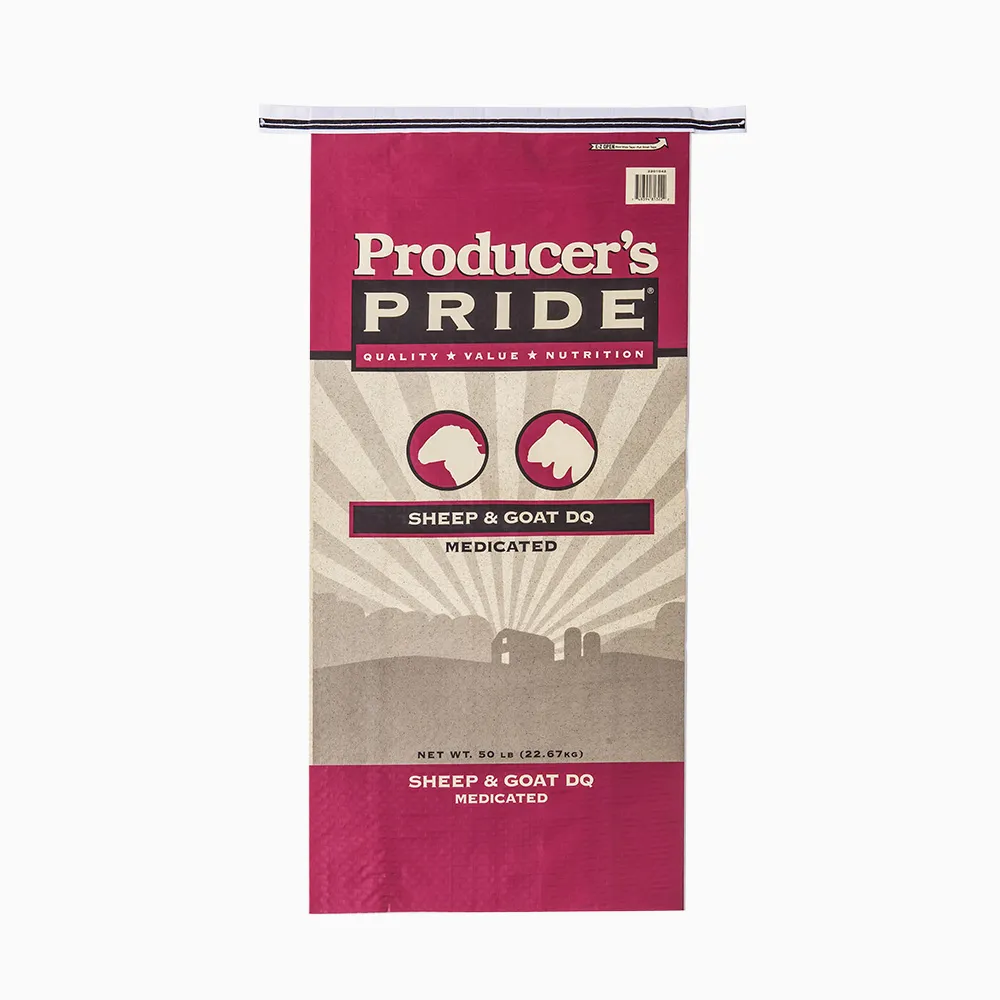
In today’s packaging industry, Custom Printed Woven Bags have gained significant popularity. These bags, made from polypropylene (PP) or BOPP (Biaxially Oriented Polypropylene), are known for their durability, flexibility, and customization options. When it comes to branding, Printed Woven Bags allow businesses to showcase their logos, designs, and marketing messages with vivid, multi-color prints. This post will dive into two main topics related to these products: the various printed woven bag techniques and their health and safety evaluations.
At the start of the 21st century, the demand for Custom Printed Woven Sacks has risen considerably due to their ability to meet packaging needs in industries ranging from agriculture to construction. Whether it’s for transporting agricultural products, foodstuffs, or even chemicals, the design possibilities for Printed PP Bags and Printed BOPP Woven Bags are vast. These bags can be customized to suit the client’s branding needs and the specific requirements of the product being packaged. For more details on these products, check out our article on Custom Printed Woven Bags and Printed Woven Bags.
Types of Printing Techniques for Custom Printed Woven Bags
When choosing Custom Printed Woven Bags, companies can select from various printing methods, each with unique advantages depending on the materials, the design complexity, and the intended use of the bags. Below are some of the most commonly used printing techniques:
1. Flexographic Printing
Flexographic printing is one of the most common methods for printing on woven bags. It uses flexible plates to transfer ink onto the woven material, which is ideal for printing on uneven surfaces like the texture of woven fabric. This method is cost-effective for large orders and provides vibrant, durable prints. It is commonly used for Printed PP Bags and Printed BOPP Woven Bags, particularly when companies need to print multi-color designs.
2. Gravure Printing
Gravure printing, also known as rotogravure printing, is highly suitable for high-quality printing with very fine details. It uses engraved copper cylinders to transfer ink to the woven material. This method is often preferred for complex designs, fine lines, and high-resolution images. However, it is more expensive compared to flexographic printing and is typically used for larger production runs where high-end quality is essential.
