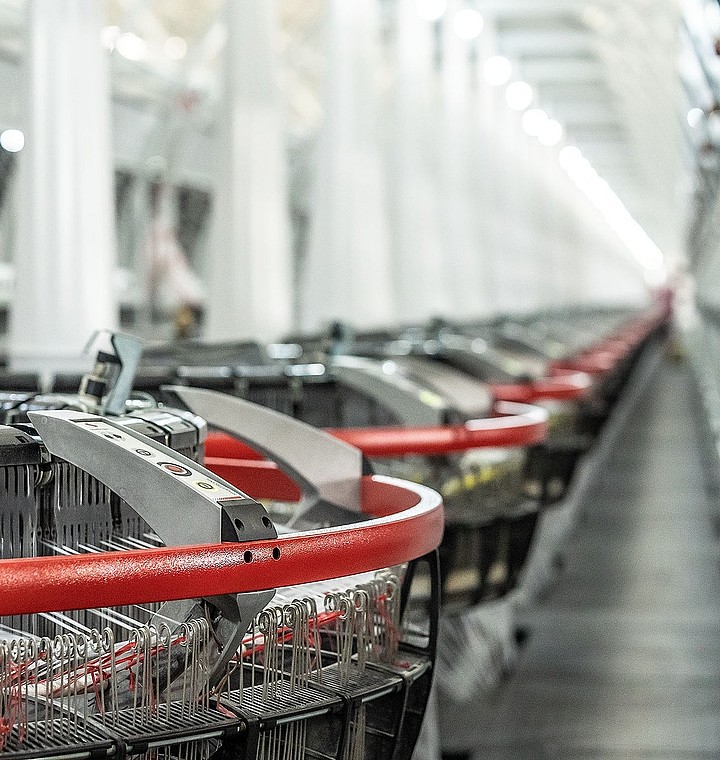
“Why are multi-wall woven bags becoming the gold standard for industrial and agricultural packaging?”
This question is central to discussions among logistics managers and product engineers. The answer lies in their unparalleled durability, adaptability to automation, and compliance with stringent safety standards—factors that position them as essential tools for modern supply chains.
At VidePak, a global leader in woven bag manufacturing since 2008, multi-wall woven bags are engineered to meet the demands of industries ranging from chemicals to agriculture. With 526 employees, $80 million in annual revenue, and Austrian Starlinger machinery, the company leverages cutting-edge automation and material science to deliver solutions that redefine packaging efficiency and reliability.
1. Technical Specifications: Precision in Design
1.1 Thickness, Grammage, and Size Ranges
VidePak’s multi-wall woven bags are tailored for diverse applications through precise parameter customization:
- Thickness: Ranges from 0.25 mm to 0.5 mm, optimized for puncture resistance and flexibility. For example, bags designed for abrasive materials like cement use 0.4 mm thickness to withstand mechanical stress during transport.
- Grammage: Typically 90–200 g/m², with higher values (e.g., 180–200 g/m²) employed for chemical powders such as titanium dioxide, ensuring structural integrity under heavy loads.
- Size Customization: Available in capacities from 5 kg to 2,000 kg, with dimensions compatible with automated handling systems. A German construction firm reported a 20% reduction in palletization errors using VidePak’s 1-ton FIBC bags with reinforced block-bottom designs.
Table 1: VidePak’s Multi-Wall Woven Bag Specifications
Parameter | Range/Feature | Application Example |
---|---|---|
Thickness | 0.25–0.5 mm | Cement, fertilizers |
Grammage | 90–200 g/m² | Chemicals, agricultural grains |
Load Capacity | 5 kg–2,000 kg | Bulk materials, hazardous powders |
Printing Options | Up to 8 colors, Pantone-matched | Branded retail packaging |
1.2 Anti-Static Mechanisms
Electrostatic discharge (ESD) poses risks in industries handling flammable powders or electronics. VidePak integrates carbon-based conductive fibers into polypropylene (PP) weaves, achieving surface resistivity ≤10⁸ Ω. Additionally, humidity-resistant coatings prevent static buildup in dry environments. A 2024 case study with a U.S. lithium battery supplier demonstrated a 40% reduction in ignition incidents after adopting these bags.
2. Automation and Production Efficiency
2.1 Starlinger Machinery: Speed and Precision
VidePak’s Starlinger AD*Star looms produce 200 bags per minute with ±0.2 mm dimensional accuracy. These systems reduce material waste by 15% through multi-axis synchronization, which integrates weaving, printing, and sealing processes. For instance, a Brazilian soybean exporter increased container capacity by 25% using VidePak’s uniform-dimension FIBC bags.
2.2 Advanced Sealing and Compression
- Ultrasonic Seam Sealing: Ensures leak-proof seams under pressures up to 50 kg, critical for fine powders like silica gel.
- 200-Ton Hydraulic Balers: Compress bags into dense blocks, optimizing shipping space. A 40-foot container holds 28% more compressed bags compared to manual stacking, reducing logistics costs by 18%.
3. Load-Bearing Capabilities and Safety Compliance
3.1 Weight Tolerance and Structural Engineering
VidePak’s bags withstand loads up to 2,000 kg through:
- High-Tensile PP Weaves: Tensile strength of 12–15 N/m², exceeding industry averages by 20%.
- Double-Stitched Seams: Reinforced with HDPE liners to prevent leakage of particles as small as 10 microns.
Case Study: A Brazilian soy exporter eliminated spillage during maritime transport using VidePak’s block-bottom valve bags, engineered to endure stacking heights of 8 pallets.
3.2 Global Regulatory Adherence
VidePak complies with:
- EU REACH: Phthalate-free additives for chemical safety.
- US ASTM D5260: Validated UV and abrasion resistance.
- China GB/T 8946: Minimum tensile strength of 10 N/m².
4. Future Trends: Sustainability and Smart Packaging
4.1 Recyclable and Biodegradable Materials
VidePak’s recyclable PE/PP blends reduce carbon footprints by 35%, aligning with the EU’s Circular Economy Action Plan. Pilot projects with PLA-based liners aim for 90% compostability by 2026, targeting organic agriculture sectors.
4.2 IoT-Enabled Innovations
Integration of NFC tags allows real-time monitoring of environmental conditions (e.g., humidity, temperature), critical for pharmaceuticals. Coupled with Starlinger’s AI-driven looms, which dynamically adjust weave density, these advancements position VidePak at the forefront of Industry 4.0.
5. FAQs: Addressing Industry Concerns
Q: How do anti-static bags prevent explosions in chemical plants?
A: Conductive fibers and coatings dissipate static charges, complying with ATEX directives for hazardous environments.
Q: What grammage is ideal for construction materials?
A: 150–200 g/m² bags balance cost and durability, resisting abrasion from aggregates like barite sand.
Q: Can these bags withstand freezer storage?
A: Yes. Low-temperature PP resin maintains flexibility at -30°C, ideal for cryogenic storage.
Conclusion
Multi-wall woven bags are evolving from passive containers into active solutions for safety, efficiency, and sustainability. VidePak’s fusion of Austrian engineering precision, automation mastery, and regulatory compliance solidifies its role as a leader in the $8.3 billion global packaging market.
External Resources:
- Discover how multiwall laminated woven bags ensure safety.
- Explore automated form-fill-seal systems revolutionizing packaging efficiency.