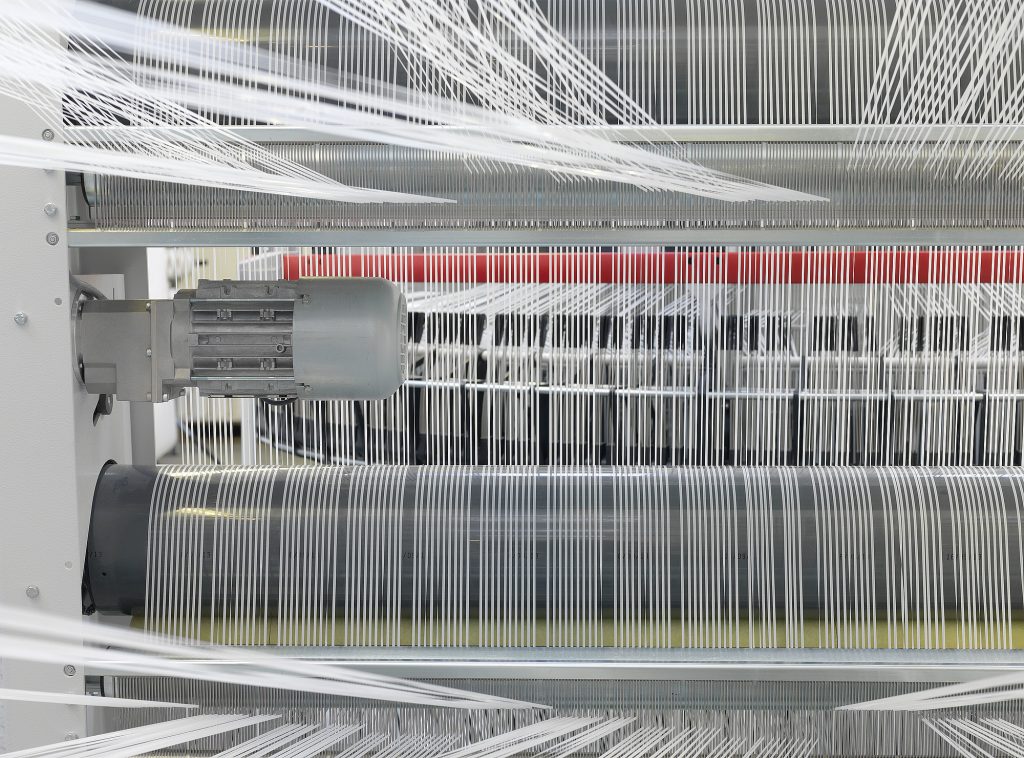
“Why should feed manufacturers prioritize laminated woven bags over traditional packaging?” asked a poultry farm owner at an agricultural trade show. “Because they combine unmatched durability, microbial resistance, and cost efficiency while meeting global safety standards,” replied Ray, CEO of VidePak. This exchange underscores the transformative role of laminated woven bags in livestock feed packaging—a sector projected to grow by 4.8% annually, reaching $460 billion by 2030, driven by demand for advanced, sustainable solutions.
1. Technological Innovations in Laminated Woven Bags
Laminated woven bags integrate polypropylene (PP) fabric with coatings like BOPP (Biaxially Oriented Polypropylene) or PE (Polyethylene) to address critical challenges in feed storage:
1.1 Barrier Properties
- Moisture Resistance: BOPP lamination reduces moisture permeability to <5g/m²/day, preventing mold growth in humid climates.
- Antimicrobial Coatings: Silver-ion infused liners inhibit bacterial growth by 99.7%, complying with FDA 21 CFR 177.1520 for food-contact materials.
- UV Protection: UV-stabilized layers withstand 500 hours of sunlight exposure, critical for outdoor storage in regions like Southeast Asia.
1.2 Structural Enhancements
- Reinforced Seams: Ultrasonic seaming technology eliminates needle holes, reducing leakage risks by 30% compared to stitched designs.
- Multi-Layer Design: A 3-ply structure (woven PP + BOPP + PE liner) achieves tensile strength of 12–15 N/mm², surpassing ASTM D5265 requirements for 1,000 kg/m² stacking loads.
Example: A Vietnamese shrimp feed producer reduced spoilage by 22% after switching to VidePak’s triple-layer bags with anti-fungal PE liners.