3. Screen Printing
Screen printing involves pressing ink through a mesh screen that holds the stencil of the design. This technique is cost-effective for simple, large-scale designs and is often used when high volumes of one color print are required. Though this method is less flexible than flexographic or gravure printing, it provides long-lasting, vibrant prints that withstand wear and tear.
4. Digital Printing
Digital printing has become more popular in recent years due to its flexibility and ability to print high-resolution, multi-colored designs without the need for printing plates. This method uses inkjet or laser technology to directly apply the ink to the woven fabric, making it ideal for short runs, prototypes, or custom designs. However, digital prints tend to be less durable than other types of printing, making them better suited for products that don’t face heavy wear.
5. Heat Transfer Printing
Heat transfer printing is often used for Custom Printed Woven Sacks when a detailed design or logo is needed. A design is first printed on a transfer paper, which is then applied to the woven material using heat and pressure. This method offers high-quality designs but is most often used for smaller batches.
Each printing technique has its own pros and cons, but the most suitable method for any given project depends on factors like order size, design complexity, and intended use of the Printed Woven Bags.
Printing Comparison Table
Printing Technique | Suitable for | Cost | Durability | Design Complexity |
---|---|---|---|---|
Flexographic Printing | Large runs with multi-color designs | Low to Medium | High | Medium |
Gravure Printing | High-quality, intricate designs | High | Very High | Very High |
Screen Printing | Large-scale, simple designs | Low | High | Low |
Digital Printing | Short runs, custom designs | Medium | Medium | High |
Heat Transfer Printing | Detailed logos, smaller batches | Medium | High | High |
Health and Safety Considerations of Custom Printed Woven Bags
When assessing the health and safety performance of Printed Woven Bags, it’s crucial to consider the materials used in the production process, the safety standards followed during manufacturing, and how the bags are used. The following are some aspects to keep in mind:
1. Material Safety
The first concern when evaluating the safety of Custom Printed Woven Bags is the type of material used in their construction. Most woven bags are made from polypropylene (PP) or BOPP. These materials are considered relatively safe for packaging, but their safety depends largely on the manufacturing process.
- Polypropylene (PP): PP is non-toxic, lightweight, and durable. It is resistant to chemical damage, making it a suitable choice for many packaging applications. However, low-quality PP bags or those produced with hazardous additives may pose health risks, such as the leaching of chemicals.
- BOPP (Biaxially Oriented Polypropylene): Printed BOPP Woven Bags often feature enhanced graphics and durability. BOPP is safe for food packaging but needs to be tested to ensure it does not contain harmful chemicals such as BPA (bisphenol A), which may be used in certain plastics.
To ensure safety, it’s essential to source Custom Printed Woven Bags from manufacturers who use high-quality raw materials and meet international safety standards.
2. Regulatory Compliance
For Printed PP Bags used in food packaging, compliance with health regulations is crucial. In many countries, packaging used for food products must meet stringent regulations regarding chemical migration, safety, and hygiene. These regulations ensure that there are no harmful interactions between the bag and the contents it holds. Bags that meet these standards are considered safe for storing consumables and are often certified by health organizations.
It’s important to check whether the Printed Woven Bags comply with regulatory standards like those from the FDA (Food and Drug Administration) or the EFSA (European Food Safety Authority).
3. Environmental Safety
While not directly related to human health, the environmental impact of Custom Printed Woven Bags is also an important factor in overall safety. Bags that are not properly disposed of can contribute to environmental degradation, leading to pollution and harm to wildlife. Many manufacturers are now prioritizing eco-friendly options, such as recyclable or biodegradable bags, to reduce their environmental footprint. When considering the safety of these bags, it’s essential to look at their recyclability and disposal impact.
4. Safety During Use
For industries like agriculture and construction, Custom Printed Woven Sacks often have to bear heavy loads. It’s essential to ensure that these bags are manufactured with reinforced stitching and are rated for the appropriate weight capacity. Bags that are not adequately constructed can tear or fail, posing safety risks to workers who may be handling the bags.
Manufacturers of Printed Woven Bags often include load-bearing guidelines on the packaging to ensure that the bags are used safely.
Safety Comparison Table
Safety Aspect | Material Type | Safety Concerns | Regulation |
---|---|---|---|
Material Safety | Polypropylene (PP) | Toxic additives in low-quality bags | FDA/EFSA compliance |
Compliance with Regulations | BOPP | Chemical migration (BPA) | Food safety certifications |
Environmental Impact | PP, BOPP | Non-recyclable waste | Eco-friendly initiatives |
Safety During Use | Woven fabric (PP/BOPP) | Risk of bag failure | Load-bearing standards |
Conclusion
The world of Custom Printed Woven Bags is diverse, with numerous printing options available to suit varying needs across industries. Whether you’re looking to promote your brand with Printed BOPP Woven Bags or ensure safety with Printed PP Bags, there are various methods and considerations to keep in mind. Furthermore, understanding the health and safety implications of these bags, from the materials used to the safety during use, is crucial in maintaining product integrity and safeguarding human health. When sourcing these products, always ensure that manufacturers adhere to quality and regulatory standards to guarantee the best possible results.