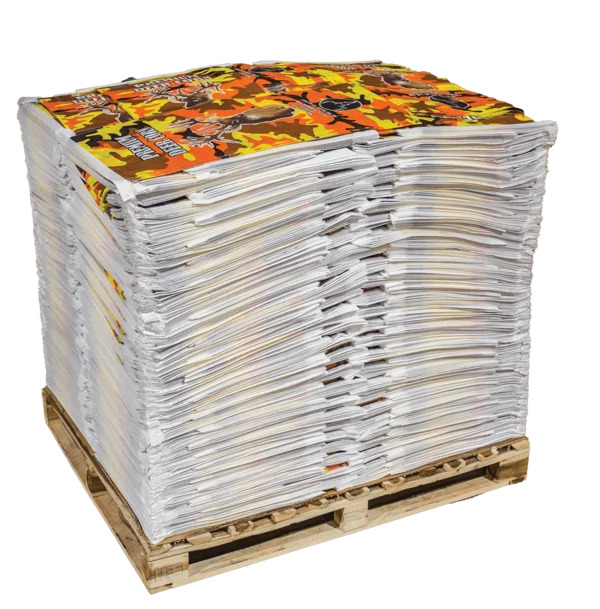
Packaging has always been a vital element in the supply chain. Whether it’s for protecting products during transport, providing critical information to consumers, or offering eco-friendly solutions, packaging plays a key role in many industries. Over recent years, advances in packaging materials and techniques have significantly enhanced both functionality and sustainability. Among the various options, jumbo bags (also known as FIBC or bulk bags) and advanced printing techniques have emerged as game-changers in packaging solutions.
In this article, we will explore how these innovations are shaping the packaging industry, particularly for large-volume products, and how advanced printing technologies further enhance their functionality.
What are Jumbo Bags?
Jumbo bags, or FIBC (Flexible Intermediate Bulk Containers), are large woven polypropylene bags designed to carry heavy or bulk goods. They are widely used in industries such as construction, agriculture, chemicals, and food products for storing and transporting materials such as grains, cement, sand, and even liquid products.
The appeal of jumbo bags lies in their strength, flexibility, and cost-effectiveness. These bags are made of woven polypropylene, which ensures durability, making them ideal for heavy-duty applications. They come in various sizes and can hold up to several tons of material, making them highly efficient for bulk storage and transport.
Key Features and Benefits of Jumbo Bags:
- Large Capacity: Jumbo bags can hold between 500 kg to 2,000 kg of product, making them perfect for bulk storage.
- Durable: Manufactured using woven polypropylene fabric, they are incredibly resistant to abrasion and can withstand rough handling.
- Customizable: They can be tailored to specific needs, with various design features such as lifting loops, discharge valves, and different closure types.
- Eco-friendly: FIBCs are reusable and recyclable, making them a more sustainable packaging option compared to other traditional materials.
Below is a breakdown of typical jumbo bag specifications:
Specification | Detail |
---|---|
Material | Woven polypropylene (PP) |
Capacity | 500 kg to 2,000 kg |
Dimensions | Varying sizes; typically 90x90x110 cm |
Weight | 1.5 kg to 5.5 kg |
Closure | Open top, valve, or duffle closure |
Lifting System | 4 corner loops, 2 loops, or 1 loop |
Design | Customizable sizes, prints, and labels |
The Role of Advanced Printing Techniques
While the core function of a jumbo bag is to carry bulk goods efficiently, the application of advanced printing techniques adds significant value. Printing on jumbo bags not only enhances their branding potential but also allows manufacturers to add critical product information, safety instructions, and regulatory compliance marks.
In recent years, there have been several advancements in printing technologies, such as flexographic printing and digital printing, that enable more detailed, vibrant, and customizable designs on jumbo bags. Let’s take a closer look at these techniques:
1. Flexographic Printing
Flexography is a highly efficient printing method that uses flexible plates to apply ink on various materials. It is commonly used for printing on woven bags. This technique is capable of producing high-quality prints with fine details and vivid colors.