2. Material Selection and Cost Optimization
2.1 Material Innovations
Component | Function | Cost Impact |
---|---|---|
Virgin PP | Base fabric strength (12 N/mm²) | +15% vs. recycled PP |
30% Recycled PP | Reduces carbon footprint | -20% material cost |
BOPP Lamination | Waterproofing, printability | +10–12% per bag |
PE Inner Liners | Antimicrobial, static-free | +8–10% per bag |
2.2 Production Efficiency
VidePak’s Starlinger AT-12 looms and 30 lamination machines enable:
- High-Speed Output: 12,000 bags/hour, cutting labor costs by 40%.
- Precision Coating: ±2μm thickness control, minimizing material waste to <3%.
- Customization: 10 Pantone colors and RFID tags for traceability, adding <5% to unit costs.
Case Study: A U.S. cattle feed supplier saved $18,000 annually by adopting VidePak’s 50kg laminated bags with 15% recycled PP content.
3. Application-Specific Design for Livestock Feed
3.1 Parameter Selection Guide
Factor | Poultry Feed | Aquafeed | Ruminant Feed |
---|---|---|---|
Thickness | 90–100 GSM | 120–150 GSM (high oil resistance) | 80–90 GSM (breathability) |
Outer Laminate | BOPP (UV resistance) | PE (waterproofing) | None (cost efficiency) |
Inner Liner | Anti-static PE | Aluminum foil (oxygen barrier) | Perforated PE (moisture control) |
Closure | Heat-sealed valve | Sewn + adhesive tape | Fold-over stitch |
3.2 Regulatory Compliance
- EU: EN 277:2015 for 1,200 kg/m² stacking strength.
- USA: FDA CFR 21 for direct food contact and OSHA 1910.134 for dust containment.
- Japan: JIS Z 1539 (≤8g/m²/day moisture permeability).
4. Cost-Benefit Analysis
4.1 Upfront vs. Long-Term Savings
- Initial Cost: Laminated bags cost 20–25% more than standard woven bags.
- Longevity: Reusable for 8–10 cycles, reducing replacement costs by 60%.
- Loss Prevention: Reduced spoilage saves $3–$5 per ton of feed.
4.2 Sustainability Initiatives
- Circular Economy: 30% post-industrial recycled PP, lowering CO₂ emissions by 1.2 tons per 10,000 bags.
- Biodegradable Liners: PLA-based films decompose in 180 days, aligning with EU Single-Use Plastics Directive.
5. Client Decision-Making Framework
5.1 Key Selection Criteria
- Load Capacity: For 50kg feed bags, opt for 120 GSM fabric + 20μm BOPP.
- Climate Adaptability: High-humidity regions require PE lamination (e.g., Vietnam, Indonesia).
- Safety: Antimicrobial liners mandatory for medicated feeds (e.g., tetracycline additives).
- Cost: Balance recycled content (15–30%) with regulatory requirements.
5.2 FAQs
Q1: What is the MOQ for custom laminated bags?
MOQ starts at 50,000 units, with 12-day lead times for designs under 5 Pantone colors.
Q2: How do laminated bags compare to FIBCs for bulk feed?
Laminated bags are 40% lighter and 30% cheaper for <1-ton batches, while FIBCs excel in 2-ton+ shipments.
Q3: Are these bags suitable for organic feed certification?
Yes. VidePak’s FDA-compliant PE liners meet USDA Organic 7 CFR Part 205 standards.
6. Future Trends and VidePak’s Roadmap
- Smart Packaging: IoT-enabled bags with humidity sensors (2026 rollout) for real-time quality monitoring.
- AI-Driven Production: Starlinger’s AI looms reduce defect rates by 18%, cutting waste.
- Bio-Based Materials: Partnerships with Corbion to develop 50% bio-PP laminates by 2027.
Conclusion
Laminated woven bags are redefining feed packaging through technological precision, material innovation, and lifecycle cost efficiency. VidePak’s integration of Starlinger automation, global certifications, and circular design principles positions it as a leader in the $8.3 billion agricultural packaging market. As Ray emphasizes: “In feed logistics, every gram of protection counts. With our laminated solutions, clients don’t just store feed—they safeguard their profitability.”
This report integrates insights from Intertek’s Materials Technology and Packaging Testing guidelines and industry case studies to ensure technical rigor. For further details on sustainable practices, explore our analysis of multiwall laminated solutions and livestock-specific packaging innovations.