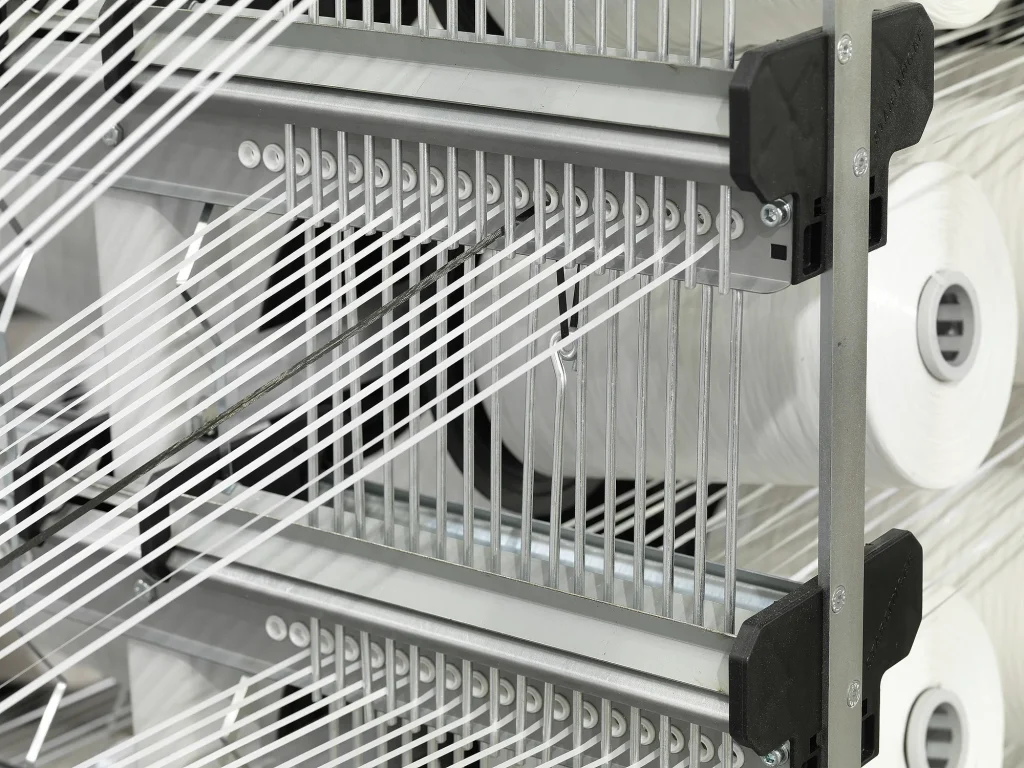
The primary answer this article provides is: Paper valve woven bags require rigorous raw material testing—PP pellets must meet melt flow index (MFI) standards of 2–12 g/10 min, density ranges of 0.905–0.925 g/cm³, and tensile strengths exceeding 35 MPa, while PE liners demand dart impact resistance >400 g/mil. VidePak’s ISO 9001-certified labs validate 25+ parameters using ASTM/ISO methods, ensuring compliance with EU REACH, US FDA, and GB/T standards for chemical-grade packaging solutions.
Introduction
In the $120 billion global packaging industry, substandard polymer materials cause 17% of product failures—a risk mitigated only through systematic raw material testing. Paper valve woven bags, critical for cement, fertilizers, and industrial powders, demand precision-engineered polypropylene (PP) and polyethylene (PE) to achieve structural integrity and regulatory compliance. This guide explores how advanced material testing protocols—from MFI analysis to thermal stability assessments—underpin high-performance bag production, aligning with VidePak’s 30-year commitment to quality assurance.
Founded in 2008, VidePak operates 16 extrusion lines and 100+ Starlinger circular looms to produce 500 million paper valve bags annually. Our in-house labs, equipped with Instron tensile testers and DSC analyzers, validate every batch of PP/PE against 12 international standards, serving clients like Cargill and BASF across 60+ countries.
PP Granule Testing: The Foundation of Woven Bag Durability
1. Physical Property Validation
- Melt Flow Index (MFI): Measured via ASTM D1238 at 230°C/2.16 kg, ideal PP ranges from 2–12 g/10 min. Lower MFI (<5) enhances tensile strength for heavy-duty bags (e.g., 50 kg cement), while higher MFI (>8) suits lightweight applications.
