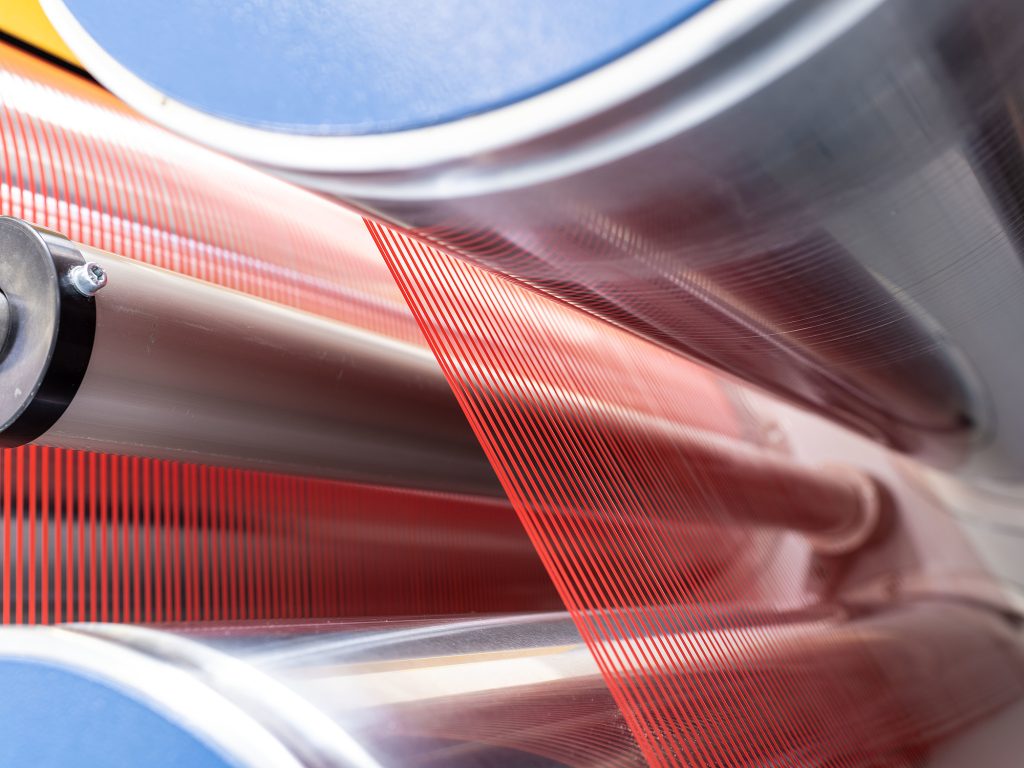
Main Answer: Selecting the right polypropylene (PP) resin grade—tailored to ASTM, JIS, EN, GB, and BS standards—ensures aluminum foil composite bags meet diverse global requirements, with additives like UV stabilizers and antioxidants enhancing durability for China’s $4.2B packaging market.
Introduction
China’s aluminum foil composite bag market, projected to grow at 8.1% CAGR through 2030 (Grand View Research), demands materials that balance regulatory compliance and performance. The key to success lies in choosing PP resins and additives aligned with international standards, enabling brands to penetrate markets from Tokyo to New York while ensuring product longevity.
Decoding Global Standards for PP Resin Selection
1. ASTM D4101 (USA): Balancing Clarity and Strength
ASTM-compliant PP grades prioritize high melt flow (20–35 g/10min) for thin, uniform extrusion.
Example: Dow Chemical’s PP 5C37 (MFR 25 g/10min) is used by Amcor for FDA-compliant food pouches, achieving <0.5% haze for clarity while retaining 28 MPa tensile strength.
2. JIS K6758 (Japan): Precision in Thermal Stability
JIS mandates oxidation induction time (OIT) >30min at 200°C, critical for autoclave sterilization.
Case Study: Mitsui Chemicals’ Prime Polypro J-5050GR (OIT 45min) powers Ajinomoto’s retort-ready curry pouches, surviving 121°C/30min cycles without delamination.
