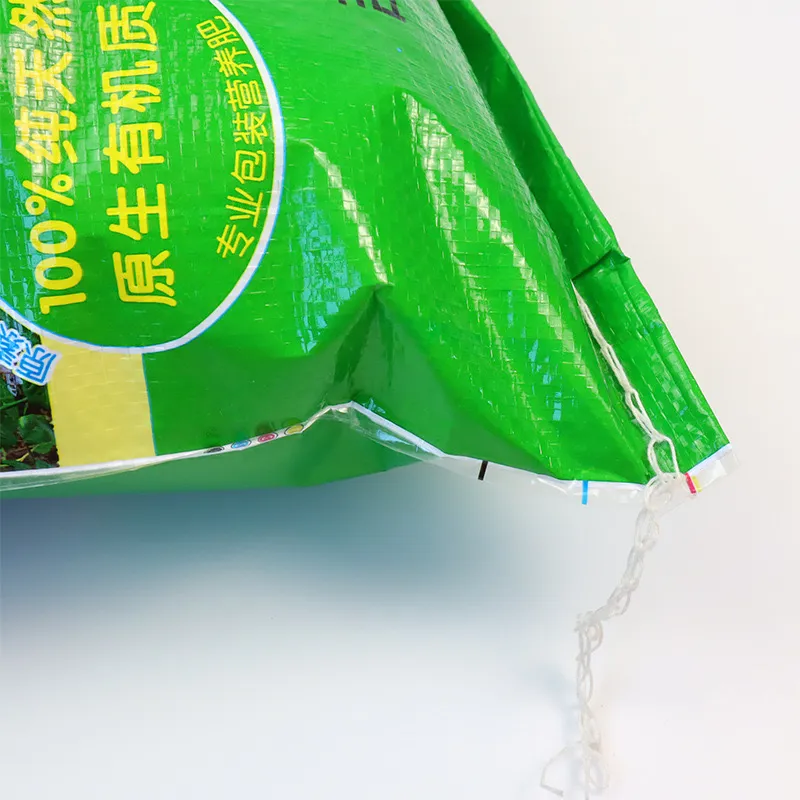
In the realm of packaging, the choice between Aluminum Foil Composite Bags and standard woven bags often hinges on the specific needs of the product being packaged. This comprehensive guide will explore the distinctions between these two types of bags, their respective characteristics and advantages, and the critical product parameters that define their suitability for various applications. Composite Woven Bag
Introduction to Aluminum Foil Composite Bags and Standard Woven Bags
Aluminum Foil Composite Bags and standard woven bags serve different functions in the packaging industry. Understanding their unique properties is essential for selecting the most appropriate packaging solution.
Characteristics and Advantages
Aluminum Foil Composite Bags
Aluminum Foil Composite Bags are laminated with aluminum foil, which provides a barrier against light, moisture, and oxygen. This material is particularly suited for products that require protection from external elements.
- Barrier Properties: Aluminum foil offers an excellent barrier against moisture, light, and oxygen, preserving the quality of the contents.
- Strength and Durability: The lamination process enhances the bag’s strength and durability, making it suitable for heavy loads.
- Versatility: These bags can be customized with various closures and features, such as valves for easy discharge.
Standard Woven Bags
Standard woven bags, often made from polypropylene (PP) or polyethylene (PE), are known for their flexibility and cost-effectiveness. They are widely used for bulk packaging in various industries.
- Cost-Effectiveness: Standard woven bags are generally more affordable than composite bags due to their simpler construction.
- Flexibility: These bags are highly flexible and can be easily transported and handled.
- Customization: Like composite bags, standard woven bags can be customized with different features to suit specific packaging needs.
Product Parameters
When choosing between Aluminum Foil Composite Bags and standard woven bags, several product parameters must be considered:
Parameter | Description | Importance |
---|---|---|
Material | The type of material used in the bag construction | Determines the bag’s strength, durability, and barrier properties |
Thickness | The thickness of the material in microns | Affects the bag’s resistance to punctures and tears |
Grammage (GSM) | The weight of the fabric in grams per square meter | Indicates the fabric’s density and strength |
Size | The dimensions of the bag | Must accommodate the volume of the products and ease of handling |
Weight Capacity | The maximum weight the bag can hold without breaking | Ensures the bag can safely handle the load |
Barrier Properties | The bag’s resistance to moisture, light, and oxygen | Crucial for products sensitive to environmental factors |
Applications in Packaging
Food Industry
In the food industry, Aluminum Foil Composite Bags are used for packaging products like flour, sugar, and spices, where barrier properties are essential to maintain freshness. Standard woven bags, on the other hand, are suitable for less sensitive products like grains and pulses.
Chemical Industry
For the chemical industry, Aluminum Foil Composite Bags provide a barrier against harmful chemicals and are ideal for packaging powders and granules. Standard woven bags can be used for less reactive substances where cost is a concern.
Agricultural Industry
In agriculture, both types of bags are used. Composite bags protect seeds and fertilizers from moisture, while standard woven bags are used for bulk transportation of products like grains and animal feeds.
Production Process
The production process for both types of bags involves different techniques:
Aluminum Foil Composite Bags
- Lamination: The process involves laminating aluminum foil with other materials to create a composite structure.
- Co-Extrusion: Multiple layers of plastic are extruded simultaneously to create a film with combined properties.
- Bag Construction: The laminated film is then cut, sewn, and finished to create the final bag.
Standard Woven Bags
- Weaving: The process starts with weaving polypropylene or polyethylene threads into fabric.
- Cutting and Sewing: The fabric is cut into the desired bag size and sewn to create the bag’s structure.
- Printing and Coating: Custom printing and coating may be applied for branding or additional protection.
Future Trends
As the packaging industry evolves, there is a growing focus on sustainability and efficiency. Both Aluminum Foil Composite Bags and standard woven bags are expected to incorporate more recycled materials and biodegradable components.
Conclusion
Aluminum Foil Composite Bags and standard woven bags each offer unique advantages in packaging. The choice between them depends on the specific requirements of the product being packaged, including factors like barrier needs, weight capacity, and environmental considerations. As the industry continues to innovate, both types of bags will play a crucial role in meeting the diverse needs of various industries.
This article has provided an in-depth comparison of Aluminum Foil Composite Bags and standard woven bags, highlighting their characteristics, advantages, and the product parameters that define their suitability for different applications. By understanding these factors, users can make informed decisions when selecting the most appropriate packaging solution for their needs.