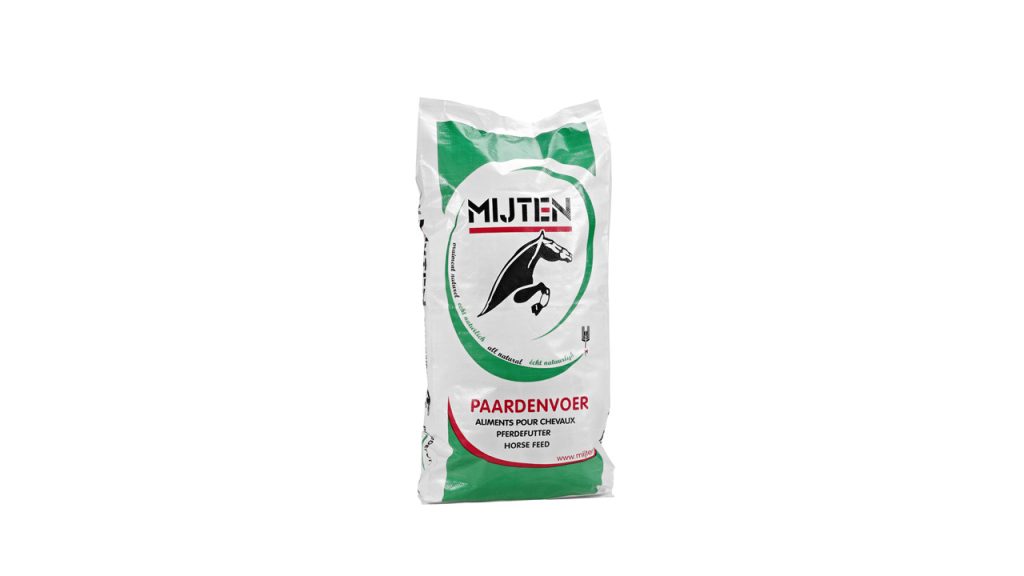
主要答案:对于高负载、严苛环境和多国出口要求,选用高熔体强度与优异机械性能并符合食品安全及环境标准的高韧性共聚聚丙烯(PP)牌号,搭配UV稳定剂、抗氧化剂等功能性添加剂,是制造Open Mouth PP Bags的最优解决方案。
In the global packaging landscape, Open Mouth Bags made from polypropylene (PP) have rapidly become indispensable due to their robustness, cost-effectiveness, and versatility. Industry reports, such as a 2023 market analysis by MarketsandMarkets, indicate that the PP woven bags market is expected to grow at a CAGR of around 5.2% through 2026, propelled by rising demand in the agricultural, construction, and chemical sectors. This article delves into how the right PP grade, combined with targeted additives, aligns with major international standards (ASTM, JIS, EN, GB, and BS) to ensure Open Mouth sacks and Sewn Open Mouth Bags meet stringent performance, safety, and sustainability requirements.
1. Introduction to Open Mouth PP Bags
Open Mouth Bags (also referred to as Open Mouth sacks) offer a simple yet highly efficient design, where one end of the bag remains open for easy filling. Demand has surged in sectors such as grains, fertilizers, animal feed, and construction materials. According to the World Packaging Organisation (WPO), the adaptability of Open Mouth Bags makes them a global packaging staple, especially for bulk shipping and storage. Moreover, as consumer preferences shift toward eco-friendly solutions, PP’s recyclability further boosts its appeal.
Example
- Cement Packaging in Europe: A German cement producer switched to Open Mouth Bags made from a high-tenacity PP grade, aligning with EN standards. This transition improved packaging durability and reduced product spillage during transit.
2. Overview of Key Global Standards
Manufacturing standards vary by region, and compliance is pivotal to ensure product safety and global market entry. Below is a brief overview:
- ASTM (United States): Focuses on tensile strength, impact resistance, and environmental performance.
- JIS (Japan): Stresses dimensional stability and uniformity, especially for automated filling lines.