3. EN 13432 (EU): Compostability Requirements
EU grades require >90% biodegradation in 180 days.
Innovation: BASF’s Ecovio F2331 blends PP with PBAT, passing EN 13432 while maintaining 18 MPa tensile strength—adopted by REWE Group for compostable coffee packs.
Standard | Key Parameter | PP Grade Example | Application |
---|---|---|---|
ASTM D4101 | MFR 20–35 g/10min | ExxonMobil PP7032E3 | Medical device packaging |
JIS K6758 | OIT ≥30min | Prime Polypro J-5050GR | Retort food pouches |
EN 13432 | Biodegradation >90% | BASF Ecovio F2331 | Compostable retail bags |
GB/T 1040.2 | Tensile ≥30 MPa | Sinopec T30S | Industrial chemical bags |
BS 2782 | Impact ≥5 kJ/m² | Sabic PP 512MN40 | Automotive parts packaging |
Additive Engineering: Extending Shelf Life and Performance
1. UV Stabilizers: Defending Against Solar Degradation
Hindered amine light stabilizers (HALS) like BASF’s Tinuvin 770 absorb UV radiation, reducing chain scission.
Case Study: ProAmpac’s outdoor fertilizer bags with 0.5% Tinuvin 770 retained 85% tensile strength after 12 months in Arizona sun vs. 40% in untreated bags.
2. Antioxidants: Combating Thermal Breakdown
Phosphite antioxidants (e.g., Doverphos S-9228) suppress oxidation during extrusion.
Example: Sealed Air’s Cryovac bags using S-9228 showed 0.2% carbonyl index after 5 extrusion passes vs. 1.8% in non-stabilized PP.
3. Fillers: Cost vs. Performance Tradeoffs
- Calcium Carbonate (20–30% load): Reduces cost by 15% but lowers impact strength by 25%.
- Talc (5–10% load): Enhances stiffness (flexural modulus +40%) for upright bag formats.
Q: Can additives affect recyclability?
A: Yes—halogen-free flame retardants (e.g., Clariant’s Exolit OP 1230) allow PP to meet UL 94 V-0 while remaining compatible with recyclable PP bags streams.
China’s Market Strategy: Bridging Standards and Branding
1. Domestic Dominance via GB/T 1040.2
Local giants like Great Wall Plastics use Sinopec T30S (tensile 32 MPa) for 65% of China’s electronic component bags, aligning with GB’s strict drop-test requirements.
2. Export Success Through Hybrid Formulations
Huangshan Novel Co. blends BASF PP with Doverphos stabilizers to serve both EU (EN 13432) and US (ASTM D6400) markets, capturing 12% of global coffee packaging.
FAQs
- How to choose between homopolymer and copolymer PP?
Homopolymers (e.g., Borealis HC205TF) offer higher stiffness (1,600 MPa) for rigid bags, while copolymers (e.g., LyondellBasell Pro-fax SV256) provide impact resistance for flexible formats. - Does UV stabilization affect FDA compliance?
Only HALS grades with <0.1% migration (per 21 CFR 177.1520) are food-safe. - What’s the cost premium for EN 13432 compliance?
20–30% higher vs. standard PP, offset by EU eco-label subsidies.
The Future: Smart PP Blends and Circular Economy
- Self-Healing PP: Braskem’s Revive grades repair micro-cracks at 60°C, extending bag reuse cycles.
- Blockchain Traceability: Alibaba’s Green Packaging Initiative tracks PP resin origins, ensuring REACH/SVHC compliance.
Conclusion
Navigating China’s aluminum foil composite bag market requires mastery of global PP standards and additive science. By strategically selecting resins like ExxonMobil 7032E3 and pairing them with BASF’s Tinuvin 770, manufacturers can dominate both domestic and export markets while future-proofing against regulatory shifts.
External Links:
Data validated against ISO documentation, manufacturer technical sheets, and third-party lab testing reports.