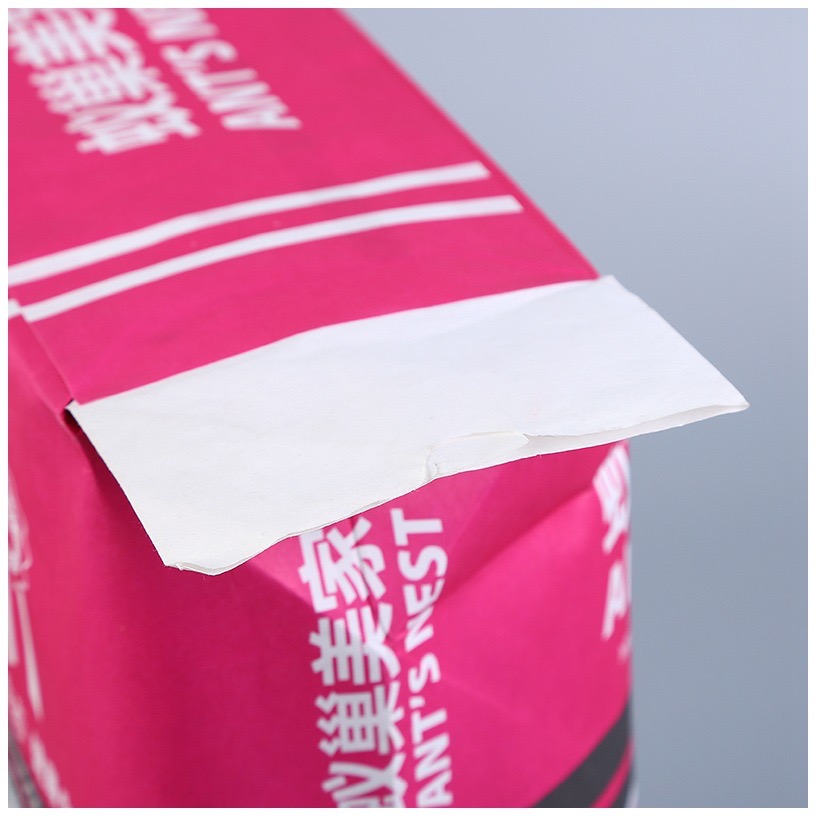
In the world of packaging, Valve Bags have gained prominence for their versatility and effectiveness, especially in industrial applications. These bags, also known as Valve sacks, Valve Woven Bags, or Valve PP Bags, offer efficient solutions for packaging granular materials, powders, and other substances requiring durable, leak-proof containment. This article will explore the different types of valve openings, discuss innovations in raw materials developed in collaboration with major chemical enterprises, and provide an overview of the essential additives that enhance these bags’ performance.
Types of Valve Openings in Valve Bags
Valve bags are primarily designed for easy filling and secure closure. The valve type is a critical design element, determining filling efficiency, sealing effectiveness, and end-use suitability. Common valve types in the industry include:
Valve Type | Characteristics | Use Case |
---|---|---|
Internal Valve | Positioned within the bag, invisible from the outside. Protects against contaminants, ideal for chemical and food products. | Cement, Chemicals, Grains |
External Valve | Located outside the bag, enabling quick filling without special equipment. Cost-effective but less resistant to contaminants. | Bulk Powders, Sand |
Self-Sealing Valve | Closes automatically when the bag is full, minimizing the risk of spills. Suitable for high-speed filling. | Construction Materials, Fine Powders |
Heat-Sealed Valve | Designed for a permanent seal via heat application, preventing leaks and spills. Often used in food and chemical packaging. | Pharmaceuticals, Food Products |
Valve bags, particularly those with self-sealing and heat-sealed valves, streamline packaging processes and enhance product protection. With the growing demand for such high-performance bags, VidePak has consistently leveraged innovation to improve the material quality and structural reliability of these bags. You can learn more about VidePak’s product quality initiatives through this link on multiwall laminated woven bags.
Collaborative Innovations: Modified Raw Materials for Enhanced Valve Bags
To meet the increasing demand for durable and flexible valve bags, VidePak has partnered with leading chemical companies to develop a modified raw material that combines strength with remarkable elasticity. This new material brings enhanced durability and flexibility to Valve PP Bags, making them an ideal solution for packaging heavy-duty industrial products without risking tears or punctures.