- Key Benefits:
- Suitable for large-scale runs of bags.
- Can produce multi-color designs on woven bags.
- Fast drying time for high-volume production.
- High precision for clear, sharp designs.
2. Digital Printing
Unlike flexographic printing, digital printing involves printing directly onto the surface of the material using inkjet technology. This method is more flexible for short-run, high-definition designs.
- Key Benefits:
- Excellent for high-definition designs, gradients, and photographic images.
- No need for plates or screens, reducing setup time and costs for short orders.
- Eco-friendly ink options are available.
- Ideal for low-volume, custom orders with complex graphics.
The combination of jumbo bags’ bulk capacity and the visual appeal of advanced printing techniques makes them an attractive choice for companies that want to enhance their product presentation and improve logistics. For example, in the food industry, printed jumbo bags can include essential nutritional information, brand logos, and even eco-friendly messages to highlight sustainability.
Current Trends in Jumbo Bags and Advanced Printing
As industries continue to evolve, several trends are shaping the future of jumbo bags and advanced printing techniques:
1. Sustainability
The growing focus on sustainability has pushed manufacturers to adopt eco-friendly practices. More companies are opting for recyclable and biodegradable options for jumbo bags. This is where transparent woven bags and kraft paper laminated woven bags are gaining traction, as they offer an eco-conscious alternative to traditional plastic bags.
For example, Kraft paper laminated woven bags are an excellent solution for industries looking to reduce plastic usage. These bags provide the same strength and durability as polypropylene bags, but they come with a more natural, eco-friendly appeal.
2. Customization for Branding and Functionality
With advanced printing techniques, customization options for jumbo bags have skyrocketed. Custom prints allow companies to align packaging designs with branding goals, which helps improve customer recognition. For instance, in industries like agriculture or food production, bags can be printed with unique logos, color schemes, and product information to stand out on retail shelves.
3. Technological Integration
New technologies like QR codes or RFID tags can be integrated into the designs of jumbo bags. These technologies enhance traceability and provide additional layers of functionality in supply chains. For example, embedding a QR code into a jumbo bag print can allow customers to quickly access important information, such as product origin, specifications, or safety guidelines.
FAQs
1. How much weight can a jumbo bag carry?
Jumbo bags can typically carry from 500 kg to 2,000 kg, depending on their design and material specifications. Some customized bags can hold even more, depending on the intended application.
2. What materials are used to make jumbo bags?
Jumbo bags are primarily made from woven polypropylene (PP), which provides strength and flexibility. Some variations include laminated fabrics or kraft paper for enhanced durability and eco-friendliness.
3. Are jumbo bags recyclable?
Yes, FIBC bags are recyclable. They are often reused several times before they are recycled. The material used for production, polypropylene, is widely accepted in recycling programs around the world.
4. How does flexographic printing differ from digital printing?
Flexographic printing uses flexible plates to apply ink to the surface, making it ideal for high-volume production. Digital printing, on the other hand, directly applies ink to the material using digital technology, allowing for high-definition prints and greater flexibility for short runs.
5. Can I customize my jumbo bags with my logo or design?
Absolutely. Advanced printing techniques like flexography and digital printing allow for full customization, including logos, safety information, and vibrant designs.
Conclusion
As industries continue to adapt to consumer demands and sustainability goals, the role of jumbo bags and advanced printing techniques in packaging solutions has become more vital than ever. Jumbo bags, with their large capacity, durability, and eco-friendly options, are an excellent solution for bulk packaging, while advanced printing enhances their branding and informational capabilities. Whether you’re in agriculture, chemicals, or retail, understanding the advantages of these innovations will help streamline your operations and boost your market presence.
For more insights into how packaging solutions are evolving, check out this article on the versatility of woven bags and how they meet global market demands through customization and quality control here.
Similarly, for a deep dive into the benefits of Kraft paper woven bags, explore our article on kraft paper laminated woven bags here.