- EN (Europe): Emphasizes recyclability and food safety.
- GB (China): Addresses mechanical performance and hygiene norms for food-related applications.
- BS (United Kingdom): Aligns closely with EN but may include specific labeling and safety guidelines.
Example
- Animal Feed Packaging in Japan: By choosing a PP grade with low shrinkage, a Japanese livestock feed supplier met JIS dimensional requirements, minimized bag deformation, and safeguarded the feed from contamination.
3. Selecting the Appropriate PP Grade
Picking the right PP grade for Open Mouth sacks, Sewn Open Mouth Bags, or Block Bottom Bags can significantly impact your packaging’s durability, shelf life, and compliance with regulations. Recent data from the Flexible Packaging Association (FPA) underscores the growing preference for high-performance resins that balance strength, cost, and processability.
- Mechanical Strength
- High-tenacity PP grades deliver better tear resistance and load capacity.
- Standard grades may be cost-effective but can underperform in demanding conditions.
- Melt Flow Index (MFI)
- Higher MFI grades streamline manufacturing, favoring high-volume production.
- Lower MFI grades provide superior mechanical strength but may be slower to process.
- Thermal Stability
- PP grades with extended heat resistance cater to hot-fill applications.
- For ASTM compliance, especially for materials like hot asphalt or certain chemicals, specialized thermal-stable PP is essential.
- Food-Grade Compliance
- FDA-approved PP (U.S.) or EFSA-approved PP (EU) is mandatory for direct food contact.
- In certain Southeast Asian markets, local regulations increasingly mirror these global benchmarks.
- Environmental Considerations
- Recycled PP usage is on the rise, encouraged by EU sustainability directives.
- However, mechanical properties and safety checks (like GB for China) must still be met.
Table 1: Common PP Grades and Their Properties
PP Grade | MFI Range (g/10min) | Key Properties | Typical Applications |
---|---|---|---|
Homopolymer PP | 1–3 | High rigidity, fair clarity | Food packaging, general Open Mouth sacks |
Copolymer PP | 3–5 | Enhanced impact resistance | Block Bottom Bags, heavier-duty industrial packaging |
Random PP | 5–10 | Good transparency, soft finish | Film-laminated Open Mouth Bags for visual appeal |
High-tenacity PP | <1 – 3 | Superior tensile strength | Sewn Open Mouth Bags for extreme load-bearing needs |
Example
- Rice Packaging in China: To meet GB standards, a premium rice brand adopted a high-tenacity copolymer PP. This choice ensured robust protection and minimized tearing issues during long-distance shipping.
4. Fillers and Additives: Enhancing Performance
Adding specialized fillers and additives can dramatically improve bag performance. Experts at the American Society of Plastics Engineers highlight that the correct additive blend optimizes reliability in challenging environments.
- UV Stabilizers:
- Essential for prolonged outdoor exposure.
- Protects bag coloration and structural integrity against UV-induced degradation.
- Anti-oxidants:
- Safeguard polymer chains from breaking down at high temperatures or over lengthy storage times.
- Prevent brittleness and tearing.
- Anti-slip Agents:
- Increase friction between stacked bags, reducing slippage in warehouses or on pallets.
- Crucial for high-volume storage and transport lines.
- Anti-static Agents:
- Minimize static buildup, vital for chemical or fine-powder contexts.
- Enhance safety and ease of handling.
- Fillers (Calcium Carbonate, etc.):
- Lower cost, can improve printability and stiffness.
- Must be carefully calibrated to avoid undermining tensile strength.
Example
- Fertilizer Packaging in Southeast Asia: A local fertilizer firm observed bag fading due to intense sunlight. Incorporating state-of-the-art UV stabilizers resolved this issue, boosting customer satisfaction and reducing rejected product returns.
5. Product Applications and Insights
Block Bottom Bags
Block Bottom Bags feature a square or rectangular base that stands upright, which is ideal for automated filling lines and retail display. Recent innovations in lamination technology allow for sharper print resolution, enhancing brand recognition.