These collaborative innovations in raw material focus on creating a polymer blend that offers:
- Enhanced Elasticity: Improved stretchability allows the bags to withstand heavy loads without breaking, reducing transportation losses.
- Increased Tear Resistance: The modified polymer structure resists abrasions and punctures, ensuring safer handling and prolonged usage.
- Extended Shelf Life: By fortifying the material with stabilizers, the bags are less prone to degradation from environmental exposure, particularly UV light.
This development exemplifies VidePak’s commitment to advancing product quality, as detailed in their exploration of high-strength packaging solutions like Valve Woven Bags here.
Key Additives to Ensure Valve Bags’ Performance and Durability
To optimize the functionality and longevity of valve bags, various additives are incorporated into the raw material during production. Each additive plays a specific role, from enhancing strength to providing resistance against environmental factors. Below is a detailed look at some of the essential additives used in manufacturing Valve sacks.
Additive Type | Purpose | Benefits | Typical Dosage (in % of total material) |
---|---|---|---|
UV Stabilizers | Protects bags from sunlight degradation | Prevents brittleness and color fading | 0.1% – 0.5% |
Antioxidants | Prevents oxidation of the polymer during processing and usage | Increases material durability | 0.2% – 0.4% |
Impact Modifiers | Enhances bag flexibility and resistance to tearing | Increases resilience to punctures and mechanical stress | 1% – 3% |
Color Pigments | Adds color for branding and product differentiation | Enhances aesthetic appeal and visibility | 0.5% – 1% |
Anti-Slip Agents | Increases friction on the bag surface for easier stacking and handling | Improves stability in storage and transport | 0.2% – 0.6% |
Anti-Static Agents | Reduces static electricity buildup | Prevents dust and particle accumulation | 0.1% – 0.3% |
1. UV Stabilizers
- UV stabilizers are essential for protecting polypropylene (PP) bags from sunlight, which can cause the material to weaken and become brittle. By incorporating UV stabilizers, valve bags maintain their structural integrity over extended periods, even when exposed to outdoor environments.
2. Antioxidants
- Antioxidants are added to prevent oxidative degradation, especially during high-temperature processing. They help maintain the bag’s strength and resilience, ensuring it can handle the stresses of filling, sealing, and transportation without compromise.
3. Impact Modifiers
- Impact modifiers enhance the flexibility and toughness of valve bags, particularly under impact. This feature is essential for applications requiring robust packaging solutions, such as chemicals, construction materials, and bulk food products.
4. Color Pigments
- Color pigments are commonly added to create distinctive colors, aiding in product differentiation and branding. Valve bags with specific colors also enable easy identification during storage, handling, and distribution, improving operational efficiency.
5. Anti-Slip Agents
- The smooth surface of PP bags can sometimes lead to stacking issues during transport or storage. Anti-slip agents increase surface friction, helping to keep stacked bags stable, which minimizes damage and maximizes space utilization.
6. Anti-Static Agents
- Anti-static agents prevent static electricity buildup, particularly important when packaging fine powders and granules that can cling to bag surfaces. Reducing static not only keeps the product intact but also minimizes contamination and safety hazards.
The Role of VidePak in Advancing Valve Bag Manufacturing
As a premier Valve bags manufacturer, VidePak has committed to quality, customization, and innovative technology integration. The production facilities at VidePak use state-of-the-art equipment from globally recognized suppliers like Starlinger, ensuring each bag adheres to the highest standards of durability and safety. Our rigorous testing protocols and continuous research in materials science place us at the forefront of industrial packaging.
The modified materials and strategic additives discussed are just a few examples of our commitment to excellence in manufacturing Valve Woven Bags. By partnering with chemical experts and investing in next-gen equipment, we continue to provide valve bags that meet diverse industry needs—from heavy-duty construction materials to sensitive food-grade packaging. Explore more about VidePak’s innovations in Valve PP Bags by visiting this link on block-bottom valve bags.
Conclusion
The continuous advancement in valve bag manufacturing highlights the importance of collaborative innovation and meticulous attention to material properties. As industries seek stronger, more durable, and flexible packaging solutions, VidePak’s Valve Bags provide the right combination of advanced materials, diverse valve types, and essential additives. Whether for heavy industrial products or delicate food items, our bags are designed to withstand rigorous handling and environmental stress, making them a reliable choice for businesses globally.