed PP Woven Bags that are designed to hold heavy items.
- Elongation at Break: This test measures the material’s ability to stretch before breaking, contributing to the strength and flexibility of the bag.
- Color Consistency: A key test for Printed BOPP Woven Bags to ensure that the final print appears vibrant and consistent across all bags.
- UV Resistance: This test ensures that the bags are suitable for outdoor use and can withstand prolonged exposure to sunlight without degradation.
We also conduct ongoing checks throughout the production process to guarantee that the bags produced meet the stringent quality standards set by both the industry and our clients. These checks include visual inspections and mechanical testing of the bags to ensure their strength, functionality, and appearance.
The Importance of Printed BOPP Woven Bags
Printed BOPP Woven Bags are not just a packaging solution; they serve as a marketing tool. Their ability to be custom-printed with logos, designs, and other branding materials makes them an ideal choice for companies looking to stand out in a competitive market. When it comes to industries such as food, chemicals, and agriculture, these bags offer a functional solution that also enhances brand visibility.
One of the main reasons companies opt for Printed BOPP Woven Sacks is their versatility. These bags can be tailored to meet specific needs such as moisture resistance, UV protection, and custom sizing. The use of BOPP (Biaxially Oriented Polypropylene) film on the woven PP fabric creates a high-quality surface for printing. The result is a bag that combines the strength of woven polypropylene with the aesthetic appeal of high-definition printing. This makes them highly attractive for businesses that require both functionality and a professional appearance.
Printed PP Woven Bags for Various Applications
Our Printed PP Woven Bags are highly versatile and used across multiple industries. Whether for agricultural products, chemicals, or food grains, these bags provide the durability and performance required to meet the unique demands of each sector. Below are some key applications of Printed PP Woven Bags:
- Agricultural Products: These bags are commonly used to package products like grains, rice, fertilizers, and seeds. Their strong construction and ability to hold large quantities make them a perfect solution for this sector.
- Chemicals: The robust nature of Printed BOPP Woven Sacks makes them ideal for packaging chemicals. The moisture and UV resistance help protect the contents from the elements during storage and transportation.
- Food Grains: For the food industry, these bags offer the right combination of strength, moisture resistance, and ease of handling.
- Construction Materials: The bags are used to pack construction materials such as sand, cement, and aggregate, where strength and durability are paramount.
Quality Control in the Printing Process
While raw material quality control is essential, ensuring that the printing process itself adheres to strict standards is equally important. At VidePak, we employ advanced printing technology, including flexographic and gravure printing, to ensure that each Printed BOPP Woven Bag not only meets functional standards but also delivers high-quality prints. This is crucial for our clients, especially those in retail and consumer-facing industries, where the appearance of packaging is key to branding.
We offer custom printing with up to six colors, allowing businesses to incorporate complex designs, logos, and text into their packaging. The printing process is carried out using eco-friendly inks to minimize environmental impact while ensuring long-lasting results that won’t fade or smudge easily. This level of customization and quality makes Printed BOPP Woven Bags ideal for branding and marketing purposes.
Partnering with Leading Raw Material Suppliers
Our partnerships with leading suppliers like SINOPEC, CNPC, YPC, and Hengli Group are instrumental in ensuring that the raw materials used in production meet the highest quality standards. These suppliers provide state-of-the-art polypropylene and polyethylene materials that form the foundation for the bags we produce. With these materials, we can produce bags that meet the strictest standards of strength, durability, and environmental safety.
Our continuous focus on quality control, from raw material sourcing to the final product inspection, guarantees that our customers receive Printed PP Woven Bags that are durable, reliable, and cost-effective.
For further details on our Printed BOPP Woven Bags, please visit here. If you’re looking for high-quality Printed PP Bags, learn more by visiting this page.