- Density: ASTM D792 gravimetric methods ensure PP density stays within 0.905–0.925 g/cm³. Deviations >1% indicate copolymer contamination.
2. Mechanical Performance Benchmarks
- Tensile Strength & Elongation: ASTM D638 tests yield warp/weft strengths >35 MPa and elongation at break >500%—critical for resisting dynamic loads during filling.
- Impact Resistance: Notched Izod tests (ASTM D256) require >5 kJ/m² to prevent brittleness in cold climates.
Case Study: VidePak rejected a 20-ton PP shipment with 28 MPa tensile strength (vs. required 35 MPa), preventing $500k in potential customer claims.
PE Liner Testing: Beyond Basic Metrics
1. Film-Specific Assessments
- Dart Impact Strength: ASTM D1709 Method A mandates >400 g/mil for 80 µm PE liners handling abrasive powders like calcium carbonate.
- Puncture Resistance: FTMS 101C 2065 tests require >15 N/mm to withstand titanium dioxide’s sharp edges.
2. Thermal Stability Protocols
- Heat Distortion Temperature (HDT): ISO 75-1 tests ensure PE liners withstand 85°C±2°C without deformation during hot-fill processes.
- Crystallization Analysis: DSC scans verify PE’s melting peak at 120–135°C, with crystallinity >60% for optimal sealability.
Quality Control Parameters for PP & PE
Parameter | PP Standards | PE Standards | Test Method |
---|---|---|---|
MFI | 2–12 g/10 min | 0.2–4 g/10 min | ASTM D1238 |
Density | 0.905–0.925 g/cm³ | 0.917–0.941 g/cm³ | ASTM D792 |
Tensile Strength | >35 MPa | >20 MPa | ASTM D638 |
Impact Strength | >5 kJ/m² | >400 g/mil | ASTM D256/D1709 |
HDT | >100°C (0.45 MPa) | >85°C | ISO 75-1 |
FAQs: Navigating Material Procurement
Q1: Why does MFI variance matter in PP selection?
A ±1 g/10 min MFI shift alters extrusion rates by 15%, causing uneven weaving. VidePak’s tolerance: ±0.3 g/10 min.
Q2: How does PE crystallinity affect liner performance?
Higher crystallinity (>65%) improves stiffness but reduces tear resistance. Our 60–65% balance ensures both stackability and puncture resistance.
Q3: Are recycled PP/PE granules viable?
Yes, if MFI remains stable (±10%) and contaminants <200 ppm. VidePak’s 30% post-industrial recycled PP meets FDA 21 CFR 177.1520.
Q4: What certifications validate compliance?
EU REACH SVHC <0.1%, US FDA CFR 177.1520, China GB/T 21661-2020. Our PP/PE granules are certified by SGS and TÜV.
VidePak’s Multi-Stage Testing Workflow
- Incoming Inspection: XRF analyzers detect heavy metals (Pb <50 ppm, Cd <10 ppm).
- Process Validation: Online FTIR monitors polymer degradation during extrusion.
- Final Product Testing: Bag seam strength >250 N/5cm (EN 15507).
Global Regulatory Alignment
Region | PP/PE Standard | Key Requirement | VidePak Compliance |
---|---|---|---|
EU | EN 13432:2000 | Oxo-biodegradability | TÜV OK Compost INDUSTRIAL |
USA | ASTM D6400-21 | Marine biodegradation | BPI Certification |
China | GB/T 20197-2022 | Recycled content labeling | 30% PCR PP verified |
Japan | JIS Z 0238:2020 | Phthalate-free (<0.1%) | SGS Tested |
References
- VidePak Corporate Profile: https://www.pp-wovenbags.com/
- Testing Standards: ASTM D1238, ISO 75-1, GB/T 20197-2022.
- Industry Reports: Polymer Testing in Packaging (Smithers, 2024).
For inquiries, contact info@pp-wovenbags.com.
External Resources:
- Explore advanced PP weaving technologies: PP Woven Bags: Material Excellence and Manufacturing Processes.
- Learn about sustainable valve bag solutions: Paper Valve Woven Bags: Pioneering Sustainable Packaging in China.
Authored by VidePak’s Material Science Team | Updated: March 2025