Example: A U.S. pet food company successfully transitioned to Block Bottom Bags with copolymer PP. This switch improved pallet stability, reduced tearing incidents, and boosted overall consumer perception.
6. Conversation Snippet
Topic: Selecting the Right UV Stabilizer
Question: “We ship our Open Mouth sacks to regions with extreme sunlight. Which additive is critical for long-term durability?”
Answer: “A HALS (Hindered Amine Light Stabilizers) based UV stabilizer is recommended. It delays color fade and polymer degradation even under prolonged, intense UV exposure.”
7. Two External Links
For those looking to explore leading innovations and market trends in Open Mouth Bags, discover more about cutting-edge features and branding strategies here:
Open Mouth Bags
For heavy-duty packaging that requires robust sewn closures, consult this resource on
Sewn Open Mouth Bags
to understand how precise stitching and material quality control can drastically enhance durability.
8. FAQs
- Q: What determines the load capacity of Open Mouth sacks?
A: The PP grade (especially tensile strength) and the bag’s weave density are primary factors. Opt for high-tenacity PP if you’re handling heavier or abrasive materials. - Q: Are Open Mouth Bags eco-friendly?
A: Polypropylene is recyclable, and newer processes allow for partial or full recycled content. Compliance with local recycling initiatives helps reduce environmental impact. - Q: How does Block Bottom Bags design reduce shipping costs?
A: The block-bottom structure allows denser stacking on pallets, maximizing space usage. Reduced bag deformation can also lower product waste and spillage costs. - Q: When are Sewn Open Mouth Bags preferable?
A: For products prone to generating dust or where closure integrity is paramount, stitched seams can outperform heat-sealed edges in preventing leaks. - Q: Is special printing needed for PP Open Mouth Bags?
A: Flexographic and gravure printing are commonly used. A laminated or BOPP surface can accommodate high-resolution graphics, benefiting retail-facing products.
9. Detailed Market Analysis
Regional Demand
- North America: High standards under ASTM and strong focus on impact resistance lead many industrial manufacturers to adopt copolymer PP blends with advanced additives.
- Asia-Pacific: Rapid growth in agriculture and construction fuels demand, with China’s GB standards emphasizing quality consistency.
- Europe: Sustainability directives spur interest in partially or fully recycled PP. Innovation in additive technologies meets EN and BS frameworks for recyclability.
- Latin America: UV stabilization is paramount, given the high solar radiation in many regions. Crops like coffee and cocoa require durable yet breathable packaging solutions.
Growth Opportunities
- Advanced Printing: Eye-catching, high-definition prints make Open Mouth Bags appealing for retail. Digital and hybrid printing presses are on the rise.
- Additive Innovations: Emerging anti-microbial and oxygen-barrier additives extend shelf life, crucial for food-grade applications.
- Automated Filling Lines: As factories modernize, Block Bottom Bags and well-engineered Sewn Open Mouth Bags facilitate faster throughput and reduce downtime.
Example
- Chemical Packaging in the Middle East: Dealing with extreme heat and UV exposure, a chemical distributor chose a UV-stabilized, high-tenacity PP grade. They met BS requirements for exports to the UK, streamlined shipping logistics, and significantly cut bag-failure rates.
10. Conclusion
The evolution of Open Mouth PP Bags—including Open Mouth sacks, Sewn Open Mouth Bags, and Block Bottom Bags—continues unabated as global industries pivot toward stronger, safer, and more sustainable packaging. Selecting a PP grade with high melt strength and robust mechanical properties, combined with judicious use of additives like UV stabilizers and anti-oxidants, is paramount. Aligning with international standards (ASTM, JIS, EN, GB, BS) ensures these bags deliver reliable performance while adhering to growing environmental and food safety mandates. As market demand surges in sectors from agriculture to construction, adopting innovative designs and materials can future-proof your packaging strategy and cement your brand’s reputation for quality and trustworthiness.